Quality Alert is triggered after receiving a complaint from a customer or identifying an internal nonconformity. Its main purpose is to visualize the occurrence of a problem at the workplace and improve employee awareness.
Basic informations
This document is one of the Interim Containment Actions (ICA) strategies. It is most often used in conjunction with the selection and training of employees. Due to the fact that it involves filling out the appropriate form, it enhances visual management on the production line.
From a management point of view, it is important to properly manage such documents. Firstly, we must remember that it should be a system document. What does this mean? The document should:
- Have an appropriate number.
- Be cited in a given business procedure. In this case, the Claims Management Procedure seems to be the most appropriate.
Quality Alert – Document structure
In addition to basic data regarding the identification of the plant location, customer data, and the person opening the quality alert, the document should contain:
- A visualization showing the identification of an OK and NOK part.
- The location where activities will take place, specifying the place: e.g., zone outside the line, station number, external warehouse.
- The parts affected by the alert. For clarification, provide part numbers for finished products, lot numbers, dates of manufacture, all stock quantities, etc.
- The required ICA. Apart from the 8D report, the Quality Alert is a great document to define them properly. This section should define the inspection methods and criteria, visual aids, equipment, certified tools, and gauges used.
- Description for marking parts after verification. Will they be marked with a marker, sticker, or label? Additionally, agree with the client in advance on where such identification will be located. It is important that one problem does not generate another.
- Apply the same aspect to a container with certified parts.
- Provide information about the decision on parts, components, or raw materials where nonconformity was found. We should quantify the number of parts to be scrapped, provide instructions, and determine the area for repairing or returning subcomponents to the sub-supplier.
- Closing activities, product and/or process changes planned to close the Quality Alert.
- ICA exit criteria, closing actions, process changes, document updates, etc.
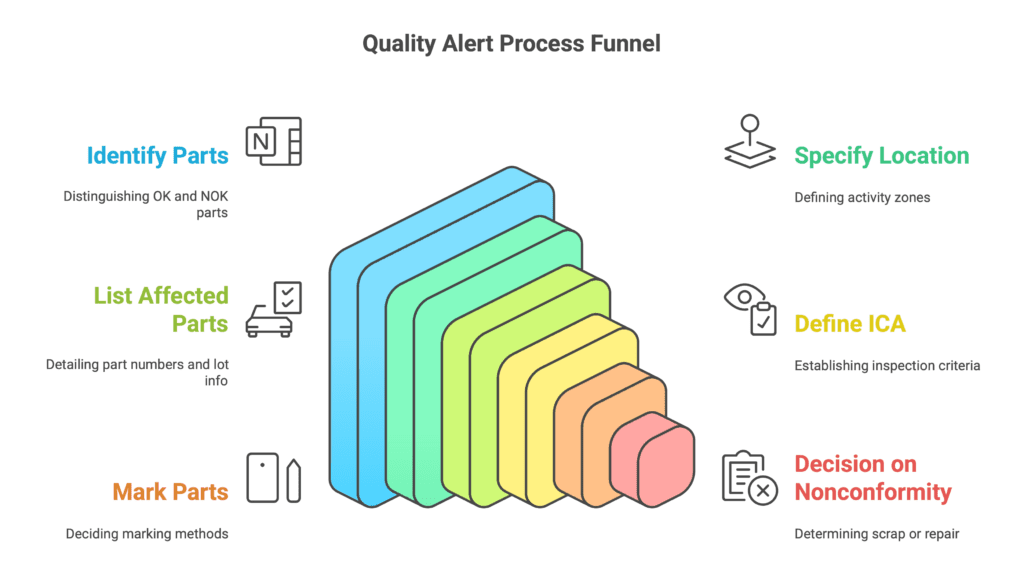
Quality Alert and 8D Report
As we can see, Quality Alert can perform an auxiliary function in relation to the 8D report. However, remember that we use the 8D report for a comprehensive approach to problem solving. On the other hand, we apply Quality Alert as a visualization on the production line and for raising awareness.
Quality Alert – Effective management
In production conditions, we usually deal with several quality requests in parallel. For this reason, it is worth defining how they are reported. This applies to both departmental meeting scenarios and daily management meetings.
One effective solution at the level of management meetings is to allocate a place on the report for quality alerts. This allows a person to simply and concisely present how many alerts are currently open. Additionally, it enables easy checking of whether any documents are out of date and need to be extended.
Duration
Dariusz Kowalczyk