Organizations supplying parts to automotive clients (OEMs – Original Equipment Manufacturers) should be aware that quality or logistic issues may trigger a customer-initiated special status. This status is typically associated with non-compliance with the requirements of IATF 16949 clause 9.1.2.1 – Customer Satisfaction (Supplement).
Certification Body’s Role in Special Audit
In such cases, the Certification Body (CB) may notify the production facility about the need for a special audit, which is linked to the suspension of certification. For certain special statuses (e.g., New Business on Hold used by Stellantis xFCA, Ford, and VW), this suspension often results in the issuance of a major non-conformity.
To prepare effectively for such audits, organizations should focus on several critical steps, outlined in the diagram below.
Handling Special Audit Notifications
When informed of the need for this activity, management must evaluate whether the certification suspension is justified. If the organization disagrees, it may directly engage with the OEM representative to initiate a de-escalation process through dialogue.
If the audit is accepted, it should be conducted promptly. Delays can worsen the situation, as OEMs are notified of certification suspensions via shared platforms and may independently decide to audit the supplier. For instance, if a client (e.g., GM) initiates a special status requiring an audit, other clients may also request verifications at the manufacturing site.
Pre-Action Plan
Formal Approval of Corrective Actions
Before the audit, it is critical to obtain formal approval for the corrective actions implemented (or planned). This demonstrates the organization’s proactive approach and can improve the likelihood of a positive audit outcome.
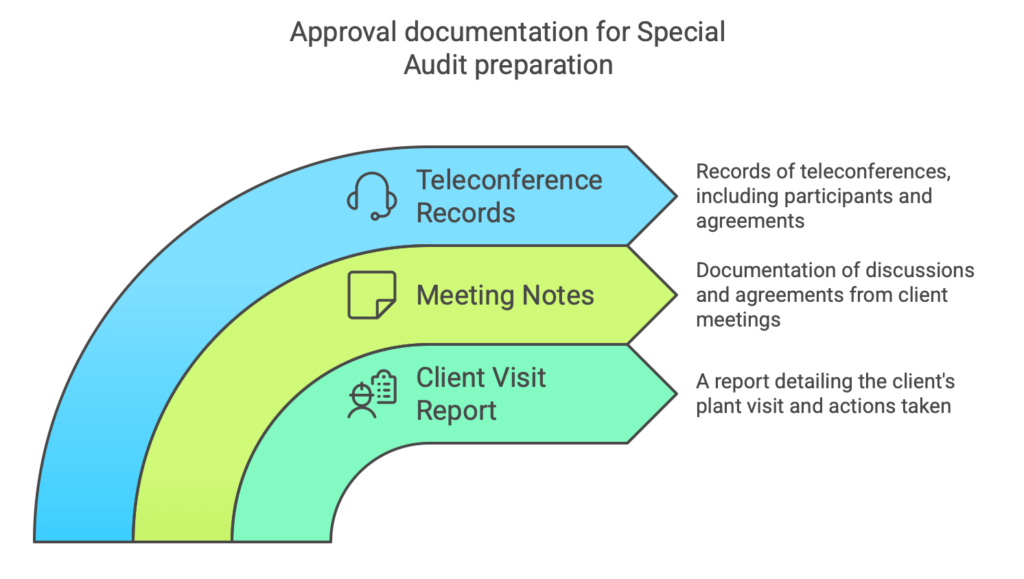
Approval documentation can take several forms:
- A report summarizing the client’s visit to the production plant and the actions taken.
- Notes or agreements from meetings held during client visits, documented for audit reference.
- Records from teleconferences, including participant details and agreements reached.
Conclusion
Special audits can pose significant challenges for organizations. To mitigate risks, it is essential to familiarize oneself with the Customer Specific Requirements (CSRs) of individual OEMs. Proactive measures and thorough preparation can help reduce disruptions and maintain compliance.
Author: Dariusz Kowalczyk