CAPA (Corrective and Preventive Actions) is a systematic approach to identifying, eliminating, and preventing problems related to quality and performance in organizations, implemented as a record for managing corrective and preventive actions.
The CAPA system is widely used in the pharmaceutical, medical, food, and other sectors where quality and safety are critical. It allows tracking the problems that arise within an organization and monitoring the implementation of actions, their status, deadlines, and effectiveness.
Format
Increasingly, organizations are no longer managing CAPA as an Excel list, which is manually controlled, but are adopting simple, internally managed application-based solutions.
This allows for the full automation of notifications in case of exceeding the action implementation time, centralization of actions, data collection and analysis, the ability to compile statistics, monitor actions using visualizations, track the progress of ongoing work, and observe trends within specific areas and the organization as a whole.
Additionally, for organizations that have implemented a system of cascading approval of actions, sometimes up to Top Management, it allows for the processing of these actions in an organized and systematic manner, along with integration with the ERP system used in the organization.
Key Elements of the CAPA System
The minimum content of an application that allows efficient management of non-conformities in an organization includes the following categories:
1. Problem Identification
- Non-conformity number
- Type of non-conformity β e.g., external complaint, internal, post-audit actions
- Category of non-conformity β e.g., product, process, system
- Problem description β preferably using tools such as 5W2H
- Area affected by the non-conformity
2. Cause Analysis
- Cause of the non-conformity β e.g., description plus identification according to 4M
3. Actions
- Corrective actions
- Preventive actions
- Person responsible for implementation
- Implementation deadline
- Implementation status
4. Validation and Verification
- Effectiveness assessment
5. Documentation and Follow-up
- Automatic alerts for unresolved actions
It is worth mentioning some key definitions here to better understand the rationale behind the CAPA system. These are:
- Corrective Actions β Taken when a non-conformity is identified. They aim to eliminate the cause of the non-conformity.
- Preventive Actions β Taken when a potential issue is identified. They aim to eliminate the cause of potential non-conformities (similar products, processes).
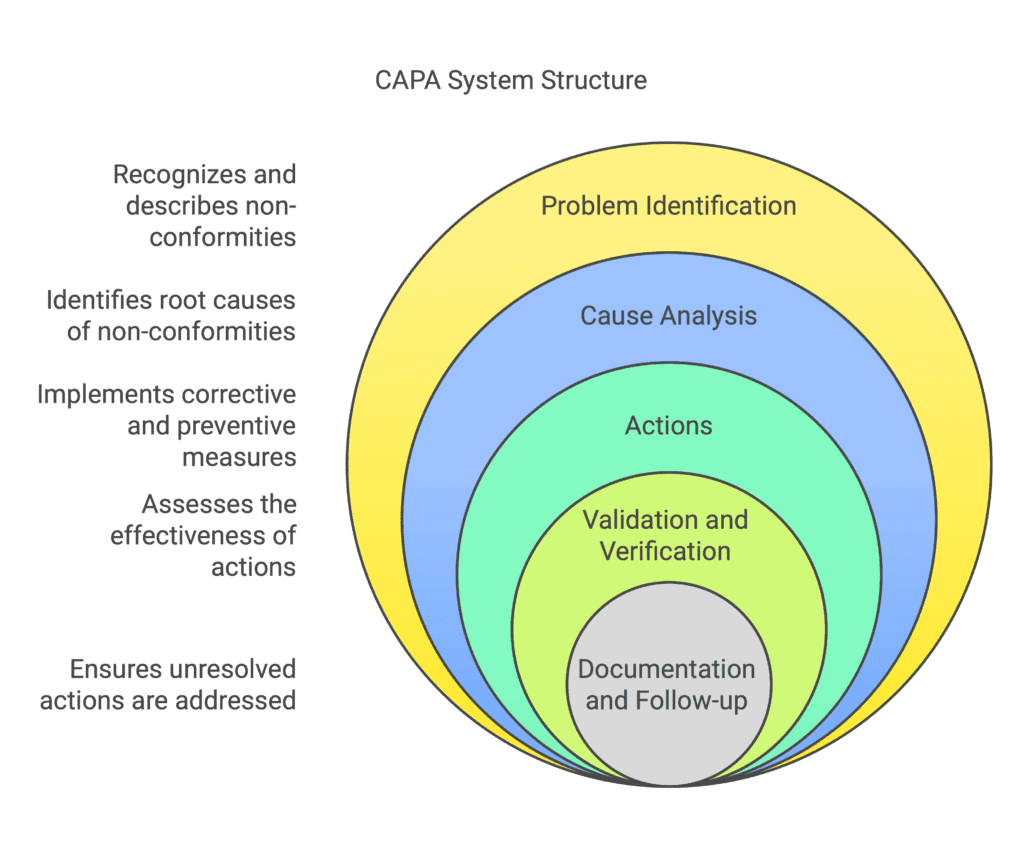
Additionally, during problem-solving processes, actions should always be appropriate to the cause of the problem and the failure to detect it. Only this approach can make the problem-solving process effective, leading to a permanent solution.
Benefits of implementing the CAPA system
Implementing a CAPA system is a process that requires the involvement of the entire organization and the support of Top Management. The minimum benefits that can be defined include:
- working within the PDCA cycle,
- implementing a continuous improvement approach in the organization,
- applying lessons learned.
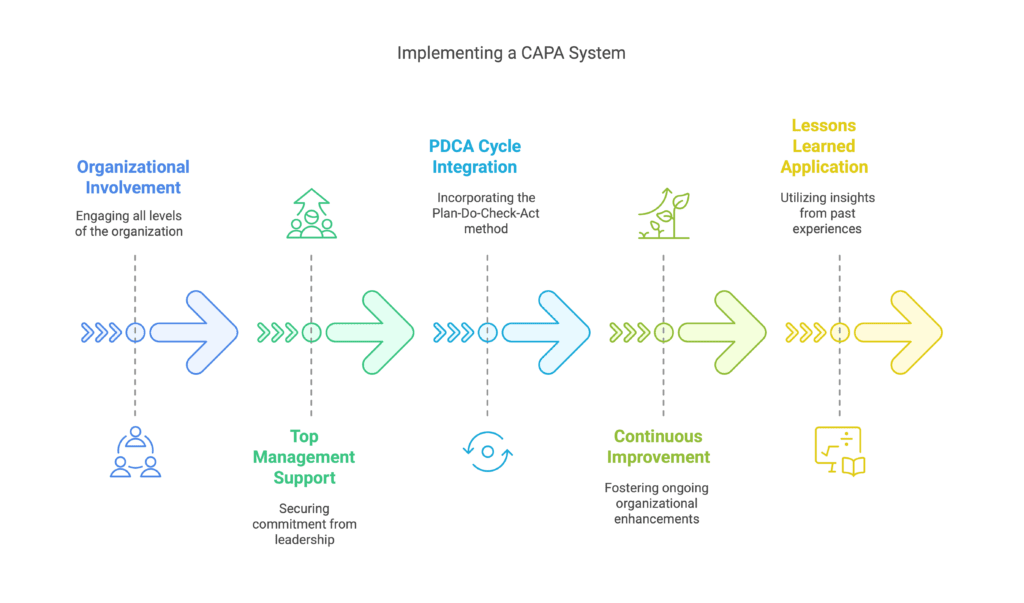
These actions collectively shape a learning organization.
As a result, these actions should lead to improved production processes and product quality, systematic elimination of defects, disruptions, and prevention of their recurrence.
Thus, the final outcomes should include reduced quality costs and increased customer satisfaction, along with a long-term strategy for building the organization’s competitive advantage.
Kinga Niedziela