Additional Quality Requirements are one of the key documents provided by the client as part of the sourcing package. Historically, organizations primarily utilized them in collaboration with xFCA. However, following the establishment of the Stellantis group in partnership with PSA, these requirements now apply to both clients.
What is the purpose of Additional Quality Requirements?
One of the main challenges encountered during new launches is the lack of awareness among the component-producing plants regarding the existence of AQRs. This is often because the central units, such as the sales department, classify this document as an RQF (Request For Quotation) without disseminating it to the production plants.
This approach can lead to complications during Progressive Planning Qualification or Mass Production Audit (PPQ and MPA). These documents have replaced the Advance Quality Planning and Process Audit methodologies previously used by FCA.
So, what exactly do Additional Quality Requirements entail? They can be categorized as process requirements derived from Lessons Learned and best practices specific to particular product families. They encompass areas such as specific requirements related to:
- Product
- Process
- Control and measurement devices
- Tests and controls defined for the process and product
- Traceability
- Sub-supplier management
- Packing
This implies that car seats will have distinct requirements, electrical harnesses will have their own set of requirements, and braking systems will also have unique specifications. Currently, there are over 230 such requirements.
It’s worth mentioning that the AQRs previously utilized by FCA were labeled with “AQ.xxxxx”. These documents have now been standardized across the Stellantis group, resulting in a minor name change to “AQR.xxxx”.
What sets apart the new revisions of the Additional Quality Requirements?
In addition to the procedure number known to suppliers who have previously collaborated with FCA, there is now a separate procedure number for suppliers who have previously collaborated with the PSA group.
For instance, the pressing process procedure number is AQR.00011 (for xFCA) and number 01598_23_01136 (utilized for xPSA). Additionally, is introduced the term “STELLANTIS HARMONIZED”. This indicates that irrespective of whether we collaborate with one or the other client, we will always adhere to the same Additional Quality Requirements.
Detailed guidance on how to implement AQRs is outlined in the GSQN.006 Global Stellantis Additional Quality Requirements Procedure (01746_23_00088), which has been available since November 30, 2023. It replaces the SQ.00001 document previously used in collaboration with FCA.
Why should a manufacturing plant undertake an Additional Quality Requirements assessment?
During the sourcing phase, the supplier should meticulously examine the submitted AQR. Signatures of the following confirm this:
- Representative from the sales department,
- Project or Engineering Manager,
- Quality Manager.
The first two individuals are often located outside the production plant.
Organizations approach the role of the Quality Manager in two ways:
- it could be a person located in the central department, or
- this could be the Plant Quality Manager situated in the production facility, designated to produce components after the project has been assigned by the client.
In the latter case, the implementation team at the plant should thoroughly analyze the document. This responsibility doesn’t solely fall on the Quality Manager. By doing so, we’ll have the opportunity to provide our input and align on a common strategy with the central department regarding any open issues.
The plant quality manager carries additional responsibilities. This is due to potential conflicts of interest that may arise. While conducting process audits, I encountered a situation where the quality manager of the production plant had signed AQRs, but upon verification, it was discovered that not all elements had been implemented.
He signed the document without proper analysis under the threat of losing business for the organization. Hence, regardless of the intentions of the central units, I strongly recommend carefully analyzing the AQRs within your team. Thorough consideration before signing is essential.
Workshops with Central Departments
From the perspective of the production plant, the optimal solution is to organize joint workshops at the location where the client plans production. This approach allows us to directly verify each requirement on the production line with the central units.
By doing so, we can prevent a situation where the implementation team at the plant disagrees with signing the document centrally. Failure to align on this matter may result in non-compliance during the PPQ and MPA conducted by the customer representative.
Additional Quality Requirements in Relation to CSRs
We currently define AQRs as Customer Specific Requirements for the xFCA group. IATF requirement “8.2.2 -Determination of requirements for products and services” addresses this activity.
During an audit by a Certification Body, auditors may inquire about how we implement these CSRs and request evidence. In such situations, presenting the Additional Quality Requirements received from central departments with the signatures of appropriate representatives is typically sufficient.
