Approving production parts according to VDA 2 is a crucial element of quality assurance in the automotive industry. This procedure, developed by the German organization VDA (Verband der Automobilindustrie), aims to standardize the production and product approval process.
Additionally, it ensures that the supplied parts meet the established quality, quantity, and timing requirements.
PPA procedure according to VDA 2
Organizations use the PPA (Production Process and Product Approval) procedure to approve production processes and final products.
This process is documented and standardized throughout the supply chain, ensuring uninterrupted deliveries in the agreed quality, quantity, and time, using the approved serial process.
The PPA procedure applies to various types of products, including:
- Final products delivered to the customer for assembly
- Service parts delivered to distribution centers
- Production materials
- Software as a product or part of a product
- Production parts launched for a new project
- Design changes, also known as engineering changes
- Reuse of currently produced parts for new projects in the same or different location, referred to as “carry over” in the automotive industry. You can also find a separate article on this topic on our blog.
- Specific customer requests arising from different scenarios during current production
PPA agreement
The client and supplier must agree on the scope, content, and schedule of the PPA procedure. This agreement includes:
- Input conditions: approved specifications, drawings, and standards
- Terminology and delivery plans
- Number of checked and delivered sample parts for evaluation
- Scope of customer approval
- Locations for sample parts delivery
- Optional software evidence
- How measurements and controls are conducted
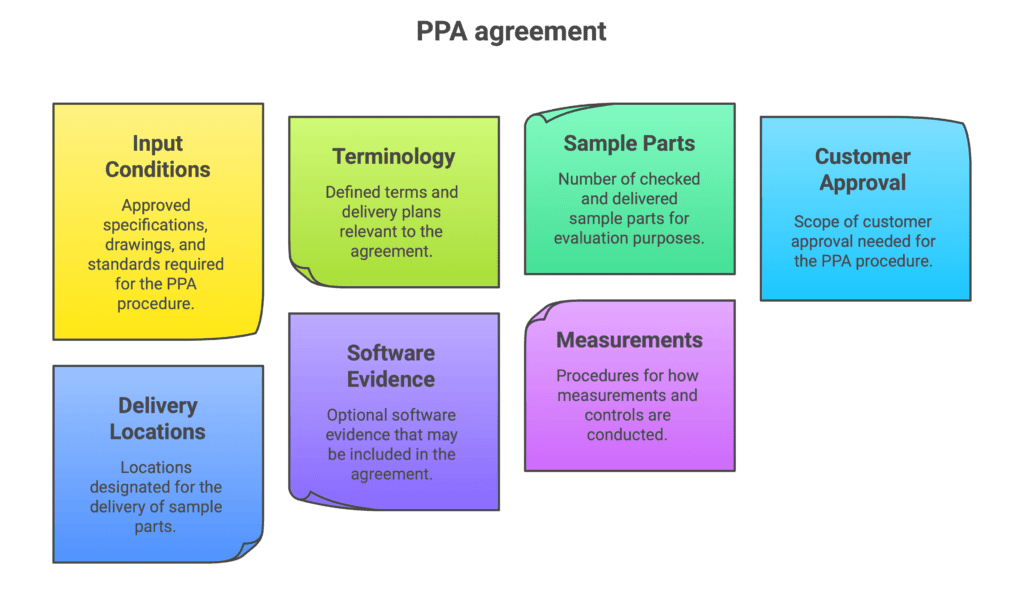
In the PPA agreement, the organization and the client determine the scope of the PPA documentation (number of attachments).
Considering the risks defined during the project, the client will appropriately define the scope, content, and schedule for submitting documentation. The more innovative the project scope for the supplier (product, process, technology, supply chain), the higher the risk for the client.
Therefore, the number of necessary documents for submitting and confirming full process and product capability increases. This rule also applies in the opposite case. Why? Let me explain.
If the supplier has been verified in previous projects, it carries less risk for the client. As a result, the number of necessary attachments according to the PPA procedure decreases.
Steps in the PPA procedure according to VDA 2
The PPA procedure includes several key stages:
Agreements and planning
The organization and client establish input conditions, including specifications, drawings, standards, packaging instructions, and deadlines. The team should document the results of the PPA procedure agreements.
Production process approval
Documenting compliance with specified quality and production requirements, including performance tests, approves the production process. The organization and client agree on the timing and scope of quality and performance evidence.
Product approval
The supplier must produce products under target serial production conditions and meet all specified functional and dimensional requirements.
Conducting the PPA procedure with the client
Documentation and sample parts are submitted to the client, who, based on the provided evidence, decides on the approval of the product and production process. The supplier and the client must agree upon the number of samples to be delivered.
Dimensional Control and Functional Tests
Regular dimensional controls and functional tests are necessary to maintain the continuity of meeting requirements in serial production. The organization and the client should agree upon the frequency, type, and scope of dimensional controls and functional tests. These should be summarized in the PPA procedure agreement.
