Layered Process Audit (LPA) is a pivotal element in enhancing an organization’s quality system. When properly implemented, LPAs help reduce quality issues such as field complaints and 0-km concerns, safeguarding operational activities and minimizing their impact.
LPAs encompass various aspects, including safety concerns, maintenance tasks performable by production staff, and internal notifications (non-conformities not communicated to customers). Include these areas in the audit scope to ensure a comprehensive evaluation.

Adhering to best practices during Layered Process Audits can significantly enhance their effectiveness and raise awareness among auditors and participants.
Effective Communication During Layered Process Audits
Before conducting audits on the production line, it’s essential to coordinate the timing and duration with the production leader. Given their many responsibilities during a shift, scheduling the audit ensures it receives proper attention and avoids being deprioritized.
This coordination does not imply a marginal role for production leaders in the LPA process. During meetings with the production leader, itโs advisable to:
- Identify the specific production station to be audited.
- Inform employees whose knowledge will be tested.
- Allow the leader time to prepare any necessary workplace documentation if itโs not readily available.
Calibration: Enhancing Auditor Competence Across Levels
The term โlayeredโ in Layered Process Audits refers to the different levels of personnel involved in conducting audits. Typically, there are three levels:
- Production Leaders: Perform audits during their shifts.
- Middle Managers: Conduct audits at an intermediate level.
- Senior Management or Directors: Provide oversight and a broader perspective.
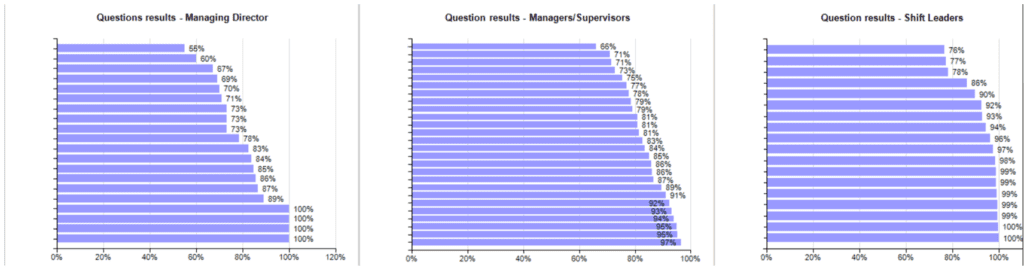
Calibrating auditors across these levels ensures consistent interpretation of potential non-compliances. For example, a manager-level auditor might invite a production leader to participate in their audit, fostering skill development and alignment. This collaborative approach strengthens the competence of all auditors involved.
Assigning Owners for Identified Non-Conformities
A critical post-audit activity involves assigning responsibility for addressing non-conformities. Itโs important to:
- Clearly inform the designated owner of their responsibility and provide a planned completion date.
- Avoid assigning tasks to individuals who did not participate in the audit.
Assigning the production leader as the owner for unresolved points or organizing a closing meeting ensures effective management of identified issues.
Production Line Audits vs. Workstation Audits
A key aspect of LPA is verifying every workstation to ensure thorough coverage. Audit every station on the production line at least once a month to ensure thorough coverage. This process provides a foundation for system-level activities, particularly when identical non-compliances are observed across multiple workstations.
Utilizing appropriate software or visualization tools can streamline this process and ensure efficient management.
Treating the Audit Question List as a Living Document
Treat the audit question list as a ‘living document’ and continuously update it based on insights from:
- Certification body visits.
- Customer feedback.
- Corporate audits.
Automotive customers, such as GM, often provide additional recommendations. For example, GM suggests including a blank field in the audit list for addressing specific topics over a given period. Examples might include verifying the effectiveness of actions following a claim or implementing a Lock-out Tag-out procedure in maintenance.
Download Free Layered Process Audit Template
You can download an editable Excel form for Layered Process Audits for free at Free Quality Tools
Document name: Layered Process Auditย โ Excel form
Author: Dariusz Kowalczyk