In the previous article, we discussed areas such as complaint management, revalidation tests, and documentation review. In this article, we will focus on the maintenance and scrap isolator areas.
Maintenance Area – A Kingdom Within the Kingdom
When preparing for an OEM (Original Equipment Manufacturer) customer audit in the maintenance area, it is essential to first verify that periodic maintenance plans are in place for tooling and equipment owned by the customer. These periodic reviews, particularly at production workstations, represent the development of Total Productive Maintenance (TPM) Levels I and II.
What is Total Productive Maintenance (TPM)?
TPM is a Lean Management method focused on collaboration between Production and Maintenance teams to optimize workstation performance on the production line.
- TPM Level I: Activities performed by production operators, such as:
- Cleaning machine elements accessible without disassembling protective covers.
- Checking wear on base plates, gauges, Poka-Yoke mechanisms, or calibrators.
- Reading displays or gauges and comparing them with technological requirements.
- TPM Level II: Activities performed by maintenance teams, including more in-depth verifications that must be conducted outside standard production cycles.
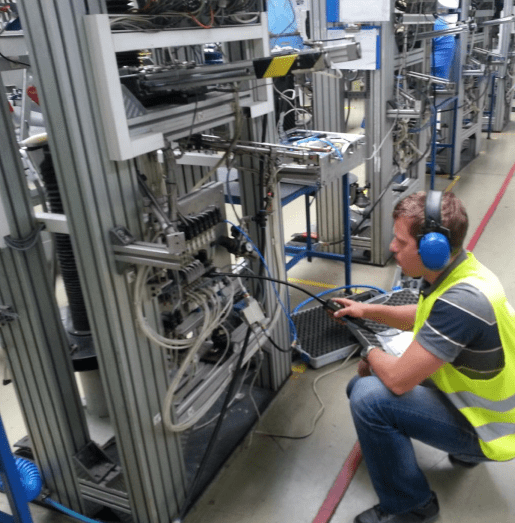
Service Contracts and Critical Components
Another crucial element is reviewing service contracts, especially those under warranty support from tooling providers. This is particularly important for newly introduced tooling. Verify key details, such as:
- Warranty coverage.
- Contact numbers provided in the contract.
- Responsibilities of external maintenance companies, particularly for second or third shifts.
Additionally, customer representatives (e.g., SQE, STA) may request a list of critical components based on factors like price, delivery time, or availability. Ensure this list is:
- Well-prepared and actively managed.
- Includes minimum stock levels to trigger purchase orders when stock falls below a set threshold.
Internal Inventory
Before the OEM client visit, conduct an internal inventory to confirm that system-listed quantities match the physical stock.
Scrap Isolator – Managing Non-Conforming Products
The scrap isolator is a designated area for blocked sub-components, inter-operational products, or finished goods identified as non-conforming during incoming inspections or production process controls.
IATF and VDA Requirements
- IATF Section 8.7.1 “Control of Non-Conforming Processes”: Does not provide specific guidelines for scrap isolator supervision but requires compliance with all customer requirements.
- VDA 6.3 Process Audit, Point 6.2.4: For customers using VDA standards, further details are provided here.
Key Points for Preparation
- Physical Security
Ensure the scrap isolator is a physically closed area. Unauthorized access can lead to someone removing sub-components or finished products without approval. Listing the names or roles of authorized personnel is a best practice. - Inventory Verification
As with maintenance spare parts, verify that the list of non-conforming parts matches the physical inventory. Conduct an internal inventory before the audit and address any discrepancies proactively. - Storage Time of Blocked Parts
Pay special attention to:- Finished products undergoing frequent modifications.
- Sub-components with expiration dates (e.g., adhesives, lubricants, paints).
If expired or outdated items are found, escalate the issue internally and take appropriate actions, such as scrapping the parts or involving the central department for further guidance.
Conclusion
Proper preparation in the maintenance and scrap isolator areas is critical for a successful OEM customer audit. By addressing key points such as TPM implementation, service contract reviews, critical component management, and scrap isolator security, organizations can ensure compliance and readiness.
Bonus Tool
You can download a free, editable Excel form for audit preparation:
Document Name: Checklist – 50 Activities to Verify Before a Customer’s Visit
Author: Dariusz Kowalczyk