A safe, ergonomic, and standardized workplace is undoubtedly where an employee can perform their duties most effectively.
One of the fundamental tools associated with Lean Management is 5S, which, when fully implemented, allows for the creation of an optimal work environment.
What is 5S?
The 5S workplace organization system aims to establish and maintain clean, safe, and ergonomic workspaces to ensure seamless operations.
1S Sort
The first step involves assessing the workplace to determine the necessity of tools and materials. It’s crucial to ask whether each item is essential for daily operations, consulting those who work in the respective positions. This step follows the basic principle of optimization workshops: we retain only what we need, in the required quantity, and when necessary.
2S Set in Order
Once we’ve completed the first step and identified the necessary tools, we must consider their optimal arrangement. Common sense should guide us; items frequently used should be easily accessible. Initially, we can sketch out the layout and observe whether it aligns with natural workflow. You can make adjustments as needed.
3S Shine
Having completed the first two steps, it’s time to rejuvenate the workspace. This phase involves bringing everything to its best condition, from updating labels and lines to cleaning tools and arranging for repairs if needed. We should also consider waste reduction. For instance, using devices to minimize debris during tasks like welding. Cleaning procedures should address what, who, how, with what, and when to clean.
4S Standardize
We must document all efforts thus far in clear, understandable standards. This is the stage for creating visual aids, cleaning schedules, and specifying cleaning responsibilities. If it wasn’t previously required, employees should now be informed, for instance, that they’re to clean their workstations according to instructions 10 minutes before the end of their shift.
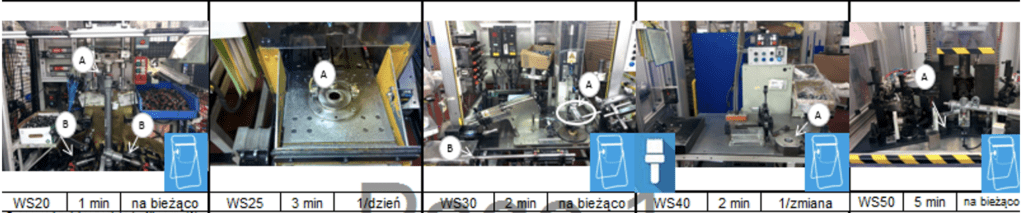
5S Self-Discipline
The final step of the 5S methodology is to integrate all previous steps. This stage involves working with the team to establish habits that naturally align with the implemented solutions. It’s arguably the most challenging step, requiring the active involvement of top management.
Consider implementing an additional activity related to conducting 5S audits. Sample questions for these audits could include:
- Has the previous audit been completed?
- What is the status of component identification in production? Is it maintained?
- Is operator wearing appropriate protective footwear and clothing?
- Are protective clothing items clean and in good condition?
- Are indicators (e.g., scraps) being filled in properly and consistently?
As with any other implementation, we should initially conduct the 5S audit in a pilot area. Only after we validate the question list should we extend it to other areas within the company.
Benefits of Implementing 5S
The implementation of 5S yields numerous measurable and intangible benefits, including:
- Improved workplace safety and ergonomics
- Cost reduction through waste elimination
- Enhanced production quality and efficiency through standardized processes
- Space savings through the reduction of unnecessary items and materials
- A clean production hall serves as a positive representation of the plant
- Acts as a preventive measure against quality problems
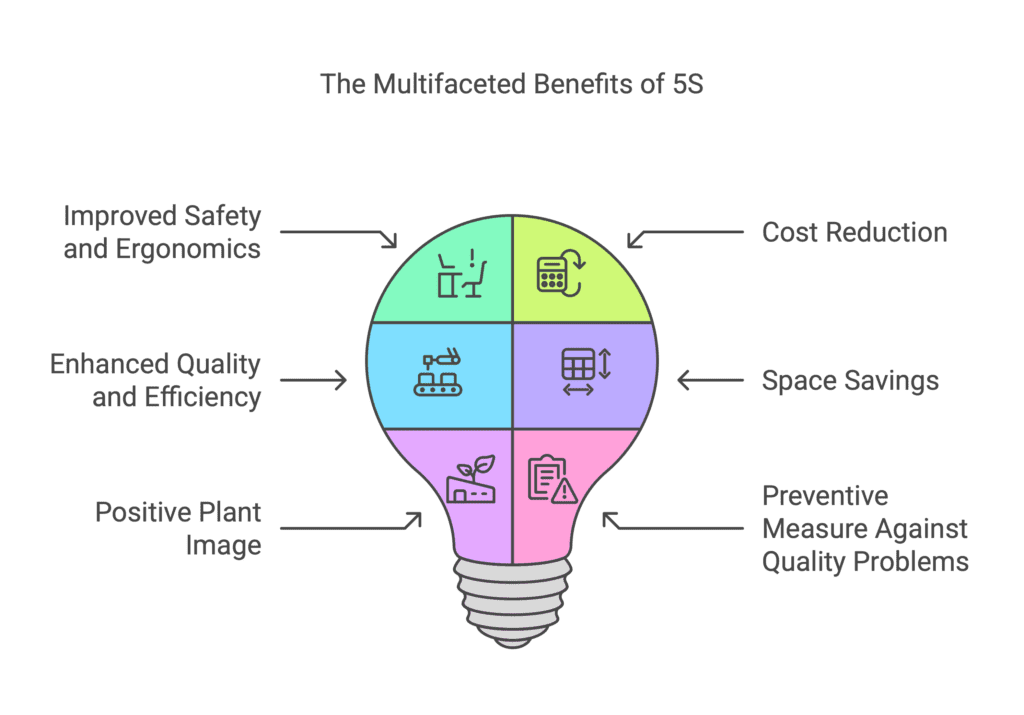
What else do we need?
Time and money are invested in staff training, cleaning, creating and implementing new standards, and purchasing the necessary tools and cleaning products. In the initial phase, it is also worth considering implementing meetings aimed at raising employee awareness. Active management involvement is crucial.
5S summary
At first glance, 5S seems like a straightforward tool. After all, what could be difficult about eliminating unnecessary items from the workplace and setting new standards? However, implementing 5S sometimes rushes and lacks involvement from key stakeholders, leading to skipped steps, which is where challenges often arise.
Some companies may boast about their 5S system, which may primarily consist of purchasing cleaning equipment and achieving cleanliness at the time of planned audits.
However, true success in implementation depends on the commitment of all employees to embrace change, support from top management, and a dedicated team to consistently introduce, monitor, and improve the new standards.
Lukasz Powszek