In many manufacturing companies within the automotive industry that utilize special processes, compliance with the guidelines outlined in the CQI-12 Coating System Assessment manual is mandatory. Major customers such as Ford, General Motors, and Stellantis (formerly FCA) enforce this requirement.
Organizations often face challenges in assessing product quality through destructive testing, which can be costly when applied to special processes. Due to these limitations, achieving 100% verification of compliance with quality requirements during production may not always be feasible.
To ensure a reliable production process that meets product requirements, it is crucial to effectively implement the guidelines outlined in the CQI-12 manual. This approach enables continuous process improvement, reduction of variability and waste, and ultimately leads to cost reduction.
Key Sections of the CQI-12 Manual
The CQI-12 manual comprises four main thematic sections and eleven process tables:
1. Staff Responsibility and Quality Planning
The first section emphasizes the importance of staff accountability and quality planning. It includes audit questions and corresponding requirements, supported by additional questions to aid understanding. These requirements are largely aligned with the IATF 16949 standard.
2. Transportation, Area Management, and Material Flow
The second section addresses requirements for transportation, material flow, and area management. As with the first section, it incorporates detailed audit questions and expectations to evaluate compliance effectively.
During auditing, it is essential not only to determine whether requirements are met, unmet, or non-applicable but also to document evidence supporting each assessment.
3. Pyrometry in Coating Application
The third section introduces new requirements concerning the pyrometry (temperature measurement and control) of the coating application process. These requirements are evaluated within designated process tables.
4. Job Audit
The fourth section focuses on conducting product audits, similar to those outlined in the VDA 6.3 manual. This involves auditing at least one product, prioritizing safety-critical or high-risk components. If time permits, additional product audits may be conducted.
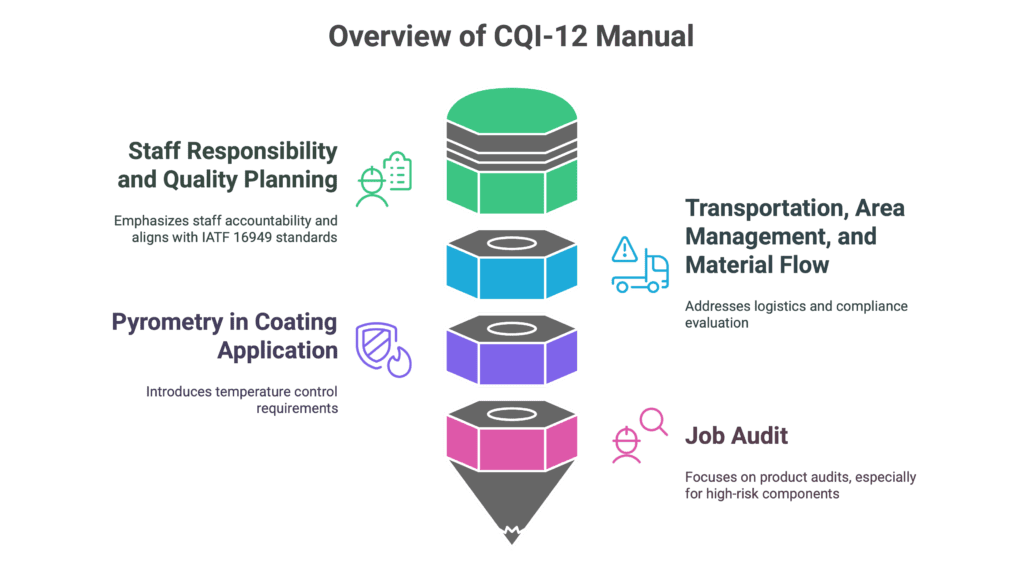
CQI-12 Process Tables
The CQI-12 process tables, labeled A-K, are designed to standardize the evaluation of different process types and equipment.
- Tables A to J: These tables focus on specific process types and outline the stages and parameters that require monitoring. They specify minimum control requirements (e.g., automatic, manual, per the Control Plan) and monitoring frequencies.
