One Point Lesson (OPL) is a tool that organizations widely use to strive for continuous process improvement and enhance employee skills. This document serves to convey specific, clear information about a particular aspect of work, usually related to safety, quality, or efficiency.
As the name suggests, it is intended to familiarize employees with one selected aspect, and therefore, it should take no more than 5-10 minutes.
One Point Lesson – Structure and key elements of the form
An OPL form consists of several basic elements that together create a coherent and understandable message. Typically, it includes:
- Title: A short, unambiguous topic of the lesson that immediately informs the recipient about the lesson’s content.
- Purpose: Explains why the lesson is important and its objective, helping employees understand the significance of the conveyed knowledge.
- Problem/Situation Description: Specifically points out the situation that requires attention, providing a clear understanding of the context.
- Photos/Graphics: Visually depict the steps or problem, which significantly aids in understanding and retaining the information.
- Author’s Contact Information: Allows for contacting the person responsible for the lesson, which is crucial if additional explanations are needed.
Benefits of using the OPL form
Using a One Point Lesson form brings several benefits to an organization:
- Quick Knowledge Transfer: One of the main advantages of OPL is its ability to quickly and effectively convey specific information without the need for long training sessions.
- Process Standardization: Enables the unification of procedures, ensuring that all employees perform tasks in the same way, which is crucial for maintaining high quality and consistency of work.
- Regular Safety Lessons: Reduces the risk of accidents, which is particularly important in industrial and manufacturing environments. Lessons can cover topics such as:
- Near misses
- Ergonomics improvement
- Training after an accident. Besides incidents in our facility, we can also include those that occurred in sister locations.
- New chemical substances used at the work
- Quality Improvement: Another benefit derived from sharing best practices and work standards. Remember that a One Point Lesson serves not only to train employees after a quality complaint, thus allowing us to “check off” section D3 in the 8D Report as an immediate action.
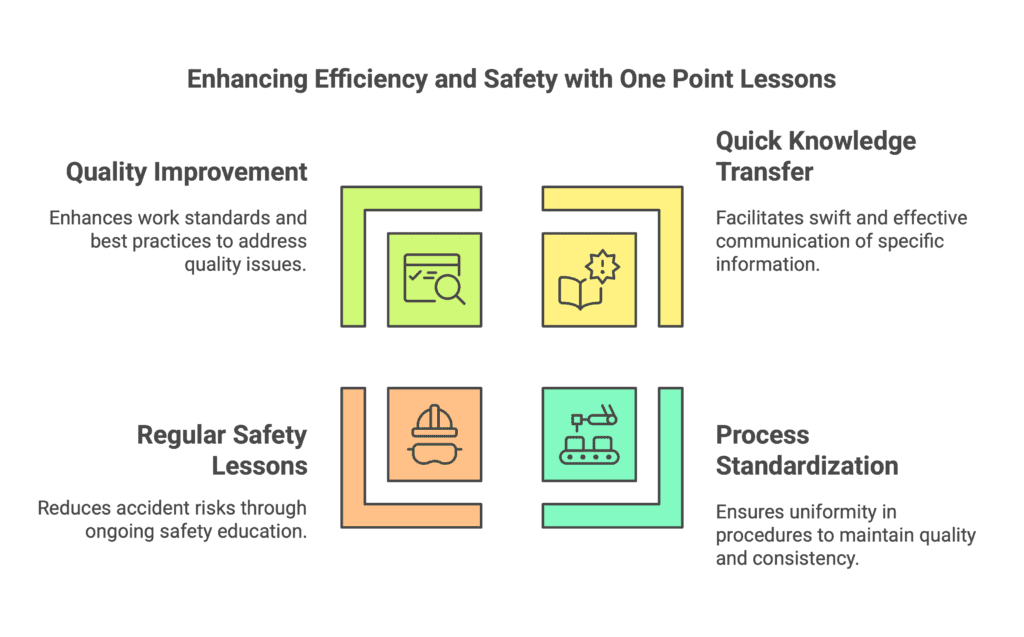
Whenever we implement any change in the production process, our operators must possess such knowledge and awareness. This, of course, applies to every production shift.
Employee Engagement
Engagement is also crucial, as OPL encourages employees to actively participate in the improvement process and share their knowledge.
An example could be updating or implementing TPM level 1. Production operators can carry out this preventive maintenance activity. They, working daily on a given machine, know exactly how to properly maintain and care for it.
What to remember when conducting a One Point Lesson?
- Allocate appropriate time. Do not allow it to be a brief reading of information from the OPL with simultaneous signing by the trained individuals.
Monitoring the implementation of trainings conducted through OPL
An effective solution for conducting training is to use Layered Audits. One of the questions worth adding to the form is the verification of operators’ awareness regarding the latest registered safety and quality reports.
During the LPA audit, we verify this knowledge in relation to the individual employee, not the entire group. This way, we can determine if additional actions are needed by the leader of a given production segment.
Systemically, also remember to ensure appropriate documentation retention time. It should comply with corporate requirements or be defined in the local plant procedure.
On the Free Tools page, you can download an editable Excel form for free for your use.
Document Name: One Point Lesson (OPL) β Excel Template
Dariusz Kowalczyk