Customer Specific Requirements (CSR) outlined in IATF 4.3.2 extend beyond the quality department and impact a majority of the company’s business processes.
One effective method for identifying and managing these requirements is by applying a requirements matrix.
IATF Standard Assumptions
According to IATF requirements, production plants must periodically assess Customer Specific Requirements (CSR). In practice, the first assessment is usually performed during preparation for IATF certification. Subsequent assessments should be conducted when updating customer-specific requirements from specific OEMs.
Some organizations establish central departments to analyze CSR from individual clients (OEMs). This approach is important because deviations from CSR application can occur at the central level. For instance, some organizations may use their own forms instead of customer-specified ones during Tier 2 supplier assessments.
IATF 4.3.2 Customer Specific Requirements: How to Fulfill Them
A practical approach to fulfilling this requirement is the use of a matrix that links IATF and CSR requirements to the business processes implemented in the production plant.
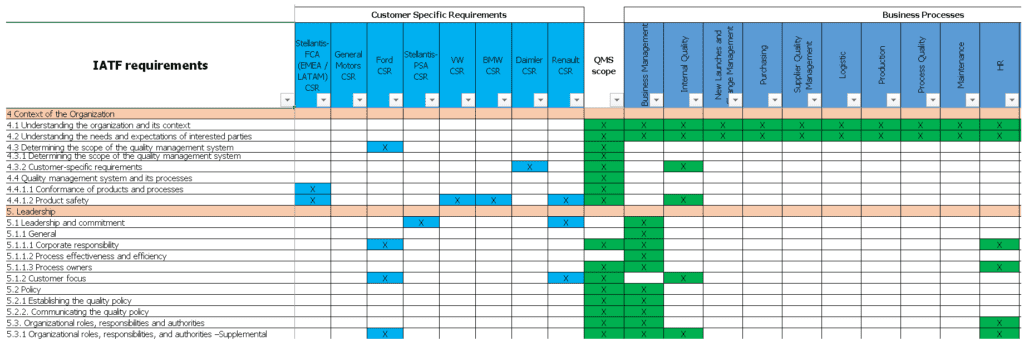
The structure of the document should be clear and systematic:
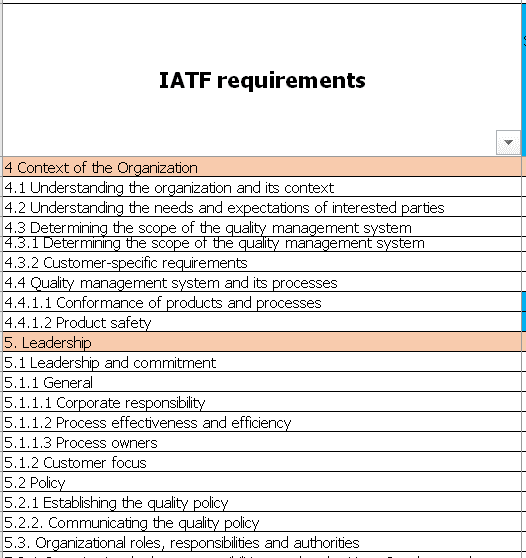
Identify CSR requirements for each customer. In the example matrix, these include Stellantis xFCA, GM, Ford, Stellantis-PSA, VW, BMW, Mercedes and Renault.
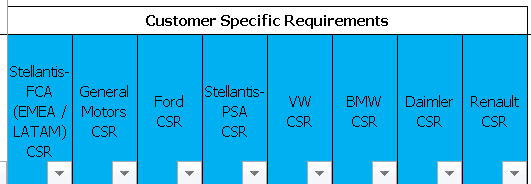
- Define the QMS scope.
The document should outline the quality management system’s scope, including documented processes with input and output connections. Turtle diagrams are often used to represent these processes. - List business processes.
On the right side of the matrix, include common business processes such as:- Business Management
- External Quality
- New Launches and Change Management
- Purchasing (often managed by remote locations)
- Supplier Quality Management
- Logistics
- Production
- Process Quality
- Maintenance
- HR
- Continuous Improvement (optional)
- QMS Management
- EHS
- Finance
- IT

IATF 4.3.2 Customer Specific Requirements: How to Use the Matrix
With the matrix prepared, it’s essential to understand who in the organization should use it and how:
- Define applicable IATF requirements for each business process.
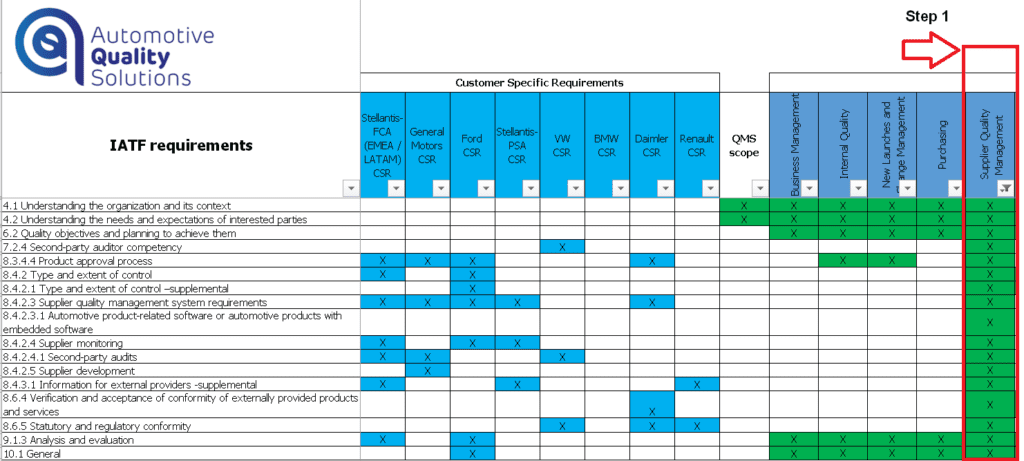
- Filter relevant Customer Specific Requirements.
Use a filter (e.g., “X”) to identify specific requirements applicable to a process. For example, the “Supplier Quality Management” process may have seven Stellantis-FCA CSR requirements to analyze and implement.
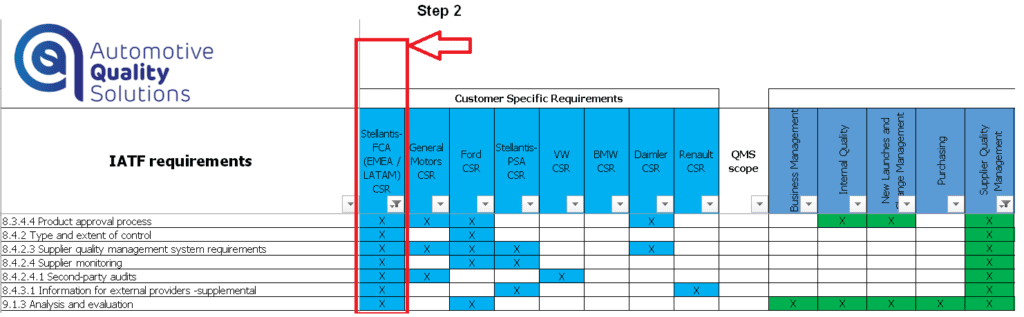
The matrix is primarily used by process owners to identify and implement applicable requirements in their areas.
Additionally, internal auditors utilize the matrix during system audits to verify that CSR requirements are correctly applied within audited processes.
Free Download
You can download an editable Excel template for a requirements matrix on the Free Quality Tools
Document name: Requirements matrix as an implementation of IATF 4.3.2 Specific Customer Requirements – Excel form
Author: Dariusz Kowalczyk