Even if permanent corrective actions are implemented in step D5, there is no guarantee that the problem will not reoccur without appropriate preventive actions to address the root cause and prevent recurrence.
In the context of the 8D report, this possibility is addressed in step D7, which is dedicated to preventive actions.
D7 Preventive Actions – Basic Information
When defining a strategy in step D7, it is crucial to ensure that corrective actions not only prevent the same problem from recurring in the production of a specific product but also address:
- All final products manufactured under the same or similar conditions. This may include production cells, processes, materials, production lines, or technologies.
- Other products with a similar design or belonging to the same product family, such as window lifters with similar construction but designed for different car models or customer plants.
- Future projects to be launched at the supplier’s production facility.
- Systemic gaps that allowed the problem to escape detection at the next step of the production process and be identified by the customer. This includes not only direct customers but also reports from the warranty field.
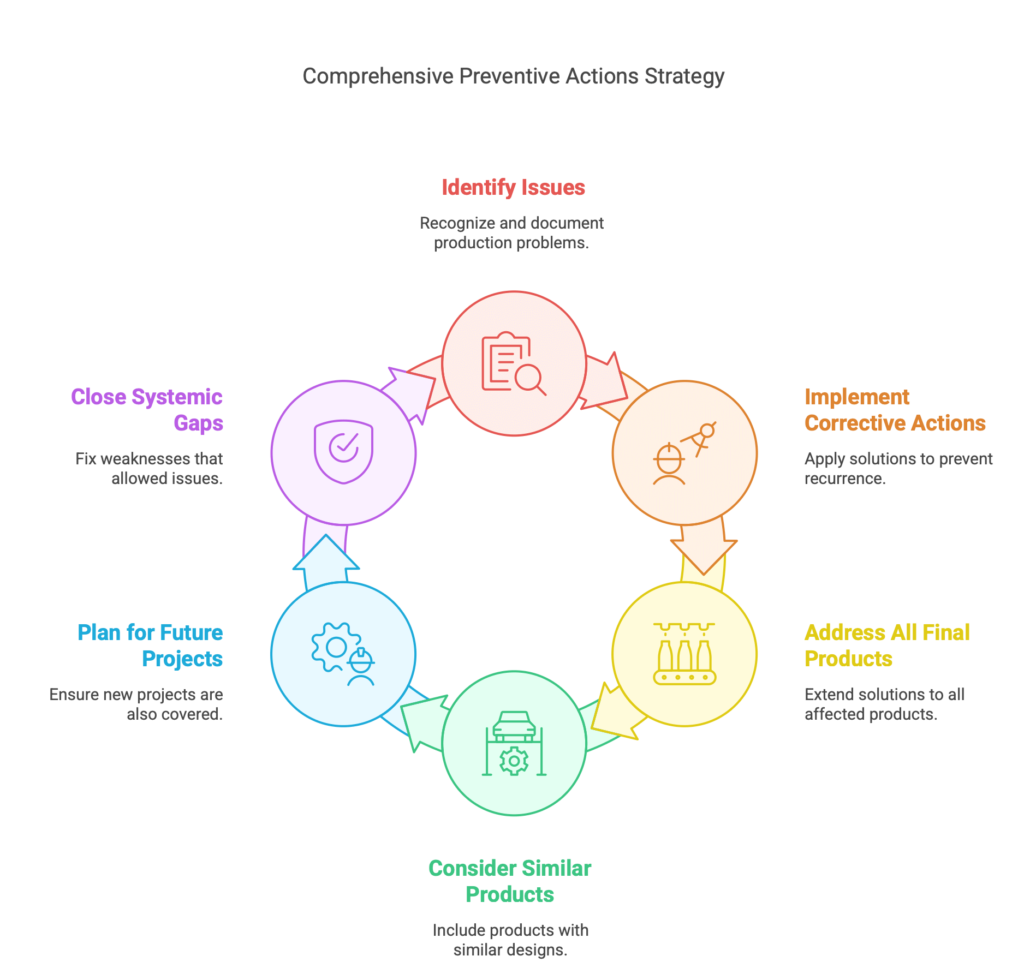
Communication During Implementation
Effective communication is a key element in implementing preventive actions. To ensure success, the following rules should be observed:
- Inform all interested personnel about the planned actions. For shift-based work, communication must cover all shifts.
- Discuss actions in daily management meetings to allocate resources appropriately.