When conducting training on the correct interpretation of CSRs for a Stellantis xFCA client, I frequently encounter the question: “Why does the document only contain signatures from our organization and not from the client?”
Our organization, specifically the sales department, uploads the signed document to the GST system (Global Sourcing Tool), where the client conducts electronic verification. As a result, physical signatures are not present.
Although the production plant does not have access to this database, an individual with access to esuppplierconnet can request permission to view it.
In such cases, I recommend presenting AQRs from the GST database during audits at Remote Locations, which typically include the sales department. On the IATF certificate of the manufacturing plant, “Sales” often identifies this department.
Currently, xPSA does not impose such requirements under CSR. However, it is essential to identify them as part of the Customer Requirement analysis process.
Mass Production Audit in Relation to AQRs
The Stellantis group utilizes the MPA as an audit form to verify the production process. In the current version, the requirement to check AQRs appears in several areas, including:
- Verifying whether the organization analyzed the appropriate AQRs when developing control and measurement devices
- Ensuring compliance with specified requirements
- Checking whether the PFMEA incorporates information from the relevant AQR.
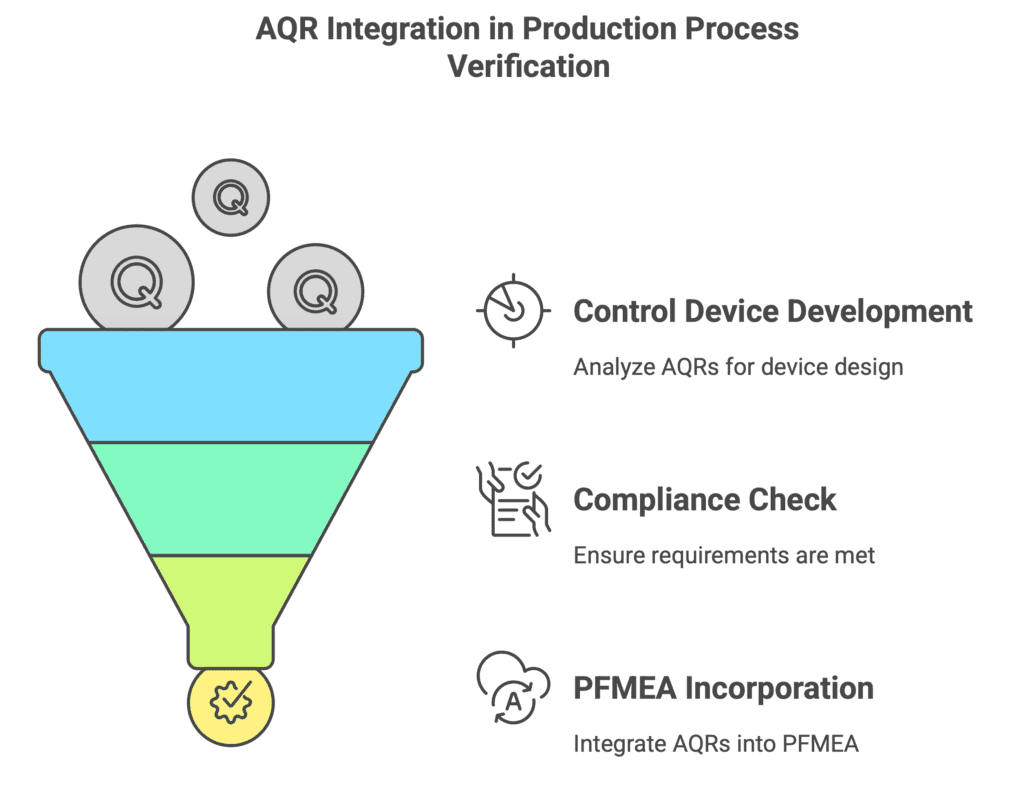
In summary, xPSA has adopted Additional Quality Requirements from xFCA. Therefore, when launching new operations, organizations should pay close attention to the proper management of Additional Quality Requirements. Additionally, effective communication with central services is crucial.
Furthermore, we cordially invite you to participate in dedicated training sessions covering this aspect of cooperation with the Stellantis group Stellantis xFCA Customer Specific Requirements management according to IATF
Dariusz Kowalczyk