In the work of a quality specialist, especially in the industrial sector, continuous process improvement and problem-solving are essential elements. One tool that can help with this is the Gemba Walk.
Although this term is well-known in the Lean Management philosophy, its proper application requires understanding not only the theory but also the practice. In this article, we’ll present how to effectively conduct a Gemba Walk, what can be achieved with it, and what benefits it can bring to quality management.
What is a Gemba Walk?
Gemba is a Japanese word meaning “the real place” or “the place where work happens.” In the context of quality management, a Gemba Walk is a practice where you visit the place where value is actually created β the production floor, warehouse, or assembly line.
This action differs from typical audits. Why? Because its goal is not control but observation, understanding, and supporting the team in solving problems.
The main principles of this practice are:
- See: Observe live processes and pay attention to potential deviations.
- Ask: Talk to employees to understand what challenges they face.
- Act: Collaboratively find potential solutions and implement them.
Why does Gemba Walk matter in the industrial sector?
In the industrial sector, especially in the automotive industry, even small deviations can lead to serious consequences. For this reason, among others, organizations must implement quality management systems according to ISO 9001 or IATF. However, the Gemba Walk allows for real-time monitoring of actual activities and their impact on the final product.
What are the main benefits of implementing Gemba Walk?
- Faster problem detection β On the production line, it is easier to notice minor process irregularities.
- Building trust β Regular management presence on the production floor can build better relationships with the team, fostering open communication.
- More effective problem-solving β Understanding the root cause of a problem in real working conditions allows for more accurate and faster solutions.
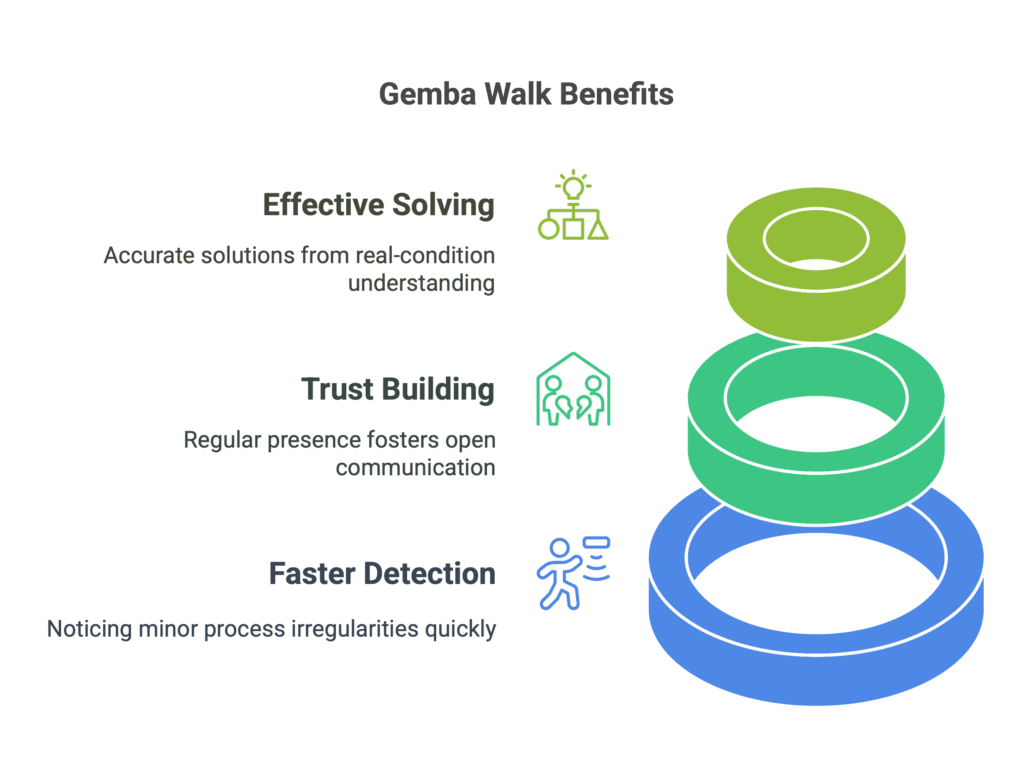
How to effectively conduct a Gemba Walk? β Practical tips
1. Plan wisely Before deciding on this practice, ensure you know what you want to achieve. Is your goal to understand a quality issue, improve workflow, or identify waste? Having a specific objective will help you better guide your conversations and observations.
2. Ask, donβt judge When you notice a problem or deviation from standards, donβt approach with a ready-made solution. Instead, ask employees what they think might have caused it and what solutions they propose. This is crucial because those working directly with the process have the most knowledge of on-site realities.
3. Focus on the process, not people Gemba Walk is not an evaluation of employee efficiency but an analysis of processes. Your goal is to understand how systems, procedures, and tools function, not to assess individual performance.
4. Document and act. You should end each Gemba Walk with a brief summary, and then implement the key findings and observations into corrective actions. A good idea is to combine the Gemba Walk with problem-solving tools like the 8D Report, QRQC (Quick Response Quality Control), or A3. This way, you will gain a structured methodology for implementing changes.
5. Consistency matters Gemba Walk should become a regular part of the work culture, not a one-time activity. Regular visits to the “Gemba” help maintain smooth communication and support continuous improvement.
Case Study
In one automotive component manufacturing plant, regular Gemba Walks helped identify a quality issue with parts installed on the final production line. The problem turned out to be low-quality components from one supplier, which initially went unnoticed in standard quality audits.
By using the Gemba Walk:
- Observation: It was noted that faulty components directly impacted production efficiency.
- Conversation: Discussions with employees revealed that defective parts were not properly labeled in the production process.
- Action: An additional quality control stage was introduced for parts from this supplier, and communication between the procurement and production departments was improved. Of course, this was a temporary measure. Ultimately, the supplier quality management team took over the issue.
As a result, complaints dropped by 30%, and production line efficiency increased.
Conclusion
As you can see, this is a powerful tool in the arsenal of a quality specialist, especially in the automotive industry, where precision and quality are crucial. Regular process observations, open communication with employees, and systematic implementation of improvements can bring tangible benefits in the form of higher product quality, fewer errors, and greater team engagement.
Remember, the most important thing in a Gemba Walk is to approach it with an open mind and a desire to collaboratively solve problems.
Now itβs your turn!
Do you regularly conduct Gemba Walks in your company? Or are you just planning to introduce this practice?
Kinga Niedziela