When starting cooperation with a Stellantis-FCA customer, each production plant should receive appropriate documentation from its engineering and sales departments.
Such documents will facilitate cooperation between the customer’s representative and the plant during the pre-launch phase and in current production.
Sourcing phase documentation
The first fundamental document that the production plant should receive from their sales department or program manager is
Quality Requirements for Suppliers (QRS) – PRO-00109. It’s important because:
- Is mentioned several times in the Stellantis-FCA customer specific requirements
- Determines the using of the following documents both in the pre-launch phase and current production:
- Additional Quality Requirement
- Basic Requirement Check List – this document is mentioned in two CSR’s and more information is stated also in FGP.39.
- Manufacturing Feasibility Assessment
- Verified by the customer’s representative (PPAP level 4 and 5) or by the production plant (PPAP level 1,2,3)
Sourcing Phase Documentation
The first fundamental document that the production plant should receive from its sales department or program manager is the Quality Requirements for Suppliers (QRS) – PRO-00109. It’s important because:
- It is mentioned several times in the Stellantis-FCA customer-specific requirements.
- It determines the use of the following documents in both the pre-launch phase and current production:
- Additional Quality Requirements
- Basic Requirement Checklist – This document is mentioned in two CSRs, with more information stated in FGP.39.
- Manufacturing Feasibility Assessment, verified by the customer’s representative (PPAP level 4 and 5) or by the production plant (PPAP level 1, 2, 3).
- The contract is not only sales department know-how.
This document contains the following relevant information for the production plant:
- IPTV warranty indicators targets (Incidents Per Thousand Vehicles) for the one-year and two-year period of car use by the final client.
- Warranty period applied for returns from the field analysis—usually a combination of the warranty period (often 24 months for the European market) and mileage.
- Service parts quantity [%] that must be added to the daily production dedicated to the first assembly in OEM plants. Most often, it is assumed to be 10%, but it’s worth verifying this provision in the contract each time.
- Cooperation with “Direct-Buy” sub-suppliers, selected by the customer to provide components to the production facility. Why is this so important? Because responsibility for launching such sub-suppliers (also known as Tier 2) during the pre-launch phase is managed by the customer, with the support of the plant representative.
- After the start of current production, full responsibility for the “direct-buy” sub-supplier indicated by the customer is transferred to the production plant. Of course, other agreements can be defined in the responsibility matrix, known as the RASI chart, as described below.
RASI Chart
It’s worth having this chart because it helps the production plant know which activities it is responsible for (R) and which are the client’s responsibilities. It also specifies who approves (A), supports (S), and who is informed (I) about planned and performed activities.
Organization Engineering
The R&D department (also known as Engineering or Product & Development) plays a crucial role in the documentation sourcing puzzle that is important for the production facility. They mainly provide:
- Product Card, which includes information on warranty indicators (also included in the contract) and the time period for revalidation tests, which are related to CSR for IATF 8.6.2 requirements. The time for this activity is defined as 12 months in the Customer Specific Requirements, but the Product Card is the superior document. If it specifies a lower frequency, this should be considered.
- Supplier Product Validation (SPV). This crucial document defines agreements made during the pre-launch phase that affect the scope of requalification tests that the production plant will need to manage in current production. If this section is incomplete, the production plant will be required to perform all tests.
- Information from warranty returns management, which details whether the customer will require the entire component to be shipped to the OEM production facility or if it’s possible to send just the appropriate sub-component. This information helps the production plant immediately filter inputs and either complete the analysis or inform the customer to send the rest of the subcomponents if needed.
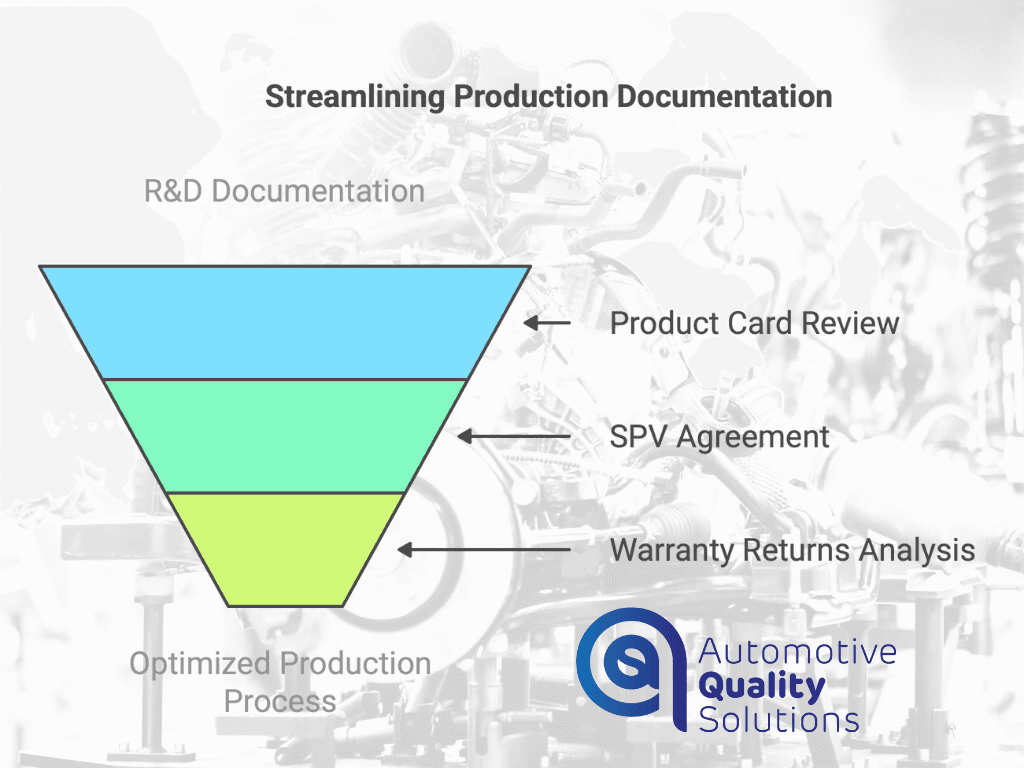
Note: In such cases, there is a possibility of losing proof for the defined problem, as the part must be reassembled, often outside the standard production process.
- Information on whether there is a Diagnostic Procedure for the dealer to replace parts covered by the warranty period. Implementing such a procedure prevents Stellantis-FCA from charging the production plant 50% of the costs for analyzes from the NFT (No Trouble Found) group.
- DFMEA severity when the production plant is co-responsible for the project (also known as co-designer). This value is important as it can be used when designing the PFMEA production process, not solely based on the classification of special customer characteristics.
Download our free ebook “Stellantis-FCA EMEA/LATAM Everything You Need To Know About Cooperation“
Author: Dariusz Kowalczyk