The VDA 6.3 process audit is a standard developed by the German Association of the Automotive Industry (Verband der Automobilindustrie, VDA). It is widely used in the automotive sector to evaluate and improve processes within the supply chain.
Why is it so important in the automotive industry?
Thanks to its comprehensive structure, which we will explore further below, it plays a crucial role in ensuring high quality and compliance of processes with customer requirements. Additionally, it focuses on identifying risks within processes and implementing improvements to minimize them.
This enables companies to meet current requirements and prepare for future projects, especially in terms of meeting the expectations of potential OEM suppliers.
VDA 6.3 Process Audit – Structure and modules
The standard is divided into various modules that cover different aspects of the product lifecycle and process chain. These include project management, product and process development, supplier management, and serial production.
During the audit, specific process elements are evaluated. These are grouped into the following sections:
- P1: Potential Analysis β Assessment of a new, potential supplier. Conducted only during the initial evaluation of starting cooperation with a new client.
- P2: Project Management β Focuses on planning and monitoring projects to ensure their timely execution.
- P3: Planning the Product and Process DevelopmentΒ β Defines essential activities necessary for executing or planning a new project launch.
- P4: Implementation of theΒ Product and Process Developmentβ Summarizes actions required to confirm the organization’s production capability.
- P5: Supplier Management β Concerns the selection, evaluation, and monitoring of suppliers to ensure the quality of delivered components.
- P6: Process Analysis Production β Focuses on analyzing and optimizing production processes to ensure efficiency and quality.
- P7: Customer Care/ Customer Satisfaction/Service β Covers issues related to complaint handling, resource availability, and the competence of personnel in this area.
For internal process evaluation during current production, auditors typically assess the last three sections.
Questionnaire and Evaluation
The audit is conducted using a detailed questionnaire, which helps auditors evaluate various process aspects and assign appropriate ratings. The question layout includes minimum requirements for conducting the evaluation and examples of implementation that the organization can fulfill.
Based on the audit result, which appropriately assigns a grade of A, B, or C, companies can identify areas needing improvement or optimization and implement corrective actions.
Benefits of VDA 6.3
The VDA 6.3 process audit is a tool that offers numerous benefits for companies in the automotive industry.

Its application allows for:
Enhancing process quality capabilities
VDA 6.3 helps companies systematically evaluate and improve process quality. Through detailed audit guidelines, organizations can identify and eliminate potential defects and optimize their processes, leading to higher product quality, fewer complaints, and less potential escalation from customers.
Risk identification and management
The standard focuses on identifying risks in processes and implementing preventive measures. This allows for better risk management and minimization of potential problems, increasing the stability and reliability of production processes.
Improving customer relationships
By applying VDA 6.3, companies can better meet customer requirements, leading to increased customer satisfaction. Automotive industry clients often require VDA 6.3-compliant audits, so conducting them can improve business relationships and increase customer trust.
Process standardization
VDA 6.3 provides a uniform approach to auditing processes throughout the supply chain. This facilitates communication and cooperation between different departments and business partners, leading to more consistent and efficient processes.
Supporting continuous improvement
The questionnaire structure promotes a philosophy of continuous improvement and includes elements of lean philosophy. Regular audits help companies systematically identify areas for improvement, eliminate inefficiencies, and waste, leading to better resource utilization, cost reduction, and productivity improvement.
Strengthening organizational culture
Applying the VDA 6.3 standard can help strengthen the quality culture within the organization. Engaging employees in the audit and process improvement process increases their awareness and builds internal commitment.
Are there any drawbacks to the VDA 6.3 Process Audit?
As with any industry practice, there are pros and cons. The main disadvantages include:
Complexity and cost of the audit
The comprehensive structure of the VDA 6.3 audit requires significant resources, both human and financial. The detailed questionnaire and necessity for thorough analysis of all process aspects can be time-consuming and costly, especially for small and medium-sized enterprises.
High competency requirements
Conducting an audit according to VDA 6.3 requires highly qualified auditors with in-depth knowledge of the standard and automotive industry specifics. Finding suitably qualified specialists can be challenging, and their training may be expensive, especially if clients require auditors to have VDA QMC licensed training.
Limited flexibility
The detailed and rigorous nature of the VDA 6.3 standard may limit a company’s flexibility in adapting processes to its specific needs. Some organizations may find the standard imposes too many formal requirements that are not always adequate to their specifics and actual needs.
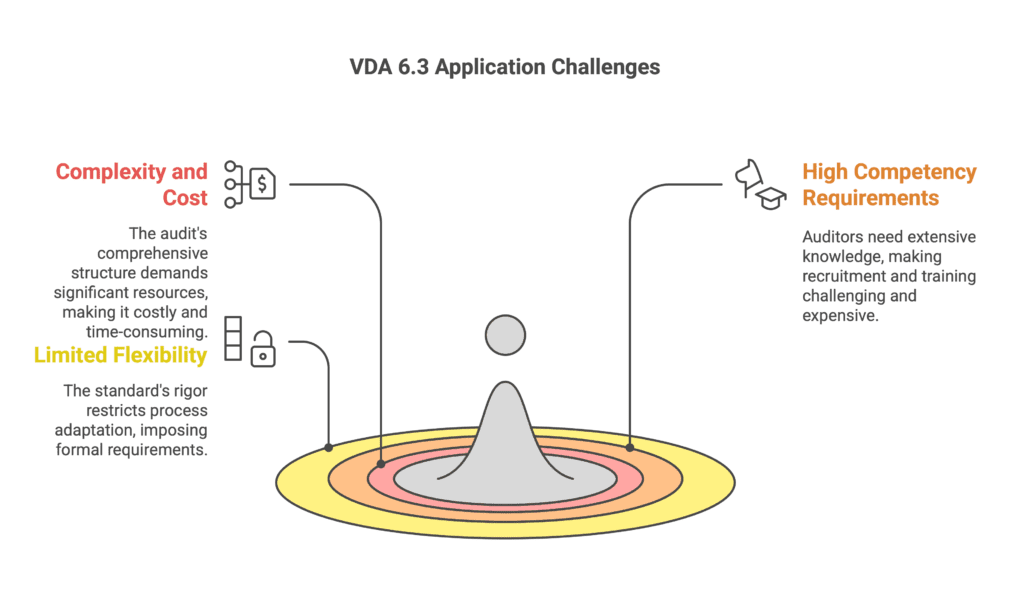
Conclusion
The VDA 6.3 Process Audit is a tool that enables automotive industry companies to ensure high quality of their processes and continuous improvement.
Regular audits and the successive implementation of recommendations contained in the standard allow companies to effectively manage risk, increase the efficiency of their operations, and gain a competitive advantage in the market, which certainly contributes to improving the business results of the organization.
Kinga Niedziela
Source:
1. VDA 6.3 Process Audit, 4th Edition, January 2023