One of the most common errors in troubleshooting is that the problem was caused by the operator. In practice, this is just the tip of the iceberg, which is only a symptom. In order to define the root cause, it is very useful to use the human error analysis method – HERCA.
It is used, among others in Kaizen problem solving. It can also be a method of activities extending for Ishikawa diagram relating to the activities area performed by the operator (Man).
HERCA – what benefits it gives
By using the above human error analysis, we get the ability to define the real root cause, which may be related to:
- Superficial training
- Different working methods (between the shifts or operators)
- Shift work system that cannot be avoided in most production plants. However, it can be considered implementing employee rotation to avoid routine errors
- Unforeseen production interruptions
- Lack of space
- Incorrect placement of sub-components that are used in production overtime
- Pressure for production capacity increasing. In this case, it is worth remembering that “Quality makes quantity”
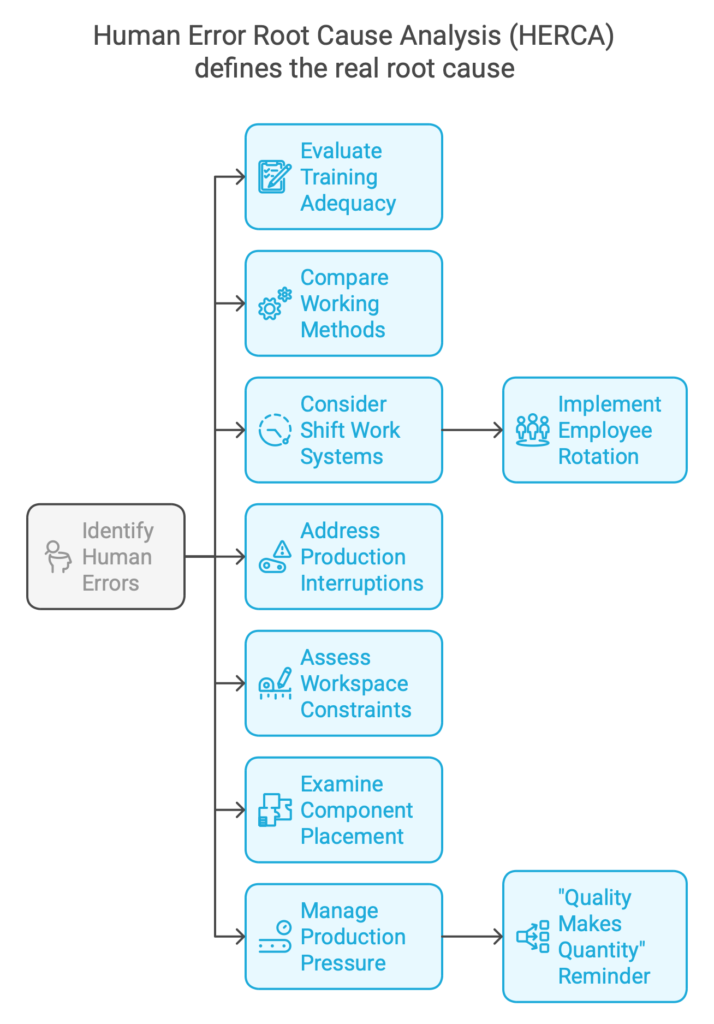
HERCA – document structure
The analysis itself consists of two sections:
- TWTTP – The Way To Teach The People – operator competence certification
- HERCA – Human Error – Root Cause Analysis – investigation into the root cause
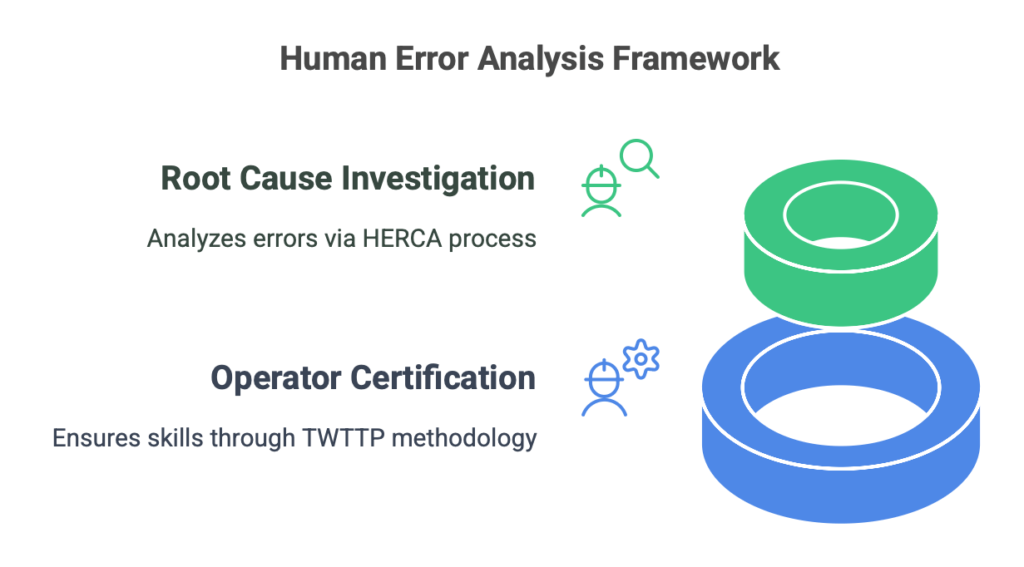
Why is the analysis of human error divided into two parts? In the first part of the analysis, we must answer the question whether the operator who made the error is properly trained. We do this by asking a few questions below:
- Describe the operation in detail
- What gives you confidence that the operation was performed correctly?
- How do you check it? At this stage, if there are special characteristics to be checked, it is recommended that this answer also be given
- What do you do when a problem arises
In case of the last question, the correct answer is the information that it has to be informed superior or leader. Most often this is done based on reaction plan. It should be available at the workplace or as a leader.
The wrong answer will be when the operator starts to solve the problem himself by unauthorized repair of the part or sub-component. If the answers are correct, we move on to the second part (HERCA) to define the root cause.
How to start the implementation?
Proper communication is the key to the success of any organization. For this reason, in the first step, plant management should perform a campaign to inform employees that the above activity is being performed in order to prevent human error and not to find the blame.
Gradual implementation is also important. In this case, it is recommended to define a model area. Then, after appropriate evaluation of the results of it can be extended to the rest of the plant areas.
You can download an automatic, editable Excel form for free on the Free Quality Tools
Document name: TWTTP β The Way To Teach PeopleΒ β Excel form
Dariusz Kowalczyk