Sooner or later, every manufacturing organization faces a quality issue that requires appropriate corrective actions. A common mistake made during the analysis process is defining the cause as an “operator error.” Why? Because, in most cases, this is only the tip of the iceberg, a symptom rather than the root cause. A suitable technique for addressing such issues is Human Error Root Cause Analysis (HERCA).
Human Error Root Cause Analysis – Structural Advantage
In a standard analysis, root causes are typically defined using the Ishikawa diagram followed by the 5 Whys technique. At first glance, this approach seems straightforward. However, moving from the first “why” to the subsequent ones requires caution to ensure the analysis stays on track.
Simply put, it demands experience and a thorough understanding of the process and the product.
Unlike standard methods, human error analysis offers a structured framework that guides users through answering specific questions grouped into relevant categories, such as:
- Proper and accurate documentation
- Process compliance
- Factors defining standard working conditions
- Personal issues
- Potential for distraction or forgetfulness
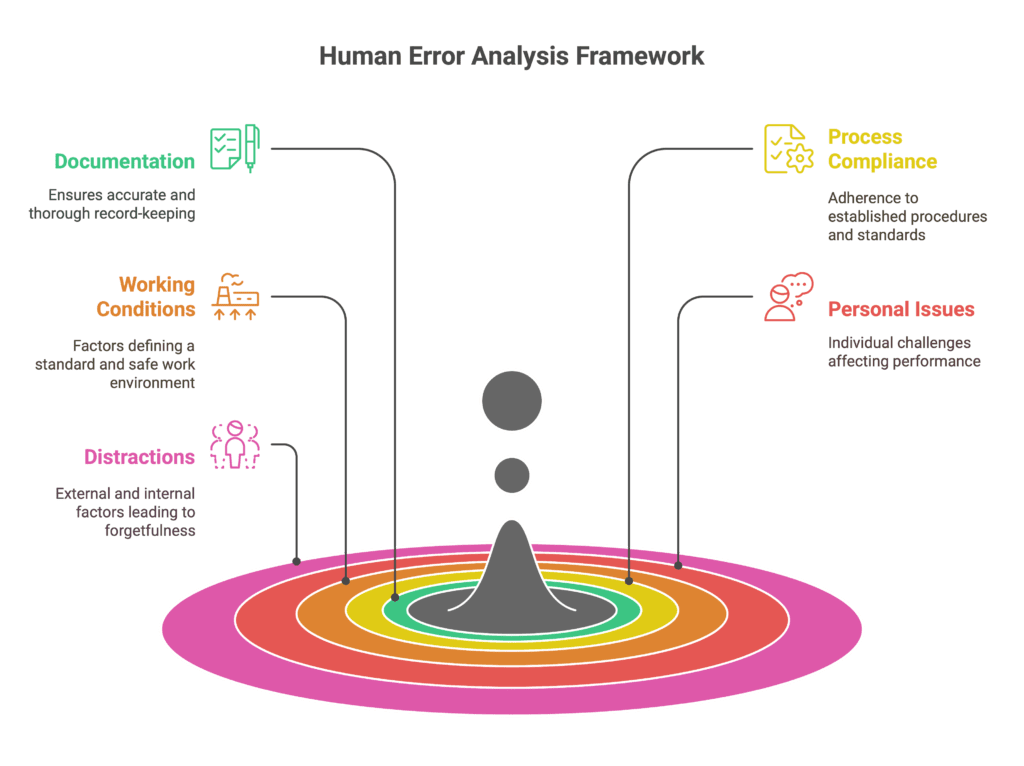
So, what should be checked in the “human” category? Here are a few ideas.
Superficial Training
If you’re a production manager or leader, you must understand that thorough initial training can be crucial during an employee’s early phase of work.
It’s not advisable to take a superficial approach, asking operators to “just sign the training documents—you’ll learn the rest on the job.” Even worse is skipping initial training altogether.
One of the best systemic solutions is conducting initial training outside the production area—such as implementing a DOJO.
The Work Instruction will tell the truth
Training on work instructions is one thing, but what they actually contain is another. An example:
Below is a graph showing the trend of one characteristic. A customer reported defects in 14 parts, which were marked with a red oval after analysis.
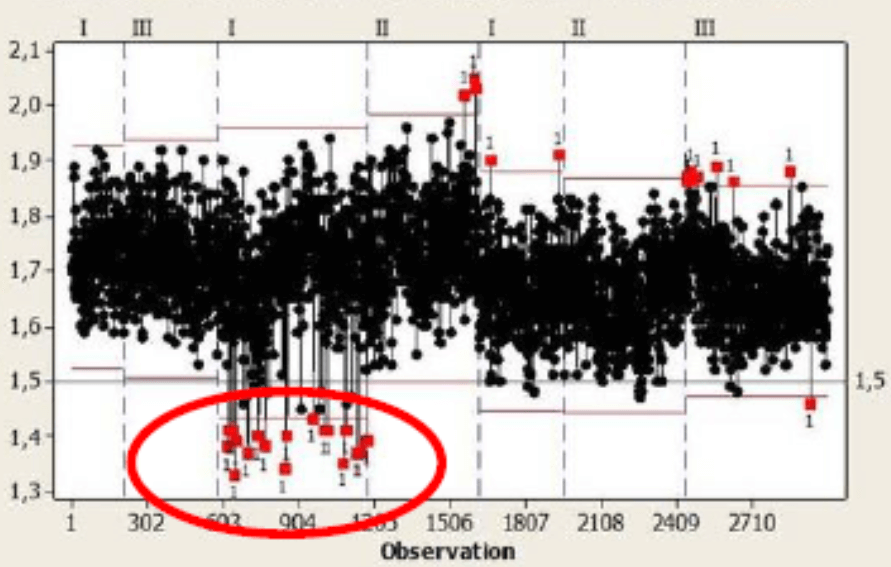
Why? The analysis revealed that the issue was linked to a vague description of an action: “install the component into the housing.” This led one operator to perform the task differently from the other shifts, but still in accordance with the work instruction.
The ultimate systemic solution was to add a positioning tool that ensured consistent component placement during assembly, guaranteeing repeatability of the operator’s actions.
Limited space between container and next layer on the rack
When designing a production line, the project team should focus not only on the process itself but also on the input elements. This includes racks and the space between packaging and the next rack level.
We conducted this type of analysis due to warranty claims related to electrical errors caused by damaged sensor boxes.
Once again, the defined symptom was “operator error,” but, as you might guess, we did not stop there. We looked deeper to understand what lay beneath the “tip of the iceberg.”
It turned out that the problem was the insufficient height between the container and the next rack layer. The limited space caused the operator to hit the sensor box against the rack while retrieving components, damaging it.
Systemically, we increased the distance between container levels and updated the Process FMEA.
If you’d like to learn more about human error root cause analysis, we invite you to attend our dedicated training session.
Dariusz Kowalczyk