When working with automotive customers (OEMs), it is important to keep in mind some best practices related to NVH evaluation and production plant involvement that can assist the organization during the launch and serial production phases.
In the article below, we’ll focus on two areas that have a significant impact on the above issues:
Criteria for Defining Noise and Vibration Assessment (NVH)
It is essential that components planned for FMEA (Failure Modes and Effects Analysis) evaluation from an NVH perspective have defined appropriate testing conditions in the car environment.
During the initial quotation phase and technical meetings with the customer’s engineering department (e.g., technical review), the organization should request information about the test track profile where the vehicles will be tested (height, width, spacing between obstacles on the test track, and their angle of inclination relative to the car wheels).
Additionally, it is worth defining the speed at which the car will travel through the test track and specifying the version, as the suspension (e.g., in the standard version) may differ from that of vehicles with drive on both axles.
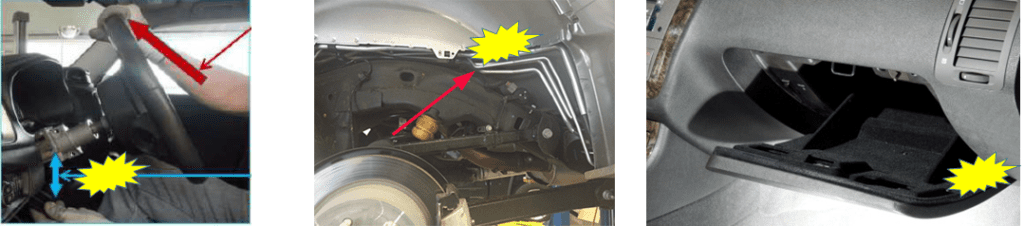
The organization must ensure that the information from the test track used for validating the customer’s vehicle and the supplier’s products aligns with the test track parameters at the customer’s location, where the vehicles will be produced. This alignment will help the organization avoid potential complaints from the client’s plant during current production.
An ideal solution would be for the supplier’s engineer responsible for NVH to conduct a correlation between the two test tracks with the client’s engineers (at both the development phase test location and the client’s plant).
These data should serve as input for defining the appropriate frequency ranges for automatic testers (EOL – End of Line Testers), which are typically provided for such components.
Involvement of the Organization’s Production Plant in the Initial Evaluation (RFQ – Request for Quotation) Sent by the Client
From the production plant’s perspective, it is crucial that appropriate representatives have the opportunity to review the design feasibility of the product provided in the client’s quotation. This early feedback allows for the verification of drawing tolerances for significant and/or critical characteristics.
By presenting data from current or similar projects, the organization may prompt the client to revise drawing tolerances even before the formal contract is signed. This proactive approach can help avoid quality issues that may arise during the launch phase at the customer’s plant.
At this stage, the organization must remember the key principle: the more time passes after production release (SOP – Start of Production / PR – Production Release), the more difficult it becomes for the supplier to implement changes in tolerances. The client may also inquire about the level of production capability demonstrated by the supplier’s process throughout earlier project phases.
Nonetheless, if quality issues occur, they must be addressed effectively.
It is also important for the Project Manager and/or Program Manager, if centrally assigned, to have the opportunity to familiarize themselves with the supplier’s target production plant processes.
This can help avoid misunderstandings, such as incorrect placement of characteristics to be measured on fixtures (e.g., locating them where fastening devices for movement are positioned).
Author: Dariusz Kowalczyk