Machine breakdowns are certainly a nightmare for any production manager. Can we reduce the number of breakdowns? Can a machine operator perform most of the tasks related to the machine without calling maintenance staff? We answer these questions by presenting another Lean Manufacturing tool – TPM.
What is TPM?
TPM (Total Productive Maintenance), or comprehensive, productive maintenance, has the main slogan “zero unplanned downtime.” The concept was developed in Japan in the 1960s.
It is a continuous process that involves all employees through Productive Maintenance leading to the optimal use of machines. Progress is measured using the OEE (Overall Equipment Effectiveness) indicator, which combines work efficiency, machine reliability, and manufacturing process quality.
Differences Between Traditional Maintenance and TPM
A key difference in companies using TPM is the involvement of production employees in performing maintenance tasks on machines. The table below presents other differences.
Main Goals of Total Productive Maintenance
- Achieving production stabilization through planned maintenance operations.
- Reducing company costs.
- Achieving the highest possible efficiency in the use of machines throughout their entire lifespan.
- Enhancing employee qualifications.
- Eliminating production losses, thereby increasing the OEE (Overall Equipment Effectiveness) indicator.
Pillars of Total Productive Maintenance
The structure of TPM is presented as a temple, whose foundation is the properly implemented 5S and the vision of three zeros (zero accidents, zero defects, zero breakdowns). The pillars of TPM are:
- Autonomous Maintenance – involves engaging operators in the independent maintenance and adjustment of machines. This primarily increases employee awareness and competence, allowing for quicker detection of irregularities.
- Planned Maintenance – with minor repairs and adjustments performed by production employees, the maintenance department can focus on more advanced tasks that are properly planned.
- Early Maintenance Planning – based on acquired experience, we make informed decisions regarding the modernization or purchase of new equipment.
- Training – activities related to enhancing personnel qualifications through the implementation of a training plan.
- Improvement – in the spirit of Lean, seeking new, better solutions to improve our current standards.
- Quality Assurance – eliminating defects through ongoing monitoring and resolving quality issues.
- Communication – primarily aimed at improving the flow of information within the organization.
- Safety and Environment – all undertaken actions must be safe for employee health. Additionally, we should make efforts to minimize environmental impact.
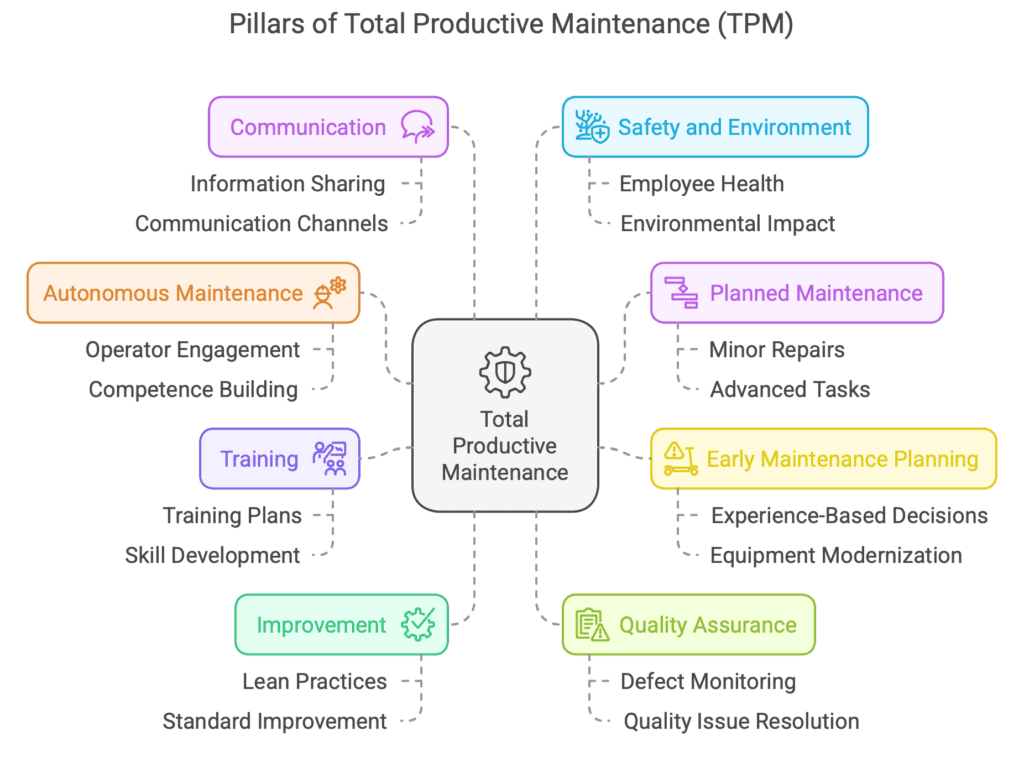
OEE – The Main Indicator of TPM
The indicator defining the progress of Total Productive Maintenance is OEE (Overall Equipment Effectiveness), which consists of:
- Availability – the ratio between planned time and the actual time available (total time minus changeovers, breakdowns, adjustments, cleanings).
