When dealing with a global market and facing growing competition and constant changes, organizations of all sizes must be prepared to adapt and improve their processes. One of the key tools to aid companies in this endeavor is the Lesson Learned system—a compilation of knowledge and experiences from past projects and activities that can be utilized to enhance future endeavors.
Now, let’s explore how to effectively implement Lesson Learned within our organization to foster continuous development and improvement.
Lesson Learned and Organizational Culture
Before diving into the implementation of Lesson Learned, it’s essential to integrate it into the organizational culture. Merely initiating the process is just the first step towards establishing a long-term commitment to employee awareness. This isn’t a sprint but rather a marathon.
Senior management should consistently promote a culture of openness to learning from past projects, ensuring employees feel comfortable sharing their experiences—both successes and failures—without fear of judgment or criticism.
A fundamental element of successful Lesson Learned implementation is an organizational culture that embraces mistakes as opportunities for learning.
One notable risk associated with Lesson Learned is its susceptibility to cost optimization. During my career, I encountered a situation where the removal of contamination formed on a PCB was replaced by implementing precoating.
While this solution was documented in the Lesson Learned database as an improvement in quality (resulting in 0-km complaints) and reliability (reducing warranty returns), the engineering department decided not to incorporate this solution into subsequent projects.
Consequently, this decision led to months of customer escalations and caused stress among production facility employees due to the prolonged effort required to persuade the engineering department to re-validate the solution.

Identification, Collection and Analysis of Applications
If we aim to effectively implement the Lesson Learned philosophy, the initial step is to identify projects, operations, or activities that offer valuable insights. Subsequently, it’s essential to determine the necessary information and experiences to gather from these endeavors. This may involve reviewing design documentation and reports detailing problems, solutions, and factors influencing success or failure.
The subsequent critical phase involves analyzing the gathered data to derive valuable conclusions and insights. Tools such as SWOT analysis, cause-and-effect diagrams (Ishikawa), or the 5 Whys method can be instrumental in this process.
Retention and Information Availability
Following analysis, it’s imperative to establish a system for retaining and accessing this information. This can take the form of a database, an internal knowledge portal, or specialized “Lesson Learned” management software. Ensuring that this information is readily available to all relevant employees is paramount.
Act with the conclusions from Lesson Learned in mind
Acting upon the conclusions drawn from Lesson Learned is paramount. The primary objective of LL is to apply the acquired knowledge in practice. This entails integrating lessons learned into the planning and execution of new projects and activities. In the automotive industry, this approach is exemplified in Advanced Product Quality Planning (APQP). Organizations should aim for continuous improvement based on past experiences and mistakes.
Remember the IATF requirements
It’s also crucial to bear in mind the requirements outlined by the International Automotive Task Force (IATF). If you operate within the automotive sector, you’ll encounter LL-related considerations when analyzing the following standard requirements:
- 4.4.1.2 Product safety
- 6. 1.2.1 Risk analysis
- 6.1.2.2 Preventive action is essential to avoid problem recurrence. The 8D Report is commonly employed for this purpose, particularly in section D7. Here, along with the standard updates of the Control Plan and PFMEA, we can integrate Lesson Learned.
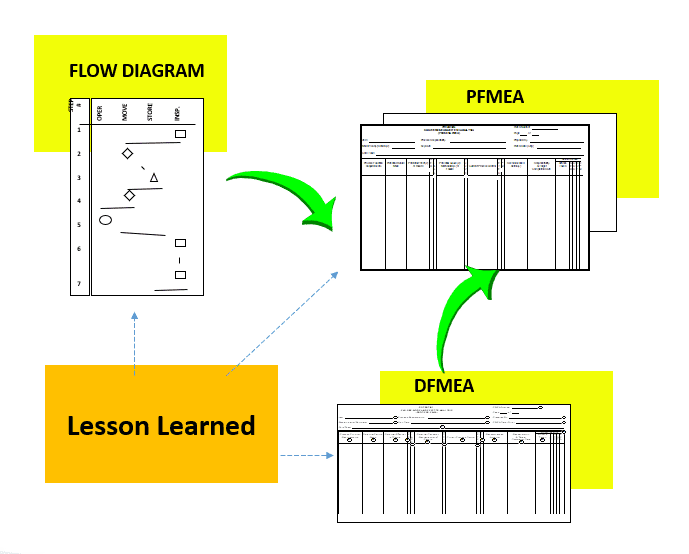
Monitoring and Evaluation of Lesson Learned Results
The final step is to monitor the impact of LL on the organization’s activities. It is necessary to track whether the implemented lessons bring positive effects, such as increased efficiency, reduced costs, or improved customer satisfaction. If not, it’s worth revisiting the analysis and adjusting your approach.
Implementing LL in an organization is a process that requires commitment and systematicity. However, the effects of continuous improvement and competitiveness are worth it. Effective learning from the past allows organizations to avoid making the same mistakes and achieve higher levels of performance.
Let us remember that learning from our own experiences is the key to success in today’s market, both in business and in private life.
Dariusz Kowalczyk