Companies supplying components to the automotive industry must be aware that, in addition to production intended directly for the customerβs production plants (0-km), they are often required to produce service parts related to automotive warranty management.Β The IATF requirement that addresses this is point 10.2.5 “Warranty Management Systems”, which not only identifies the definition of NTF (No Trouble Found) but also outlines additional customer-specific requirements, such as those described in the VDA FFA manual.
For German customers, these requirements are detailed in the following documents:
- VW Group: Customer-Specific Requirements, referenced in IATF 10.2.5, directly addressing the implementation of NTF using the VDA FFA manual.
- BMW: Standard GS 95004 – “Failure Analysis – Part Analysis of Field Complaints.”
- Daimler: MBN 10448 – βField Failure Analysis.β
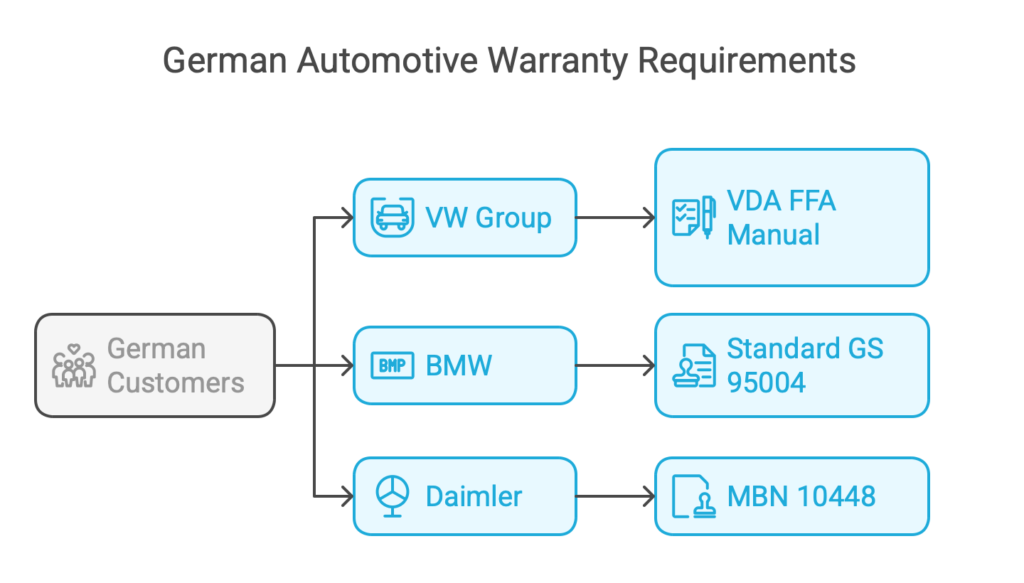
It is also important to note that both BMW and Daimler specify the possibility of field returns process auditing. These audits are typically conducted at the production plant by customer representatives. To proactively address this, organizations should consider integrating an FFA audit into their process audit framework, alongside the IATF requirement 9.2.2.3.
Warranty Issues and Responsibility Allocation
When addressing warranty issues, liability is determined after analyzing the root cause of the defective part. Liability is typically divided into the following areas:
Design Responsibility:
- For example, in the VW Group, if the organization is responsible for the design (co-design), the KVV (cost distribution factor) ranges from 10% to 90%.
- If the design is provided by the customer, the KVV is reduced to 20%-30%.
- Other configurations may apply, depending on contractual agreements.
Manufacturing Responsibility:
- If the root cause is directly linked to production process non-compliance, the organization bears 100% of the costs.
Instruction Responsibility:
- This addresses whether the organization has conducted preemptive meetings with the customer to clarify proper part handling procedures. For instance, mishandling (e.g., holding wires improperly) can cause electrical faults.
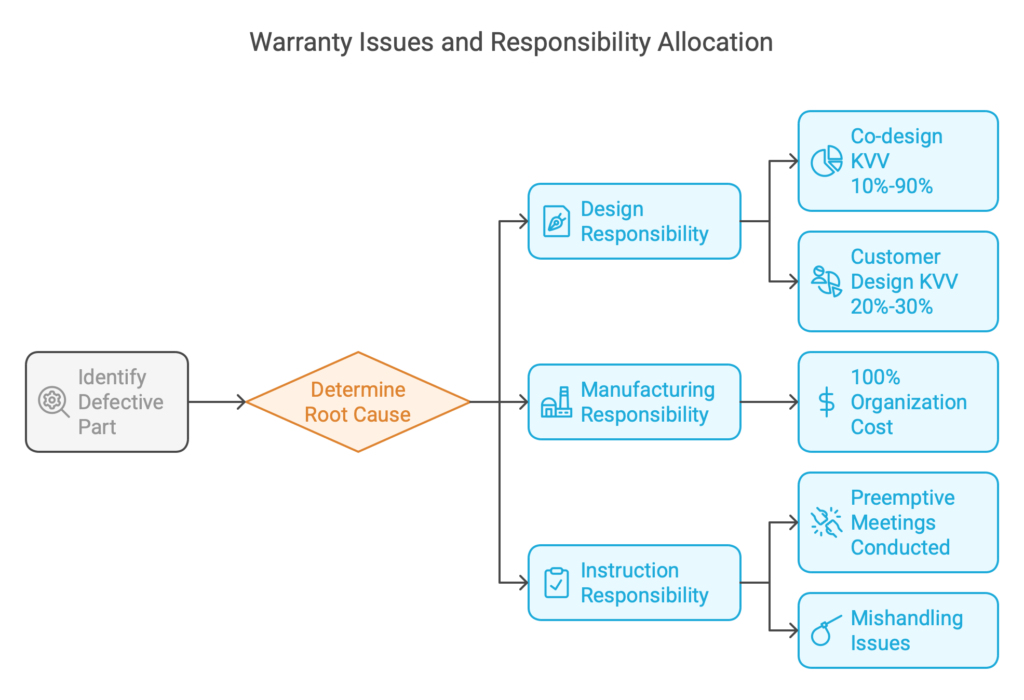
Such requirements are often included in the MLA process (level 5), as outlined in section 5.4.1, and must be discussed and agreed upon with the customer.
When to Start Planning the VDA FFA Process?
Activities related to warranty part analysis should begin during the pre-launch phase, particularly when conducting MLA (depending on the project’s risk classification: A, B, or C). For projects with higher risks, the client may perform an audit based on VDA 6.3, covering sections 2, 3, and 4.
- Sections 3 and 4 include questions on process planning for warranty return analysis and its implementation (points 3.4 and 4.7, respectively).
- During production, internal audits (conducted 1/12 months) should address question 7.4. It is equivalent to sections 6 and 7 of the FFA audit form.
Conclusion
Incorporating VDA FFA requirements ensures that organizations can effectively manage warranty returns, meet customer expectations, and proactively mitigate risks. Understanding and integrating these standards into your quality management processes is key to maintaining competitive performance in the automotive industry.
Download our free ebook Automotive Warranty Management – Practical Guideline for Suppliers