In today’s global economy, product quality plays a pivotal role in the success of any company, particularly in the automotive industry. Customers expect increasingly higher quality standards, and competition is fierce. Therefore, the role of the Supplier Quality Engineer becomes exceptionally significant.
The Supplier Quality Engineer serves as a crucial link in ensuring that products supplied by sub-suppliers meet the highest quality standards.
However, individuals considering a career in this position should be aware that they will essentially serve as an interface between the production plant and the supplier. Moreover, this role carries more responsibility when working for an automotive supplier compared to a car manufacturer (OEM).
Drawing from personal experience working as a supplier quality engineer for FCA (currently Stellantis group) for nearly eight years, I can attest to the significance of our role as a customer’s quality representative. This position affords us greater leverage in enforcing corrective actions from suppliers upon detecting non-compliance.
Supplier Quality Engineer β between a rock and a hard place
This is further facilitated by the fact that no location within the organization wants to be singled out for client-initiated escalations, which may necessitate external support. Consequently, implementing activities initiated by a manufacturer’s SQE (Supplier Quality Engineer) for a Tier 1 supplier is generally easier compared to Tier 1 to Tier 2 scenarios.
Working as a supplier quality engineer from the perspective of a component manufacturing plant is considerably more demanding and complex. I’ve often encountered situations where “our” SQE negotiated with the supplier to adjust the production process to the upper tolerance limit, typically due to issues with interface components.
This adjustment inevitably leads to increased costs, which brings us to the next topic – cost recovery for quality problems.
Unlike the manufacturer’s (OEM) SQE, who is not responsible for this aspect, as it falls under:
- the client production plant β for handling complaints and selection costs
- the customer purchasing department – in cases of warranty-related issues
From the perspective of an SQE working for an automotive supplier, involvement in these activities is common, while other departments are typically not directly engaged. However, in problematic scenarios, reporting the issue to central units is essential.
Supplier Quality Engineer – Advantages and one drawback
An undeniable advantage of working as a supplier quality engineer is the exposure to diverse production processes. This experience serves as a valuable asset in enhancing one’s professional skills and knowledge. Over time, this knowledge can significantly contribute to internal advancement or career opportunities in other organizations.
Personally, I have gained in-depth insights into various processes, including:
- Plastic processing techniques such as injection molding, blow molding, and extrusion
- Methods of plastic joining including hot plate, vibration, and ultrasonic welding
- Assembly processes for components like bumpers, car seats, fuel tanks, roofs, and dashboards
- Innovative technologies such as laser welding for car metal seat structures and dashboard instrument panels. Particularly in critical areas like the passenger airbag deployment zone
- Thermoforming applications for acoustic components
- Bitumen production processes
- Painting techniques for dashboards and bumpers
- Vulcanization methods for rubber hoses
This diverse exposure not only enhances professional expertise but also broadens career prospects in the field of supplier quality engineering.
Protip
Here’s a helpful tip from me: if your responsibilities involve managing complex products, consider requesting product training from your suppliers. I learned this strategy from one of our colleagues in the department.
This approach allows you to gain in-depth knowledge of the products you’ll be managing, especially concerning new launches and implementing changes in current production. It’s a win-win situation as the supplier benefits by initiating the first step toward building a long-term relationship with the customer’s representative.
Moreover, if you’re dealing with similar components from multiple suppliers, you can leverage benchmarking between them. This accelerates your path to becoming an expert in your role compared to other positions.
To dispose or not to dispose β that is the question?
Many times, upon arriving at the office, I received urgent requests to visit a supplier within the next two hours, often due to quality problems. These visits frequently involved traveling abroad. Additionally, overtime work was not uncommon; I once completed work at a supplier’s production plant after midnight, while a teammate spent over 40 hours with “his” supplier resolving quality issues.
When contemplating starting a family, one must carefully weigh the decision to continue working in this position, considering its implications for work-life balance and family life.
Supplier quality engineer β TOP 10 key competencies
A supplier quality engineer should possess a variety of competencies to effectively manage and ensure supply quality.
