Nonconforming product management is a daily reality in the manufacturing world. Defects are inevitable, but how you handle them can mean the difference between a minor hiccup and a major issue affecting customers, your company’s reputation, or even halting production.
This article highlights specific scenarios and common mistakes that occur in production facilities, along with strategies to avoid them.
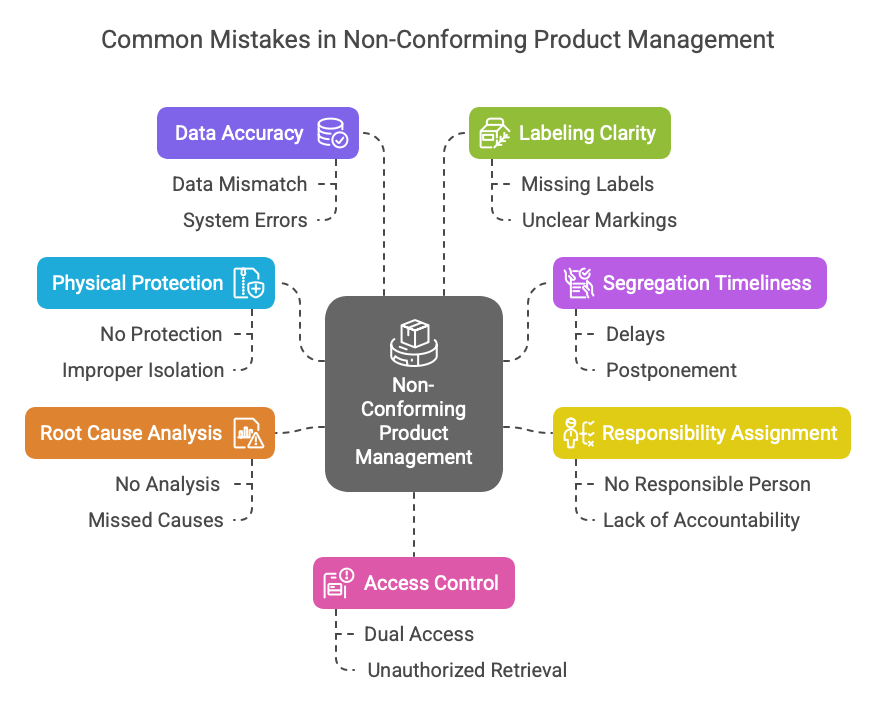
Nonconforming Product Area That Doesn’t Isolate
In theory, you have a designated area, a red bin, labels, and tags. In practice? The isolation area is open, lacks coverage, and anyone can reach in and take whatever they want. Or worse – the entire room or cage serving as the isolation area is perpetually open. Anyone can enter, place something inside, or remove items without any control.
This is how nonconforming products find their way back onto the production line because someone, either unknowingly or in haste, accessed them inappropriately. Sound familiar? Unfortunately, this is a common occurrence in many facilities.
The problem is that despite having procedures in place, there are no real barriers. Without physical obstacles, sooner or later, someone will “just take a look” or “grab it because it’s needed.”
Solution: The isolation area isn’t just a factory ornament – it must be closed, physically separated, clearly labeled, and accessible only to authorized personnel. If it’s a bin, it should be lockable with restricted access.
If it’s a designated area, it should be one that cannot be entered without proper authorization. Otherwise, it’s not managing nonconforming products; it’s merely the illusion of order.
Scrapping, but “Starting in the System” – Where Chaos Begins
End of the year. Inventory time. Decision: “Let’s scrap the accumulated components to close the year cleanly.” This time, however, they started with the system – parts were marked as scrapped. The problem? Physically, they were still in the warehouse. Logistics, unaware that these were now nonconforming parts, assembled the order and shipped it to the customer.
