The purpose of production capacity evaluation is to provide evidence to the customer that the production facility is capable of producing the agreed quantity of parts as specified in the contract.
In this article, we present best practices to help you prepare for client visits. For example, Stellantis uses a Capacity Assessment Test (CAT), German customers utilize 2 Tagesproduktion (2TP), and Ford employs Run at Rate (R@R)evaluations.
The Buffer Tells the Truth
Even if some customers do not require information about inter-operational buffers in their forms, this does not mean they won’t verify this aspect during their visit to the supplier’s plant. An experienced customer representative often starts by counting components in the buffers before beginning time measurements at individual stations.
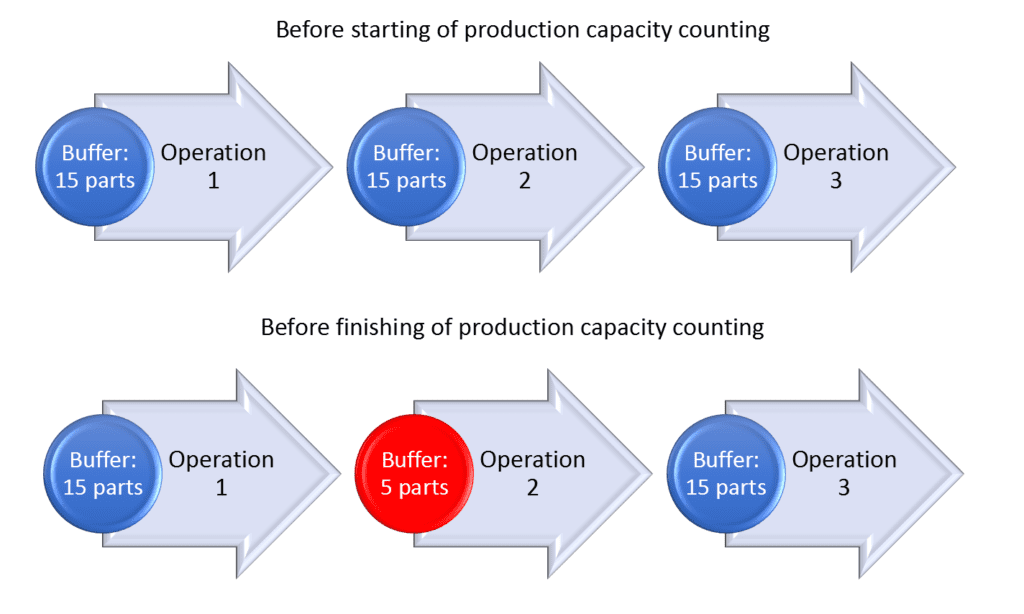
This approach ensures transparency. At the end of the capacity measurement period, the representative re-counts the components in the buffers. If significant deviations are found (e.g., 15 components at the start versus 5 after two hours), the customer may request an action plan from the supplier.
Even if production meets or exceeds contractual requirements, the customer may reject the results until appropriate rebalancing of individual operations is completed.
Don’t Overlook Sub-Supplier Production Capacity
In some cases, the customer may not approve the final production capacity results, even if the supplier meets or exceeds the contractual requirements.
More customers are now including sub-supplier capacity in their calculations. This holistic approach verifies not only the supplier’s ability to meet contractual requirements but also the capacity of sub-suppliers to produce the necessary components.