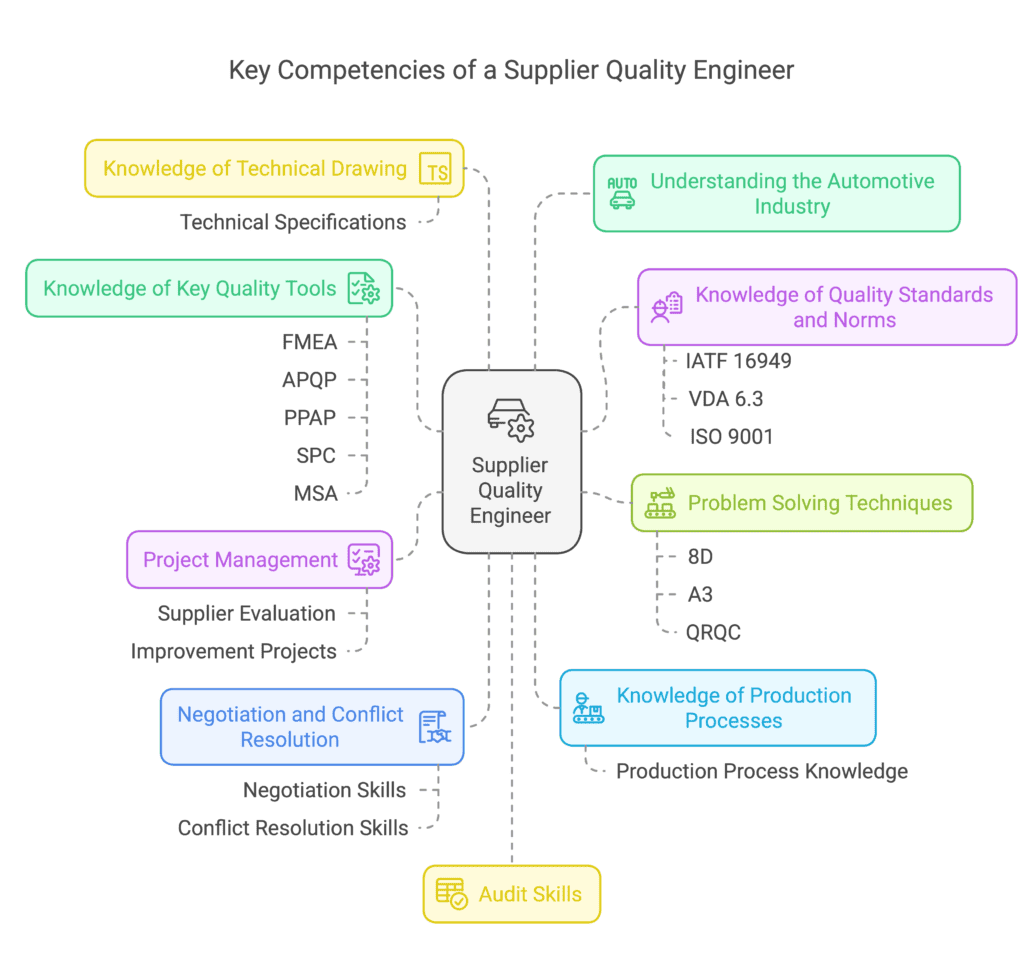
Below, I have listed those that, in my opinion, are the most important:
Understanding the automotive industry: Knowledge of the specifics and requirements of the automotive industry is crucial for effective cooperation with suppliers.
Knowledge of quality standards: Understanding norms and standards such as IATF 16949, VDA 6.3, and ISO 9001 is essential for assessing and ensuring supplier compliance.
Audit skills: Ability to audit suppliers, verify their processes, and identify areas for improvement.
Excellent communication: Effective communication is extremely crucial when solving problems and clarifying quality requirements.
Knowledge of key quality tools.Β The ability to use FMEA, APQP, PPAP, SPC, MSA allows for effective management and improvement of production processes. By understanding and applying them correctly, one can identify potential risks. Additionally, they can monitor and verify the quality of delivered products in relation to customer milestones. Especially during the launch phase. This ensures compliance with quality requirements.
Problem-solving techniques (8D, A3, QRQC): These techniques are employed to effectively identify the sources of problems and their causes in the delivery process. This enables the introduction of appropriate improvements, resulting in a more effective and reliable supply chain.
Project Management: The ability to effectively manage supplier evaluation and improvement projects.
Knowledge of production processes: This is a crucial topic. If you are becoming an SQE for a supplier with a production process you are unfamiliar with, ensure that your development plan includes the necessary training provided by the organization. It’s essential to acquire the knowledge and skills needed to excel in your new role.
Knowledge of technical drawing: Technical drawings are the primary means through which designers and engineers communicate technical specifications of products and parts. As an SQE, understanding these specifications is key to assessing whether delivered products meet specified quality standards.
Negotiation and conflict resolution: The ability to negotiate with suppliers and resolve conflicts that may arise in the cooperation process.
Summary
As you can see, the position of a supplier quality engineer can serve as a significant stepping stone in one’s professional development. Furthermore, considering that the automotive industry operates globally, there is a high likelihood of collaborating within international teams.
This environment fosters the opportunity to learn a foreign language and enhance flexibility in cooperating with individuals from diverse cultural backgrounds. Ultimately, this facilitates networking and relationship-building with a variety of people, which can prove invaluable in the future.
Dariusz Kowalczyk