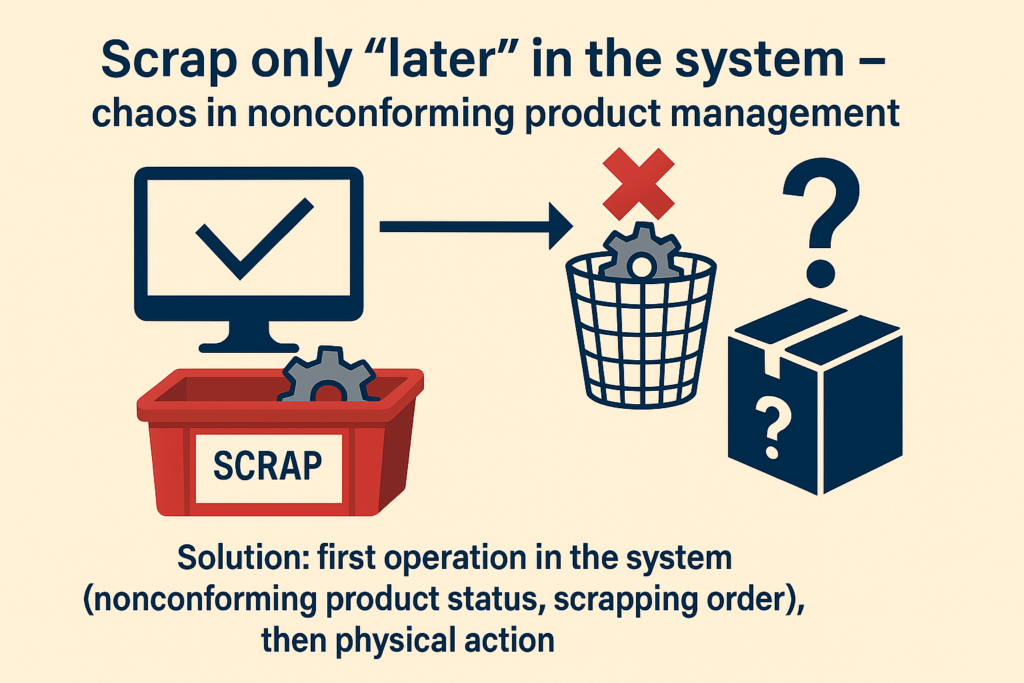
Does this sound like a trivial mistake? Yet the consequences were severe – a product with a nonconforming component reached the market, resulting in a customer complaint. All because the process began in the system rather than with actual physical actions.
Solution: Always start with physical scrapping – removing and securing the parts. Only then perform the system operation: change the status, record the actions, document everything. The physical state of the warehouse should be the reference point – because it’s the physical product that reaches the customer, not system records. Without consistency between the system and reality, there is no quality control.
Red Rabbit Consumed by the System
The Red Rabbit, a negative control sample, has one task – to test the alertness of the process. The problem arises when it’s stored in the same place as nonconforming products. The result? Someone doesn’t recognize it, assumes it’s scrap, and discards it – and that’s it. At a crucial moment, we have no way to verify if the detection system is functioning. Then comes the surprise when something slips through the line.
This is a typical case of thinking: “It’s just a part – why all the fuss?” However, the Red Rabbit isn’t an ordinary component – it’s a tool for verifying the entire process. Losing it or confusing it with a nonconforming product can mean missing actual errors.
Solution: Keep negative control samples separate, preferably in a closed, labeled container or a dedicated shelf. Mark them clearly – not just with color but also with a large label saying “Red Rabbit – do not remove.” This way, you’ll avoid many unnecessary problems and misunderstandings.
Scrap Isolator Isn’t a Warehouse
You have an isolation area. You have a system. But do you have consistency between the two? In many facilities, the answer is: “We don’t know.” And that’s where the problem begins. Lack of regular inventory in the scrap isolator leads to situations where system data doesn’t match reality. The warehouse is empty, but SAP shows 12 units. Or vice versa.
Then, a customer auditor arrives and asks: “How many nonconforming products do you physically have?” – and you check, count, and… start sweating. Because the system shows one thing, and the actual state is entirely different.
Solution: At least once a month, compare system data with the physical count in the isolation area. This applies not only to components but also to finished products. It’s the only way to truly keep your finger on the pulse.
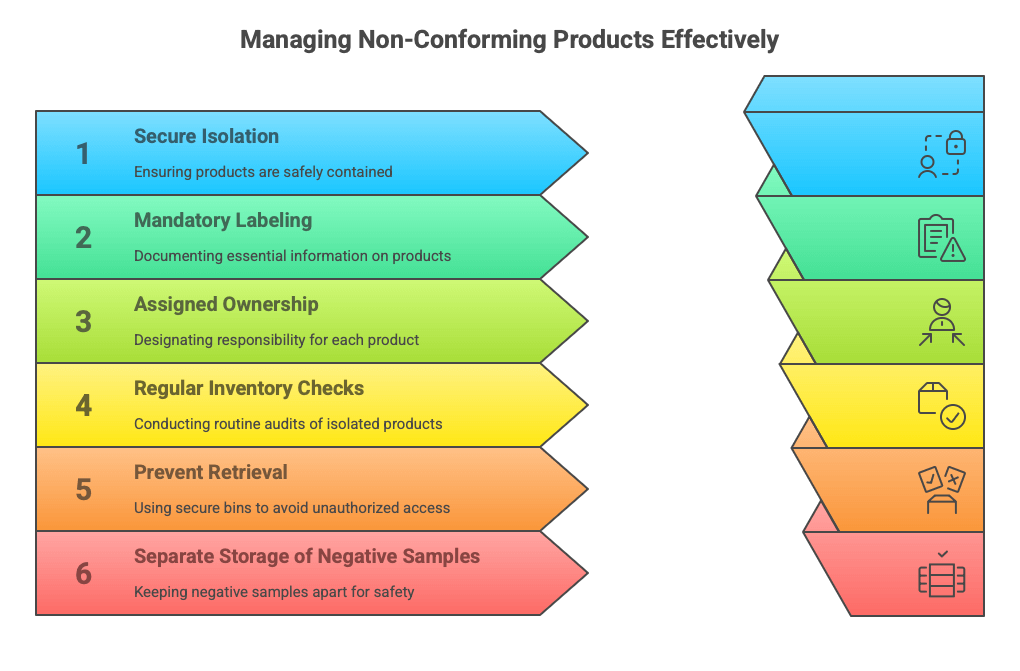
No Label? No Certainty in Managing Nonconforming Products
A red bin, a part set aside, but… without a label. In theory, everything appears to follow procedure. In practice? The operator doesn’t know what this component is – it might be nonconforming, or perhaps someone just set it aside “for a moment.” In such a situation, it’s easy to make a mistake and reintroduce the nonconforming product to the line.