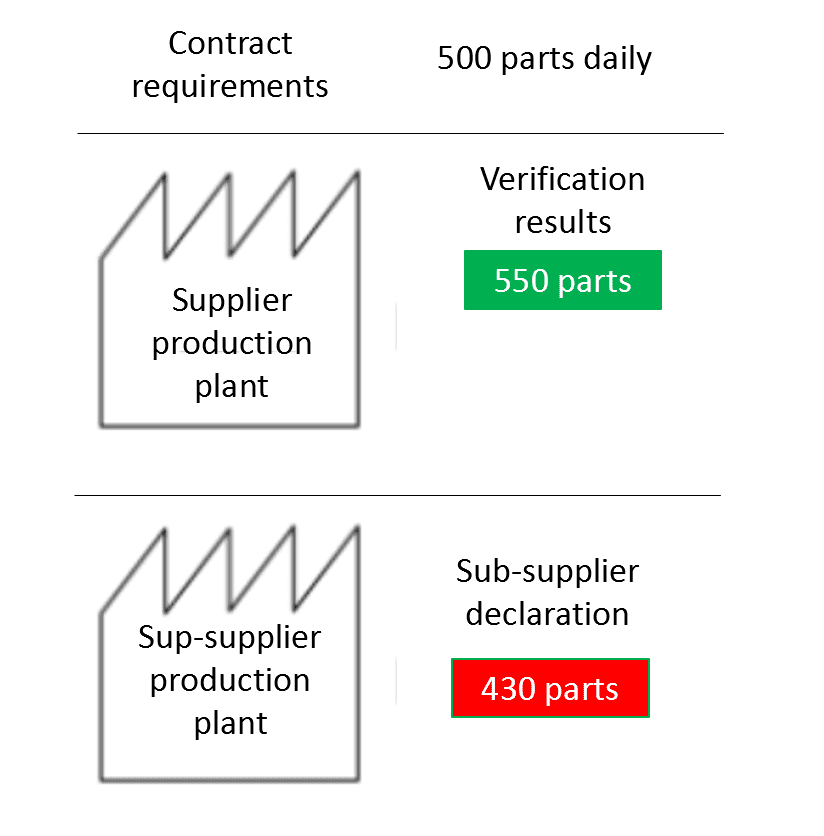
For example, if the supplier produces 500 parts but a sub-supplier can only deliver 430 components per day, the customer will use the lower value (430) in their report and require a corrective action plan.
Managing Production Capacity with Line Duplication
During new product launches, suppliers may duplicate production lines to meet contractual requirements. This applies to processes such as welding, thermoforming, or assembly. In such cases, the capacity assessment is conducted in two stages:
- First Stage: Assessment after the first production line is installed. The customer representative provides feedback that can be incorporated during the setup of the second line.
- Second Stage: Assessment after the second production line is operational, typically conducted 2–4 weeks before the maximum required production rate is achieved.
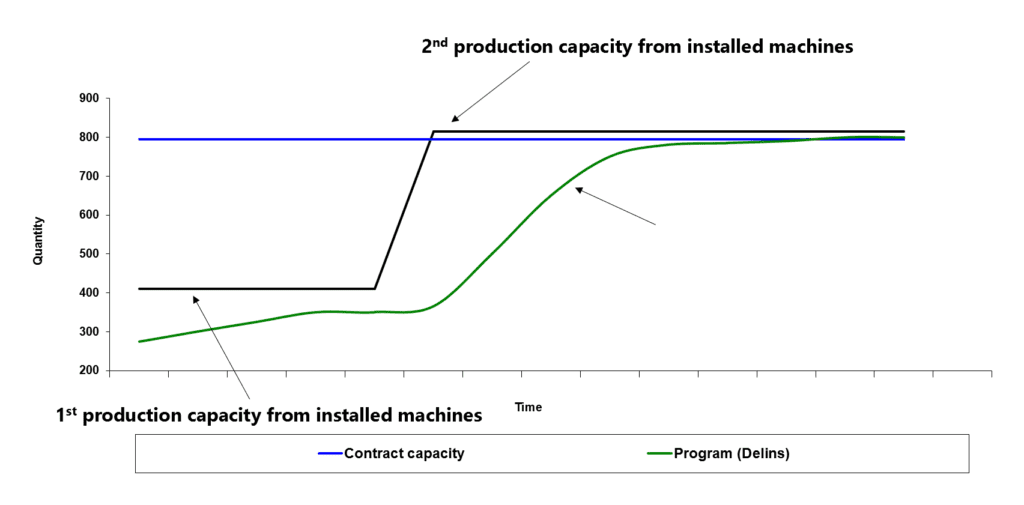
This period allows time for modifications, ensuring contractual requirements are met during the ramp-up phase.
Service Parts Production Requirements
In addition to first-assembly parts, customers may request additional service parts to be included in production plans. Typically, an additional 10% is added to the baseline daily quantity.
For example, if the contract specifies 600 components per day, the supplier must ensure production of 660 components.
To confirm service part requirements, consult your sales department, as some organizations negotiate a lower percentage (e.g., 5%) in their contracts.
Author: Dariusz Kowalczyk