Stellantis-FCA Advance Quality Planning (AQP) is a fundamental quality tool used by the customer’s representative, the Supplier Quality Engineer, during project development evaluations in the launch phase. The rules governing the application of AQP are outlined in the SQ.00010 standard.
Customer Specific Requirements for AQP
In the Customer-Specific Requirements (CSRs) issued in April 2017 on the IATF website, the SQ.00010 standard is assigned to the following requirements:
- 8.1: Operational Planning and Control
- 8.1.1: Operational Planning and Control – Supplemental
- 8.2.3.1.2: Customer-Designated Special Characteristics
- 8.3.3: Design and Development Inputs
- 8.3.4.3: Prototype Program
- 8.5.1.1: Control Plan
When a business opportunity is secured from the client, the decision to initiate Advance Quality Planning (AQP) meetings is made. A kick-off meeting, according to the standard, must be conducted within 15 business days—typically within three weeks from the supplier’s nomination.
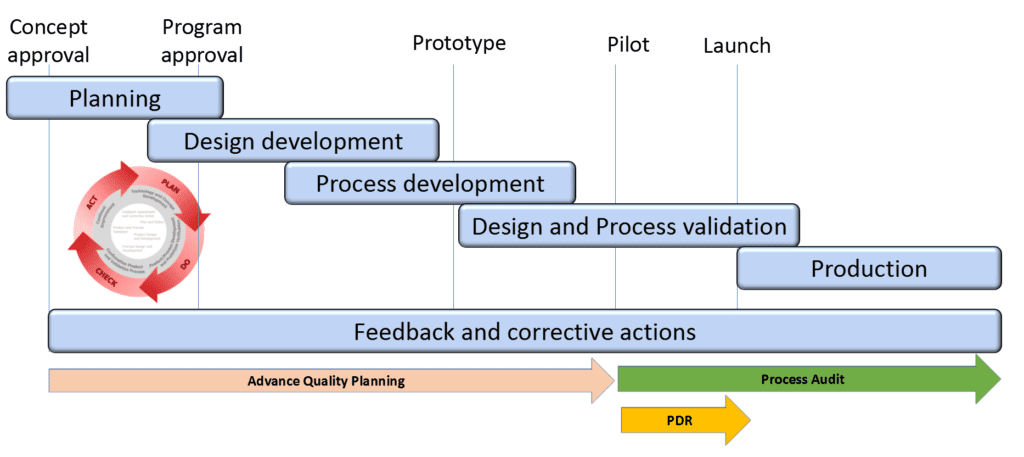
Assessing Additional Quality Requirements (AQR)
One of the key elements evaluated during an AQP meeting is Additional Quality Requirements (AQR). According to Customer-Specific Requirements (CSRs), these requirements must be communicated and distributed across the supply chain if applicable to their activities.
This requirement is verified under point 17.79 of the PPAP Audit Form, which serves as the basis for the evaluation process.
PPAP Audit Requirements for AQP and Process Audits
PPAP audit requirements are consistent for both AQP and Process Audits. However, there are differences in the methods of verification, depending on the launch phase:
- From business assignment to the Process Verification (VP) phase: All managed activities are carried out by the client based on the AQP.
- From VP to current production: The organization is assessed using the Process Audit Form.
This differentiation arises because, during the VP phase, organizations should already have production equipment and tools available. The SQ.00010 standard specifies that during the VP phase, tooling may still be at the supplier responsible for its production (off-tool, OT). From the Pre-Series (PS) phase onward, the tooling must be present at the organization’s plant (off-tool, off-process, OTOP).
Customer Monitored vs. Supplier Monitored Activities
Activities based on Stellantis-FCA Advance Quality Planning may be conducted by:
- Customer Representatives for organizations classified as Customer Monitored.
- Organization Representatives for organizations classified as Supplier Monitored.
The responsibility for these activities depends on several factors, including:
- The complexity of the product being manufactured.
- The organization’s history of cooperation with Stellantis-FCA.
- The presence of safety-critical characteristics.
- The manufacturing technologies used.
Dariusz Kowalczyk