Read Across involves creating a single system within the organization to systematically share Lessons Learned among production facilities. The goal is straightforward – continuous improvement of the manufacturing process and product design.
The basic idea behind Read Across is to establish an environment that facilitates the exchange of all stages of reported cases among individual production plants. Within RA, only cases for which appropriate corrective actions have already been implemented should be considered.
Additionally, ensuring that system management focuses centrally is essential. This allows for the definition of a common denominator in this action and avoids situations where plants operate as isolated “islands” without knowledge of what is happening in other locations.
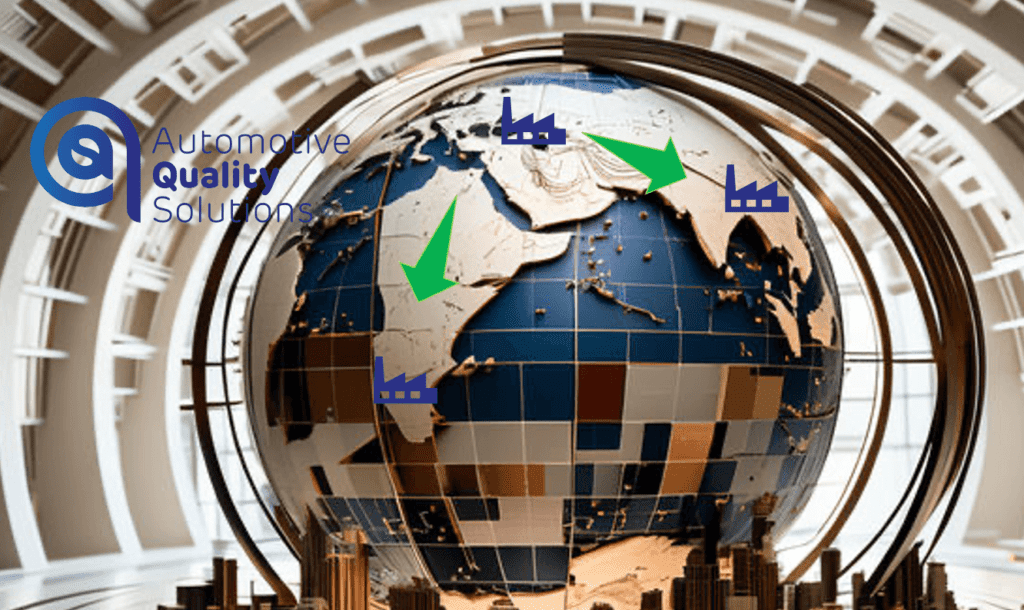
This provides us with a broader perspective on the functioning of individual production plants, enabling us to consider the implementation of actions, especially when a given process may potentially impact the generation of quality issues.
It is easy to understand that Read Across helps us identify and share Lessons Learned implemented across the organization’s facilities. This, in turn, minimizes the risk of similar issues occurring in other production areas and supports the continuous improvement process.
Read Across gathers data from various sources
Including:
– Engineering
– Internal notifications from production facilities
– Actions initiated by our suppliers
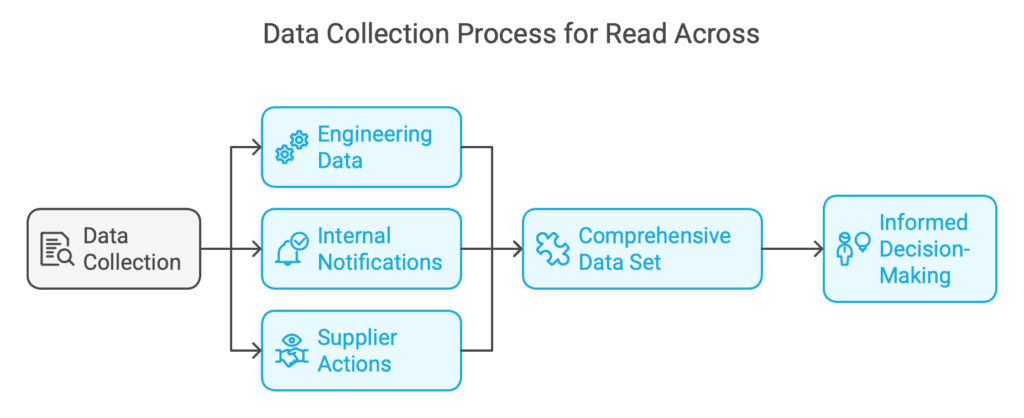
It’s important to note that this is not a problem-solving technique like, for example, the 8D Report, A3, or QRQC. In addition, documenting RA within the quality management system is not necessary. And most importantly, it’s not just a repository for storing Lessons Learned.