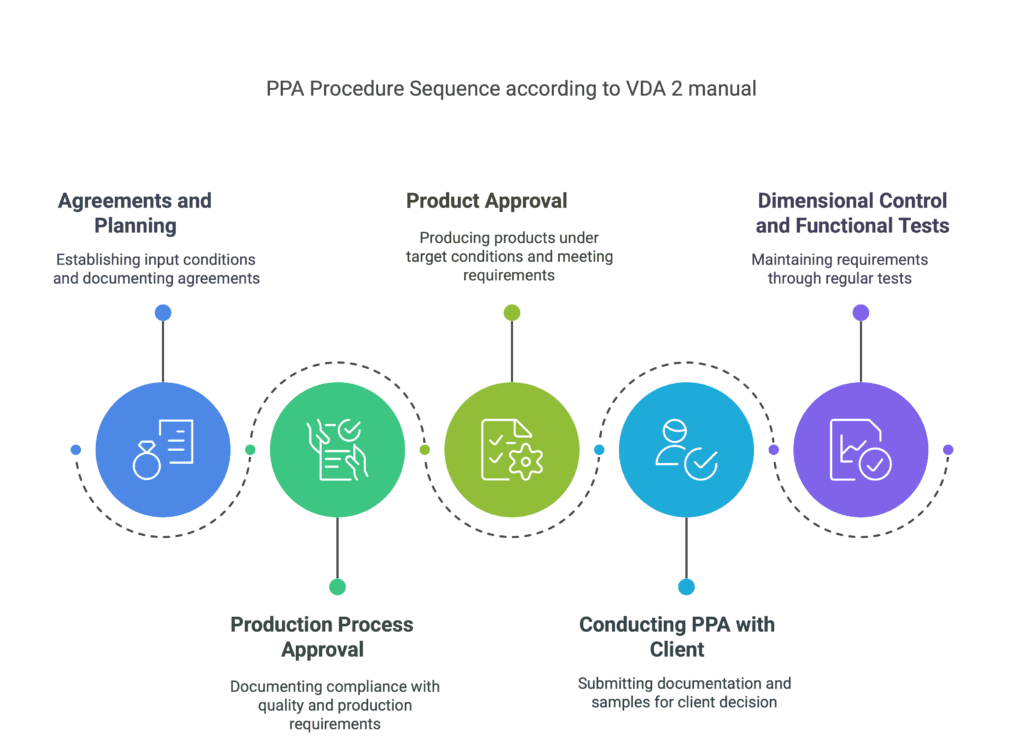
Common errors in preparing parts for evaluation according to VDA 2
One of the most common errors in the PPA procedure is failing to meet the formal requirements of the client, leading to delays in production approval. This often happens when organizations submit documentation according to the PPAP procedure instead of the PPA, as ordered by the client and found in the CSR.
Another difficulty that can lead to non-compliance in the PPA process is determining production capabilities. This scenario relies on Pp/Ppk and Cp/Cpk indices. They are often used interchangeably.
To correctly determine process capability, one must confirm the sampling method on which both indices should be calculated.. The client typically specifies the sample size and whether the capability is short-term or long-term.
Additional Considerations
Approval of product compliance for serial production can also occur based on an incorrect production trial. According to VW Group requirements, this should be the pre-check 2 phase, aiming to secure the process and volume to SOP and the complete serial process.
During one of the project implementation stages, the team should also determine production size and efficiency.
Additional errors in the PPA process often include outdated documentation or specifications used for product evaluation. This is a frequent error since changes in design often occur up to the start of production.
The client often reports the use of outdated documentation during the “Part history” document review. It turns out that the organization uses the wrong, old revision of the documentation, leading to the PPA documentation being revoked.
Sometimes, the lack of necessary attachments such as CP, FMEA, or Part history results in the client’s rejection of the PPA documentation.
Perhaps the biggest challenge in approving the process and product for serial production is neglecting the obligation to conduct an internal PPA procedure. Organizations focus on submitting documentation and confirming capability to the client, often forgetting to meet this requirement internally.
Evidence of non-compliance in this context, includes the complete absence of archived records in the organization and stored samples. Especially regarding the IATF 16946:2016 standard.
The examples above are common and highlight the importance of adhering to all VDA 2 guidelines and specific customer requirements.
Summary
Approving production parts according to VDA 2 is a comprehensive process requiring close cooperation between the supplier and the client. Following PPA procedures ensures that products meet high-quality standards. This is crucial for seamless production and delivery in the automotive industry.
If you want to learn more about part approval when working with German clients, we invite you to our training sessions.
VDA 2 – Production Process and Product Approval
Sources:
- VDA 2 – Quality Assurance of Supplies – Production process and product approval. 6th edition, April 2020