- Performance – the ratio of productive time to available time, reduced by losses associated with operations performed.
- Quality – the ratio of good products to defective ones.
OEE = Availability x Performance x Quality
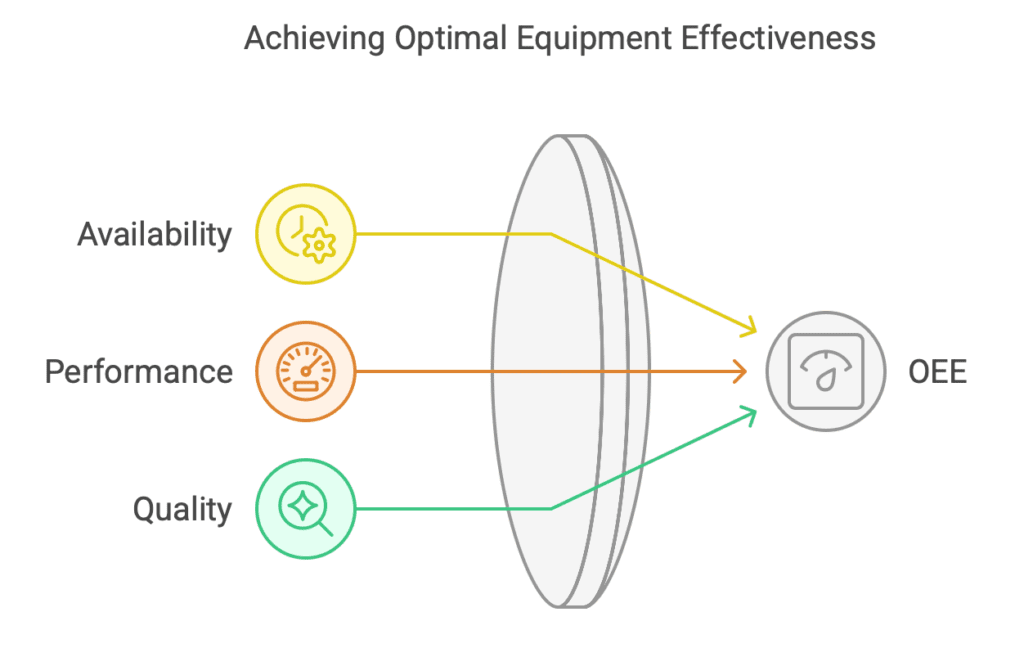
Benefits of implementation
- reduction of costs related to machine breakdowns
- increase in the OEE indicator
- improvement in quality
- skilled personnel
We also need to mention the investment involved in implementing this activity. The key aspects to consider when deciding on its implementation include:
- awareness that the foundation of TPM is 5S
- time (employee training, preparation of standardized instructions, cards, boards, planned maintenance time)
- establishment of a spare parts inventory
Łukasz Powszek