Having Lessons Learned won’t benefit us if we don’t take a broader look at our organization’s actions. It is through such actions that we can connect all the dots and ensure that corrective actions are not only taken by one facility but also by those where the same production processes, projects, or subcomponents are present.
What are the criteria for reporting Read Across?
The initiation of a RA report can be based on quality issues such as:
– Identified during internal or external audits
– Reported by a supplier
– Indicated by a customer
– Occurring during the production process
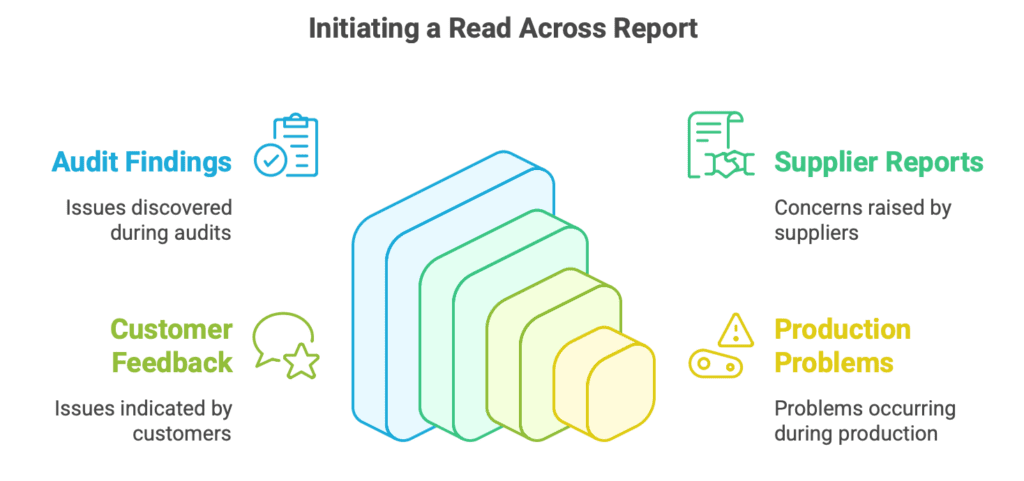
There is also one particular case when our organization should initiate RA.
These include reports (internal or external) related to non-compliance with requirements for Critical Characteristics. In this case, the organization’s interest is to verify whether a given problem may occur in other facilities.
Working in the automotive industry, you may also encounter a scenario where the customer directly asks us to check if the problem reported by a competitor is occurring in our facility. I encountered such a situation while collaborating on one of the launches with GM client.
Benefits of Implementation
The main benefit is that Lessons Learned have a follow-up in terms of checking their application in other facilities. This also greatly fulfills the practice of Best Practice.
By reducing potential complaints and preventing their recurrence, our actions have a tangible positive impact on financial indicators.
Can it be used for every part produced?
Not necessarily. More precisely, we use it for similar product families within our organization’s portfolio. In other words, we don’t use bumpers RA to verify implemented actions from fuel lines.
And what does Read Across look like in practice?
Let’s assume we have 4 production facilities manufacturing products from the same family. A quality issue has arisen in one of the four facilities, and we have already implemented appropriate actions.
So, we have a ready “case” under Read Across. At this step, remember to ensure that it meets the requirements consistent with the reporting criteria. Then, we send the reported data to the remaining three facilities. For what purpose? To verify its applicability.
In the end, we receive information that facilities No. 1 and No. 2 have implemented appropriate actions, while in facility No. 4 they are not applicable. For example, due to a newer technological solution.
The meetings themselves can be conducted based on information placed in the appropriate database or xls file.
Dariusz Kowalczyk