This isn’t just an operational error – it’s a systemic risk. A shift change, a new employee, or haste during production can easily result in such a part reaching the customer again. Without a trace, without accountability, without safeguards.
Solution: Every part entering the isolation area must be labeled. The label should include: status (nonconforming product), date, reason, responsible person. This isn’t an optional detail; it’s a fundamental requirement of the quality system related to identification.
Nonconforming Product Set Aside “for Later” – Delayed Decisions in Managing Nonconforming Products
A shelf near the workstation, a few parts set aside “for a moment” because someone didn’t have time to report them. But that “moment” turns into a week, then a month, and eventually, no one knows what these components are.
The nonconforming product, instead of being in the isolation area, is lying somewhere off to the side, without labeling, without a decision, without responsibility.
This problem is particularly prevalent at the end of a shift when a component isn’t properly labeled because the leader was in a hurry.
Such a scene isn’t uncommon. In the daily rush, it’s easy to justify: “I’ll deal with it later.” The problem is that no one does. And parts from the “reserve shelf” end up back on the line – because they look like new.
Solution: No exceptions. A nonconforming product immediately goes to the isolation area. No setting aside, no temporary spots, no waiting for a “better moment.” These aren’t waste – it’s a matter requiring immediate action.
No Root Cause Analysis = The Error Will Return – A Missed Opportunity in Nonconforming Product Management
Scrapping doesn’t fix the root cause. The part disappears from the warehouse, but… it will come back. Maybe in a week, maybe in a month — but it will return if we don’t understand why it failed in the first place. In many companies, the analysis ends with “scrap it” — no 5Why, no FMEA update, no lesson learnt.
But every nonconforming product is a signal — something in the process isn’t working. If you ignore it, you’re missing a valuable opportunity to improve. Worse, you’re allowing the same issue to repeat for years. Quietly. Consistently. Expensively.
Solution: Don’t close the case without analysis. Find the root cause — even if it takes time. Use 5Why, check both process (PFMEA) and logistics (LFMEA) risk analysis. Only then does nonconforming product management serve as a tool for improvement — not just a way to hide the problem.
Managing without analysis is like treating symptoms without a diagnosis — it might work for now, but the problem will come back. And it’ll cost more than you think.
A Red Bin… That You Can Reach Into – Small Flaws, Big Risk
At first glance, everything looks fine. A red bin, proper labeling, a designated spot on the line for nonconforming parts. But look closer — the opening is big enough that the operator can easily reach in and pull the part back out. Out of curiosity, by accident, or simply because it’s easier.
And that’s when the whole system starts to fall apart. A part that was supposed to be segregated ends up back in production. Without review, without a decision, without control. All because of a detail that should’ve been flagged during PFMEA.
Solution: Use one-way drop bins or containers with physical access restrictions — so once a part goes in, it can’t be retrieved easily. If something is identified as nonconforming — it needs to stay put until a formal decision is made.
Nonconforming product management is all about the details. One careless reach into a bin can trigger a chain reaction that ends with a customer complaint… or worse — an escalation.
Summary: The Product Isn’t the Problem. Lack of Action Is.
You can’t eliminate all nonconformities — but you can build a system that ensures they don’t leave the plant, don’t reach the customer, and don’t come back as complaints.
That’s exactly what we teach in our IATF 16949 requirements training — because effective nonconforming product management starts long before the first defect appears.
Author: Dariusz Kowalczyk