8D Problem Solving Training
Agenda:
1. Steps of the 8D Analysis Process:
D0 – Preparation and Problem Statement
- Initial problem evaluation criteria
- Emergency Response Actions (ERA) – when to use them and what information is needed for validation
- Case study
D1 – Team
- Recommended team structure and roles
- Responsibilities of team members
- Methodology for conducting meetings
- Case study
D2 – Problem Definition (Using 5W2H and Is/Is Not)
D3 – Interim Containment Actions (ICA)
- Ensuring effectiveness in the context of customer safety
- Examples of actions implemented by the production plant and at the customer’s location
D4 – Root Cause Analysis
- Tools and documentation review
D5 – Identifying Corrective Actions
D6 – Implementation of Permanent Corrective Actions (PCA) and Effectiveness Assessment
D7 – Preventive Measures
- Examples of documents that need to be updated after a claim
- Difference between “Read Across” and “Lesson Learned”
D8 – Closing the Analysis and Team Recognition
2. Describing the Search for Causes of Nonconformity
3. Records of Actions Taken
4. Tools for Initiating Corrective and Preventive Actions
Ishikawa Diagram for:
- Why Happened (WH)
- Why Undetected (WU)
5 Whys:
- Correct transition between questions
- Case study
5W2H Analysis and “Is / Is Not” Method:
- Properly structured problem description
- Common mistakes made by teams
- Case study
5. Group Troubleshooting
- Building an interdisciplinary team
- Effective communication within the team
- Collaborative search for causes of nonconformity
Submit a request
Training program
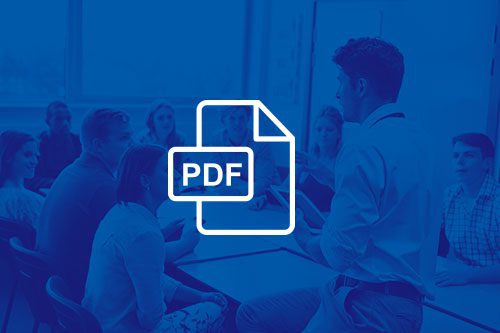
Automotive Quality Solutions
Thanks to the 8D Problem Solving training, participants will learn:
- How to document 8D activities
- Principles of effective team building
- Practical techniques for exploring root causes creatively
- How to distinguish between a symptom and a root cause during analysis
- Best practices for creatively identifying causes of nonconformity
- How to implement preventive actions (D7) to prevent problem recurrence
- Step-by-step approach to 8D methodology based on practical case studies
- How to properly describe a problem without jumping to conclusions
- Assessing the effectiveness of Interim Containment Actions (ICA) and Permanent Corrective Actions (PCA)
Automotive Quality Solutions
Duration:
- 1 day (7 hours)
Date:
June 23, 2025 – Online Training Session
Price:
287 EUR per participant
- A 10% discount applies to the second and all additional participants from the same plant.
- The invoice due date is 30 days from the invoice issue date.
- Invoices for services will be issued after service delivery.
Custom Training Options:
We also offer in-house training sessions and internal online sessions for companies. For details, please contact our office.
Price Includes:
✅ Training participation
✅ Training materials
✅ Certificate of completion
✅ 12 months of post-training consulting for participants
📥 Download the free eBook: 8D Problem Solving for Automotive Engineer