VDA 6.3 Process Auditor training agenda:
1. Purpose and scope of the VDA 6.3 manual
2. Schedule arrangements for process audits
3. Requirements and competencies for VDA 6.3 process auditors
4. VDA 6.3 process audit in relation to IATF requirements and Customer Specific Requirements
5. Evaluation criteria for collected audit evidence
6. Conditions for conducting audits
7. Implementation of the audit process
8. Discussion of individual audit sections:
- Potential Analysis (P1) as an Evaluation of a Potential Supplier
- Project Management (P2)
- Planning and Development of Product and Process (P3)
- Implementation, Development of Products and Processes (P4)
- Supplier Management (P5)
- Serial Production (P6)
- Customer Service, Customer Satisfaction (P7)
9. Post-Audit Actions
10. Audit Report – Preparing Documentation
Training addressees:
- Process Quality Engineers,
- Quality Management System Coordinators,
- Internal Process Auditors,
- Customer Quality Engineers,
- Supplier Quality Engineers,
- Supplier Development Engineers
Submit a request
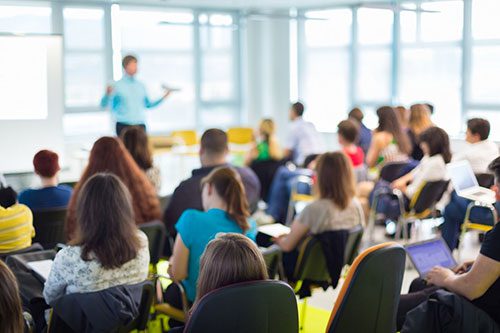
Training program
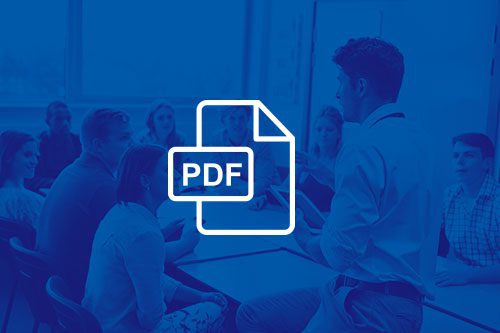
Automotive Quality Solutions
After finishing the VDA 6.3 process auditor training, participants will learn:
• Proper interpretation of requirements from the VDA 6.3 form, both for the pre-production sections (P1-P4) and current production (P5-P7).
• The relationship of the VDA 6.3 process audit in relation to IATF requirements and CSR’s.
• How to effectively conduct audits.
• Understanding of VDA 6.3 requirements – Completion of the training provides participants with a full understanding of the VDA 6.3 standard requirements for process audits. This enables effective implementation of these requirements in the organization and conducting process audits according to the latest guidelines.
• Improvement of process quality and efficiency – VDA 6.3 process audit training enables participants to learn effective analysis and assessment of processes to identify areas for improvement. This allows for implementing corrective actions that contribute to enhancing the quality, efficiency, and performance of processes within the organization.
• Risk minimization and problem prevention – Participation in the training helps in identifying and assessing potential risks associated with organizational processes. This enables the implementation of appropriate preventive actions that minimize the risk of problems occurring.
• Building customer trust – Proper ability to conduct process audits provides participants with the skills to conduct effective audits that meet the expectations of customers and business partners. This helps build trust by ensuring that the organization’s processes comply with high industry standards.
• Collaboration with suppliers – Knowledge of VDA 6.3 facilitates better collaboration with suppliers. Participants will be able to conduct effective internal and external audits, contributing to minimizing quality risks in the supply chain and ensuring supplier compliance.
• Enhancement of auditing skills – VDA 6.3 process audit training allows participants to develop auditing skills, including audit techniques, communication, data analysis, and reporting. This translates into more efficient and effective audits, leading to improved quality of processes and management systems.
Automotive Quality Solutions
Benefits for the company:
- Participants gain skills in analyzing and evaluating processes, identifying areas for improvement.
- With a deep understanding of VDA 6.3 requirements, participants can implement robust quality management systems. This results in higher product quality, fewer defects, and enhanced customer satisfaction, thereby maintaining a competitive edge in the market.
- Knowledge gained from the training enables employees to conduct effective audits, both internally and externally. This fosters better collaboration with suppliers, ensuring adherence to quality standards across the supply chain and minimizing risks associated with product quality and reliability.
Automotive Quality Solutions
Duration:
2 days
Price:
– 650 EUR for one participant
In case of 2 or more participants from the same plant offer 10% discount on the second and all other participants.
The invoice due date will be 30 days from the invoice issue date. The invoices for the services will be issued after the service delivery.
There is also possibility to organize in-house training sessions or internal online sessions for companies – for details, please get in touch with office.
On client demand there is a possibility of training extending with an additional workshop day.
Price include:
- Training participation
- Training materials
- Certificate
Check also our article VDA 6.3 Process Audit – Key steps to ensuring quality in the automotive industry