The CQI-12 training is led by an experienced practitioner and implementation specialist with over a decade of hands-on work in the automotive industry, supporting suppliers in meeting AIAG process assessment requirements. Thanks to his deep expertise, participants will gain not only a solid understanding of the CQI-12 standard for coating system assessments but also practical knowledge on implementation, audit preparation, and meeting customer expectations.
CQI-12 Training Agenda:
1. Customer Specific Requirements and IATF 16949:2016 Related to CQI
2. Overview of the CQI Standards Family and Characteristics of Special Processes
3. CQI-12: General Requirements
4. Auditor Competencies
5. Assessment of Key Aspects
6. Detailed Overview of the CQI-12 Standard
- Staff Responsibility and Quality Planning
- Responsibility for Warehouse and Material Handling
- Job Audit: Product Audit, Final Assembly Process Audit, and Packaging Audit
- In-Depth Review of Tables A–L
7. Practical Exercises and Case Studies
8. Training Summary
Target Audience for the Training:
Management:
-
Directors
-
Managers
-
Area Leaders
Specialist Staff:
-
Process Engineers
-
Quality Specialists
-
Quality Controllers
-
Maintenance Specialists
-
Personnel in direct contact with customer representatives
Submit a request
Training program
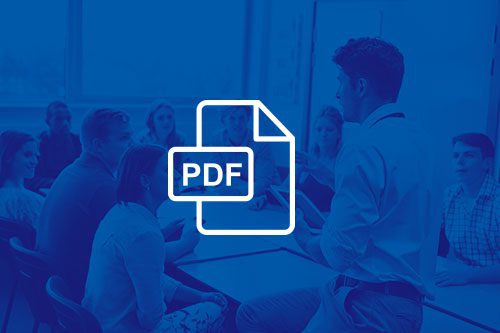
Automotive Quality Solutions
Benefits to the company:
Auditing in Compliance with AIAG CQI-12 Requirements
-
Managing Changes in Process, Quality, and Coating Documentation
-
Ensuring Proper Machine and Component Supervision to Maintain Production Continuity
Understanding Requirements and Standards
After completing the training, participants will be familiar with AIAG standards and requirements related to coating process assessment. They will accurately interpret procedures, techniques, and tools used to evaluate the quality of coating processes.
Effective Quality Process Assessment
The training enables participants to effectively assess the quality of coating processes in line with AIAG’s CQI-12 guidelines. They will learn to identify potential issues, defects, and deviations from standards, and determine appropriate corrective and preventive actions.
Minimizing Quality Risks
Upon completing the training, participants will be capable of minimizing quality risks associated with coating processes. With the acquired skills, they will detect potential non-conformities and errors, contributing to improved product quality and reduced costs related to complaints and repairs.
Enhancing Process Efficiency
Participants will learn how to identify areas for improvement and optimize the coating process. They will be able to implement innovations, new technologies, and best practices to increase process efficiency, shorten cycle times, and reduce production costs.
Improving Technical Skills
Participants will enhance their technical expertise in coating process assessment. They will learn advanced measurement methods, inspection techniques, data analysis tools, and result interpretation strategies.
Ensuring Compliance with Industry Requirements
Completing the training ensures participants can meet relevant industry requirements and quality standards. Proficiency in coating process assessment provides a competitive edge for the company.
Building Customer Trust
Solid knowledge of coating processes boosts customer and business partner confidence. Clients will trust that the company adheres to high-quality standards, leading to greater customer satisfaction.
Automotive Quality Solutions
Duration:
Duration: 1 day
Date of open training session:
24.10.2025 – online training
Price:
€400 per participant
For two or more participants from the same plant, a 10% discount applies to the second and each additional participant.
To organize in-house training sessions or internal online sessions for your company, please contact our office.
Invoices will be issued after the service is delivered. The payment due date is 30 days from the invoice issue date.
Price includes:
-
Participation in the training
-
Training materials
-
Certificate of completion
Also, check out our article on CQI-12 Coating System Assessment