By supplying parts to the automotive industry, every organization understands that it must meet specific quality and logistics requirements. One critical IATF requirement in this area is 9.1.2.1: Customer Satisfaction – Supplemental. When an organization fails to meet this requirement, it may face escalation.
Each client has a defined escalation process outlined in their procedures, which often includes activities such as 100% final goods control, typically lasting five weeks.
Various clients refer to this control shipment process differently:
Levels of Control in Controlled Shipping
The control process is divided into two levels based on the method of material inspection:
- Level 1 (CSL 1): The organization conducts 100% inspection using its internal resources.
- Level 2 (CSL 2): An external company, authorized by the customer, performs the 100% inspection. The supplier cannot choose the external company; it must use one approved by the client.
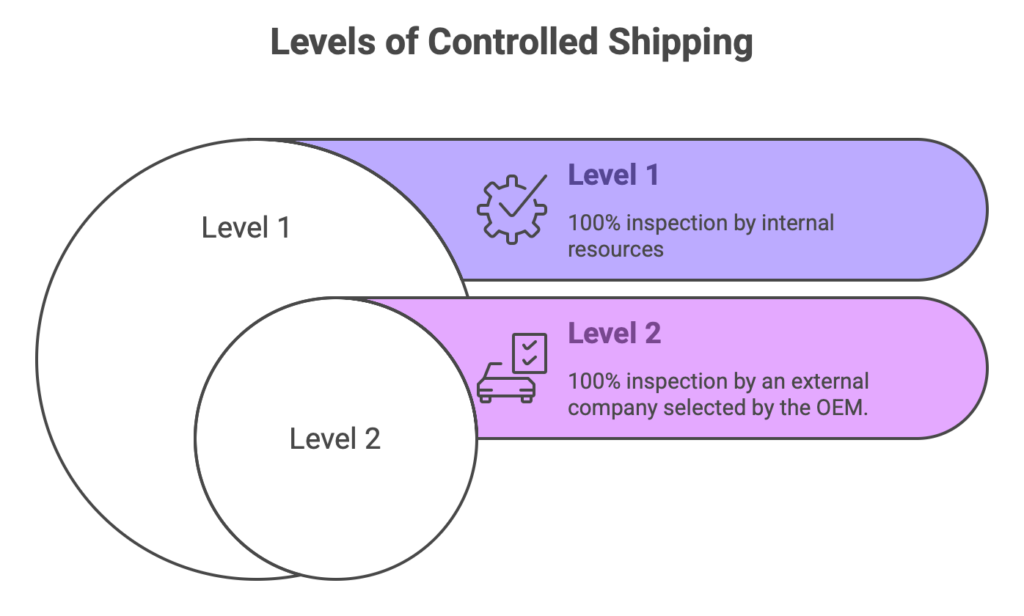
In CSL 2 scenarios, the organization must notify its certification body, which performs audits according to IATF certification standards.
Strategies for Managing Controlled Shipping (CSL)
1. Closing CSL Within One Month
When discussing CSL, it is important to remember that every time CSL is initiated, it negatively impacts the customer’s Score Card or Bid List. However, once the activity is closed, the penalty is automatically removed from subsequent rolling months.
To minimize the impact, negotiate with the customer to open CSL at the beginning of the month and close it by the end of the same month. This ensures it doesn’t appear in the Bid List for the next month.
However, this strategy leaves a procedural gap if the Control Shipment Level duration exceeds the remaining days of the month. For instance, if CSL opens on July 1 and closes on July 31, the organization must address the remaining four procedural days (since CSL lasts five weeks, or 35 days).
Negotiating an earlier closure with the customer requires strong, long-term relationships. This strategy is not applicable if CSL opens mid-month.
2. Changing Control Shipment from Level 2 to Level 1
When under special status, organizations cannot undergo supervision or recertification audits by the certification body. Instead, the oCB must first conduct a special audit.
This situation often arises when the organization is under CSL 2. To mitigate this, negotiate with the customer to transition from CSL 2 to CSL 1. It may also be possible to agree that CSL 1 will be conducted under the same conditions as CSL 2 (e.g., using an external company at rates defined by the customer).
This change can help reduce the overall impact on operations and facilitate progress towards audit readiness.
3. Early Closure of Control Shipment Through Permanent Corrective Actions (PCA)
Although CSL typically lasts five weeks, organizations can discontinue it earlier if they implement and validate permanent corrective actions (PCAs) ahead of schedule.
For example, if after three weeks the organization introduces a corrective action that not only detects potential issues but also prevents them, there is no need to wait another two weeks. Instead, initiate discussions with the customer to close CSL early, providing evidence of the corrective actions taken.
Propose that the customer directly verify these activities in the production plant for validation. This approach can lead to early closure, saving costs associated with external companies performing inspections, which often have higher rates than those pre-negotiated with the customer.
Author: Dariusz Kowalczyk