In the world of industry and manufacturing, issues related to product quality and compliance with standards are extremely important. It often happens that finished products require modifications or repairs to meet specified standards and customer expectations. In such cases, organizations face a choice: rework or repair?
Although both processes aim to improve product quality, they differ in terms of approach, methods, and ultimate goals. In this article, we will take a closer look at these differences, discussing the oversight of reworked and repaired products.
Understanding these processes is crucial for effective quality management and maintaining customer satisfaction.
Oversight of reworked products
Let’s start by explaining what rework is. Rework occurs when a non-conforming product undergoes modifications to meet all original requirements and specifications. According to the IATF standard (point 8.7.1.4), we must conduct a risk assessment before deciding to rework a product.
Risk assessment can utilize the FMEA (Failure Modes and Effects Analysis) methodology or another method. An example is the risk and opportunity analysis used in the automotive industry. A key step is obtaining customer approval before starting the rework if required by the customer.
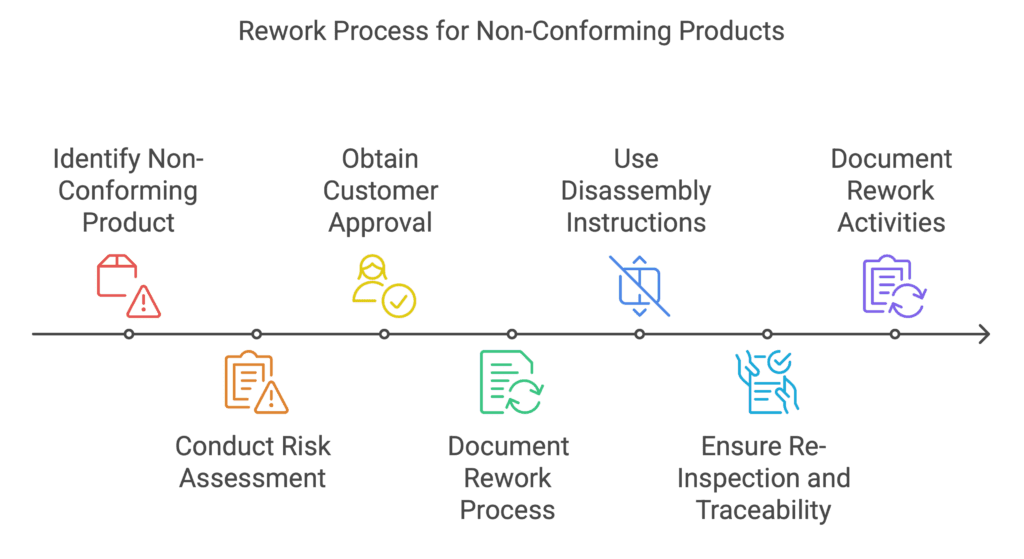
The organization must also have a documented process for approving rework according to the Control Plan or other relevant documents to verify compliance with the original specifications.
Additionally, instructions for disassembly and rework must be available and used by properly trained personnel. These instructions should cover re-inspection and traceability, which are crucial for maintaining quality standards. Furthermore, the organization must keep documented information on the number of reworked products, the methods used, and the dates.
Typical examples: repainting of parts; removal of an incorrect component from the assembly, and reassembly.
Oversight of repaired products
Similar to rework, repair also deals with non-conforming products, but with the difference that the goal of repair is to restore the product to its intended use, which may not necessarily meet all original requirements. The IATF standard defines the requirements for repairs in point 8.7.1.5, which are similar to those for rework, with one important distinction.
Before starting the repair, a risk assessment and customer approval are also necessary. The organization must have a documented process for approving repairs according to the Control Plan or other relevant documents. Instructions for disassembly and repair must be available and used by properly trained personnel, including requirements for re-inspection and traceability.
An important difference between rework and repair is that the organization must obtain documented customer approval for deviations in repaired products. In the case of rework, IATF does not require this, although customers may have such requirements, as presented in audit documents.
Additionally, the organization must keep documented information on the number of repaired products, the methods used, dates, and traceability.
Typical examples: it could be anything (reassembly, modification of the part,…) that is usable after this activity but out of specification.
Rework or repair in the context of customer requirements
IATF standard requirements can serve as an excellent starting point for analyzing whether the customers to whom we deliver products have additional criteria for evaluating rework and repairs. If you work with German customers, you can find such information in the following questions of the VDA 6.3 process audit:
- 6.2.1 β Conditions for overseeing rework (rework) are defined, assessed as part of risk analysis, and secured in the process (part identification, re-inspection, etc.).
- 6.2.2 β Example documentation: rework approval
- 6.2.4* β The scope of rework is described in work instructions + example documentation for repairs and rework
- 6.4.4 β Appropriate environmental conditions to prevent contamination, damage, part mix-up
- 6.5.1. β Example documentation: reducing losses
- 6.5.2 β Example documentation: data analysis for rework
- 6.6.1 β Is the status of manufactured parts defined (including rework)?
- 6.6.3 and 6.6.4 β Compliance with internal and customer specifications regarding documentation for rework and repairs
Another customer with additional requirements for rework and repair is the Stellantis group. The Mass Production Audit contains these requirements in the following points:
- PPC1 β Implementation of the Control Plan β the sample size subject to inspection should consider data from rework.
- SW21 β Work Instructions β should be implemented for rework.
- CNC11 β Identification β including reworked parts.
- CNC3 β Rework re-used operations:
- The process must be included in the process flow diagram.
- Is the rework process included in the skills matrix (polyvalence) and can it be performed by authorized personnel?
- Traceability! β repeating the requirement from CNC11.
- RR22 β Risk reduction β PFMEA of rework operations.
And what about CSR’s? Currently, only Stellantis x-PSA has such a provision directly on the IATF website. We will see the next update resulting from the synergy with xFCA in 2025.
Rework or Repair – Conclusion
Both rework and repair aim to improve the quality of non-conforming products but differ in their approach and scope of actions. Rework focuses on adjusting the product to the original specifications, while repair focuses on restoring functionality, which may not necessarily align with all original requirements.
Both processes require detailed risk assessments, customer approval, and documented procedures and instructions to ensure high quality and compliance with customer requirements.
If you want to learn more about this document, we invite you to our training session IATF 16949:2016 Internal Auditor.
Dariusz Kowalczyk
Literary sources:
1. IATF 16949: 2016 Requirements for quality management systems in serial production and the production of spare parts in the automotive industry, 1st edition, 2016
2. ISO 9000:2015 Quality management systems β Fundamentals and vocabulary
3. ISO 9001:2015 Quality management systems β Requirements
4. VDA 6.3 Manual – 4th edition, January 2023.
5. IATF Global Oversight – OEM Requirements (accessed on 20.05.2024)