- Table K: This table differs from the others, as it addresses monitoring and measurement equipment rather than process parameters. It includes details on calibration requirements and frequency for each device.
Additionally, during the Job Audit, these tables include sections for assessing the actual control methods and monitoring frequencies. Auditors document the current parameter results to ensure compliance with established standards.
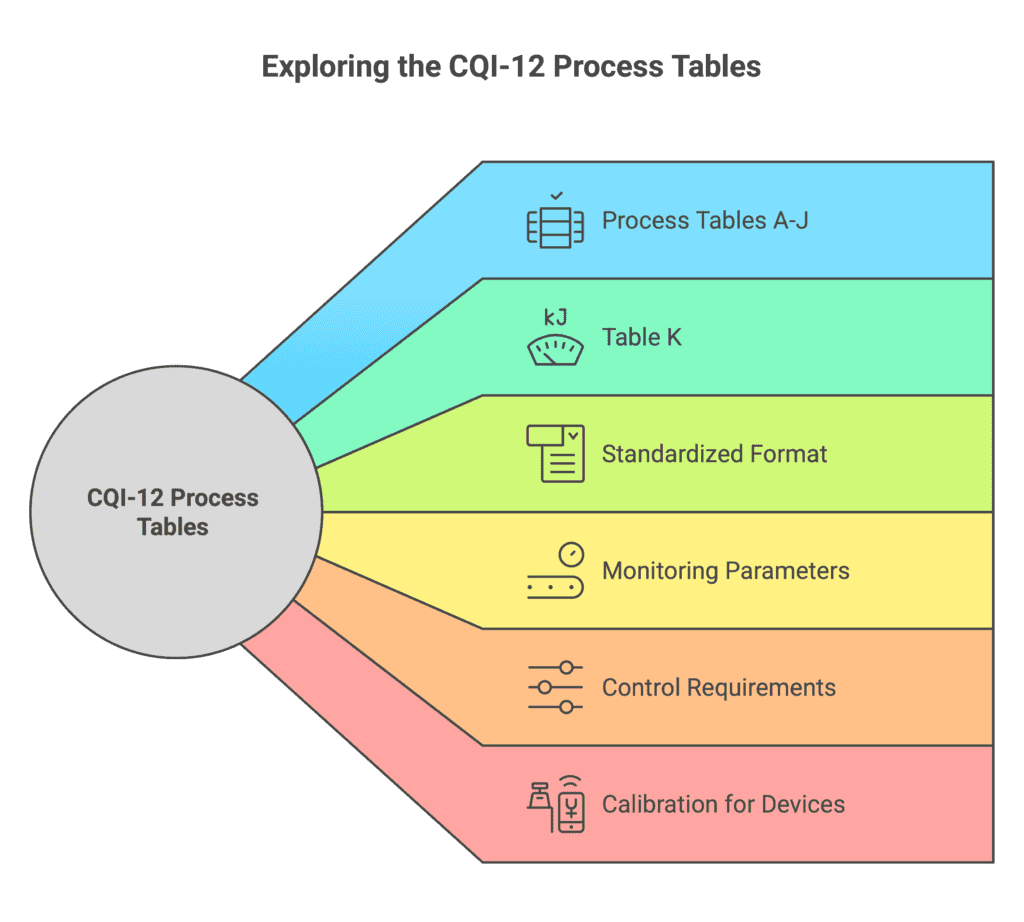
Implementing CQI-12 Requirements
Implementing the requirements outlined in the CQI-12 manual may initially demand significant time and resources, which could result in added costs. However, the long-term benefits far outweigh these initial investments.
By adhering to CQI-12 standards, organizations can:
- Deliver products that consistently meet stringent quality requirements,
- Reduce costs associated with errors and non-compliance,
- Improve process reliability and efficiency.
Most importantly, compliance fosters customer satisfaction, strengthening relationships with key clients and paving the way for continued collaboration on future projects.
Joanna Kucharska-Cichoń