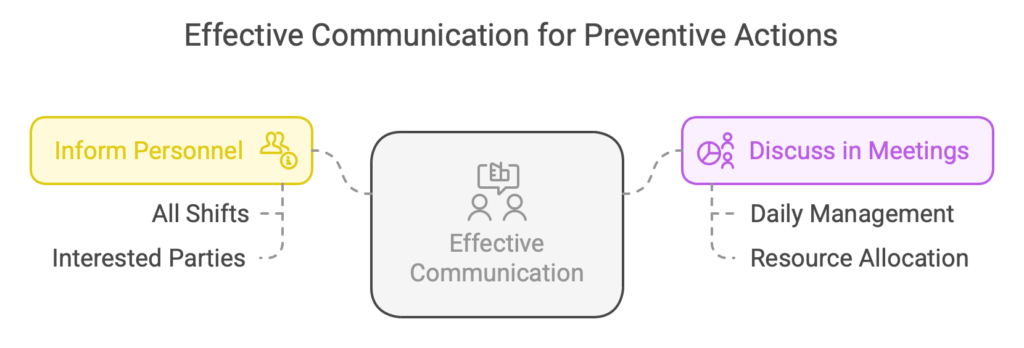
Examples of Preventive Actions
In addition to the frequent practice of updating the Control Plan and PFMEA, various other preventive actions can help prevent problem recurrence, including:
- Updating visual master samples.
- Revising changeover instructions for production or maintenance operators.
- Updating Flow Charts.
- Modifying LFMEA (Logistics Failure Mode and Effects Analysis) if the problem is related to improper handling or storage of sub-components or final products.
- Incorporating lessons learned into the database for use in Flow Charts, DFMEA, and PFMEA for new projects (see Fig. 1).
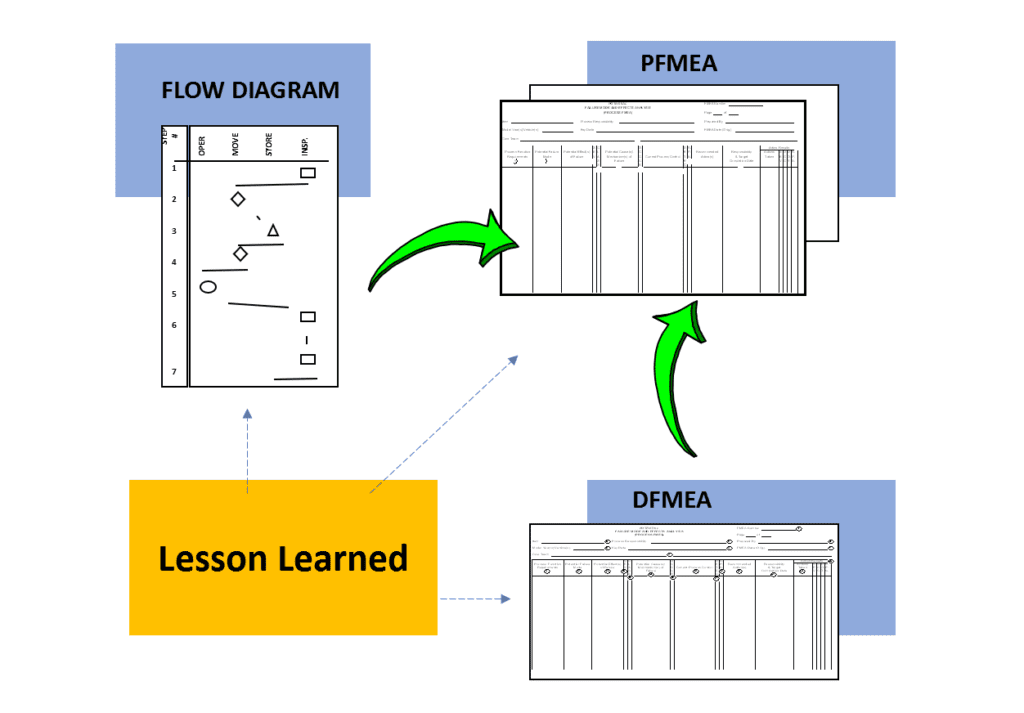
- Adjusting tolerances for Voice of Customer (VoC) or Voice of Process (VoP) requirements. For example, reducing internal scrap by narrowing process tolerances.
- Revising drawings for sub-components and finished products.
- Modifying incoming inspection controls, including measurement methods, frequency, and sample sizes. For instance, selecting one part per cavity (e.g., all eight cavities) is more effective than randomly selecting five parts.
- Creating or updating boundary samples or failure catalogs.
- Improving packing instructions for finished products.
- Clarifying selection instructions for handling non-conforming parts, to prevent damage during selection or improper repackaging.
What Happens if We Don’t Implement Preventive Actions?
Failure to implement preventive actions can lead to serious consequences for the supplier. Consider the following example:
A plant producing metal structures for seats transferred a stamping mold used for another model from abroad. Production initially ran smoothly. However, after the first scheduled maintenance by the plant’s staff, the customer reported an issue with backrest noise.
The analysis revealed that this problem had existed in the previous plant and was resolved by modifying the height of one die element in the stamping mold.
The fundamental failure in this case was the absence of preventive actions planned in step D5. This included updating the drawing documentation for both the seat structure element and the stamping mold.
Additional Resources
You can download an automatic, editable Excel form for free on Free Quality Tools.
Document name: 8D Report – Excel Form
Author: Dariusz Kowalczyk