A Customer Quality Engineer is one of the most important roles in a production facility because it combines cooperation with the customer’s quality representatives and the organization’s team members.
When preparing to start working as a Customer Quality Engineer, it’s worth learning about the main competencies that affect work efficiency.
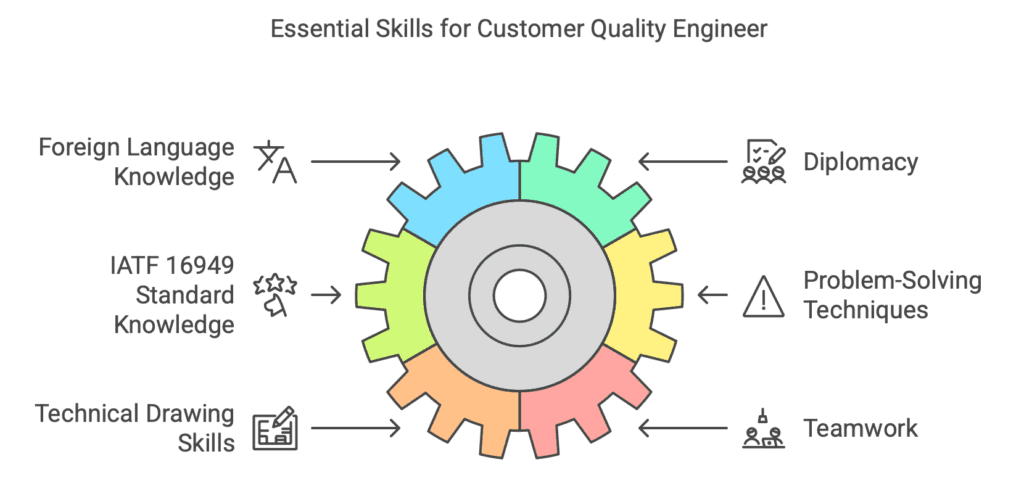
Foreign language knowledge
This is not a new discovery by any means. The specificity of the automotive industry focuses on cooperation with people often located in different parts of the globe, from employees in engineering, purchasing, and central functions, to customer representatives. English is compulsory for this position.
Of course, the vocabulary of the automotive industry is different from what we use in everyday speech. For this reason, it’s worth knowing the most common phrases and terms that can be found in daily work. That is why I have prepared a free e-book,Β “200 english terms and abbreviations for Automotive Engineer“.
More and more often, the knowledge of one foreign language is insufficient. Therefore, in addition to English, it is worth considering learning another. In my case, for example, it’s Italian.
Diplomacy
Did you know that even incorrectly used vocabulary in communicating with the client can lead to escalation? I am a living example of this. After one of the meetings with the client, the conversation did not go as I’d like.
As a result, two minutes later, I had a call from my supervisor. Ten minutes later, the plant manager called me into the office, and half an hour later, I had an interesting conversation with the Quality Director from the central department. Overall, it was not my best day at work.
The first basic rule you need to know: never argue with the client. Even if you are right, it will eventually turn against you (as you can see, I know something about it). The most constructive solution is to ask to stop the meeting, explaining that we need to gather more information and propose to set a new date for the meeting to continue it.
The area of diplomacy is also related to the selection of appropriate vocabulary. I have compiled the most important of them below.
Part damaged outside the production facility
Above wording summarizes 0-km complaints and warranty returns. It refers to a situation where we confirm a reported problem but at the same time exclude the participation of the production plant.
Remember not to use words that suggest the part has been damaged at your customer’s manufacturing facility. It’s like a red rag to a bull and can be counterproductive to what we want to achieve.
Solution concept
In this term, the word “concept” is the most important. Why? Because it allows the organization to change its strategy when defining immediate or definitive action. The lack of this word closes the possibility of a flexible approach to its change during meetings with the client.
Initial condition lost
People most often use this phrase in the case of analyses from the warranty field. It refers to a situation where the claimed part is incomplete (some sub-components are missing). The second scenario when specialists can use this wording is when the dealer or customer causes parts degradation due to inadequate shipping or packaging conditions.
The use of this term informs the client that the analysis may end without conclusions. Additionally, in the event of repeated occurrences, it is worth defining a common strategy with the client for systemic actions that eliminate the possibility of such a scenario.
IATF 16949 standard – A must-have for Customer Quality Engineers
Due to the cooperation with a customer representative, a Customer Quality Engineer should know what IATF requirements affect their work. You will find them in the Process Card, which is prepared as part of the Quality Management System (QMS).
Customer Specific Requirements
Having identified IATF points for customer quality (external) area, we must remember that the vast majority of manufacturers have additional specific requirements (CSR – Customer Specific Requirements). They are published at www.iatfglobaloversight.org.
To ensure the use of current CSRs, it is worth setting up a subscription on the main page by entering your email address. Thanks to this, each time requirements are updated, such information will be provided to your inbox.
Problem solving techniques knowledge
This skill is useful not only in the workplace but also in private life. If you work as a Customer Quality Engineer, you know very well that one of your responsibilities is proper complaints management. The vast majority of clients will require an 8D approach for it.
Technical drawing
Knowing how to “read” a technical drawing (2D) is a key skill for a Customer Quality Engineer. It is useful for identifying Special Characteristics and defining measurements that have to be performed on parts dedicated for customer approval.
Often in such a situation, the term “drawing bubble” is used. It consists of marking dimensions with an appropriate outline. Additionally, the customer drawing contains information on traceability, recycling requirements, operator identification, and the drawing number.
Teamwork
Of course, you can learn teamwork, which is a critical skill. It is related to such terms as empathy (i.e., the ability to empathize with other people’s emotions), negotiation (e.g., arranging the dates of meetings), as well as diplomacy combined with respect.
Customer quality engineer – What else is worth knowing?
In addition to the abovementioned competencies, it is also worth having knowledge of:
- Core tools
- Driving license
- Working under time pressure
- MS Office knowledge
- Optionally managing the work of residents in customer locations
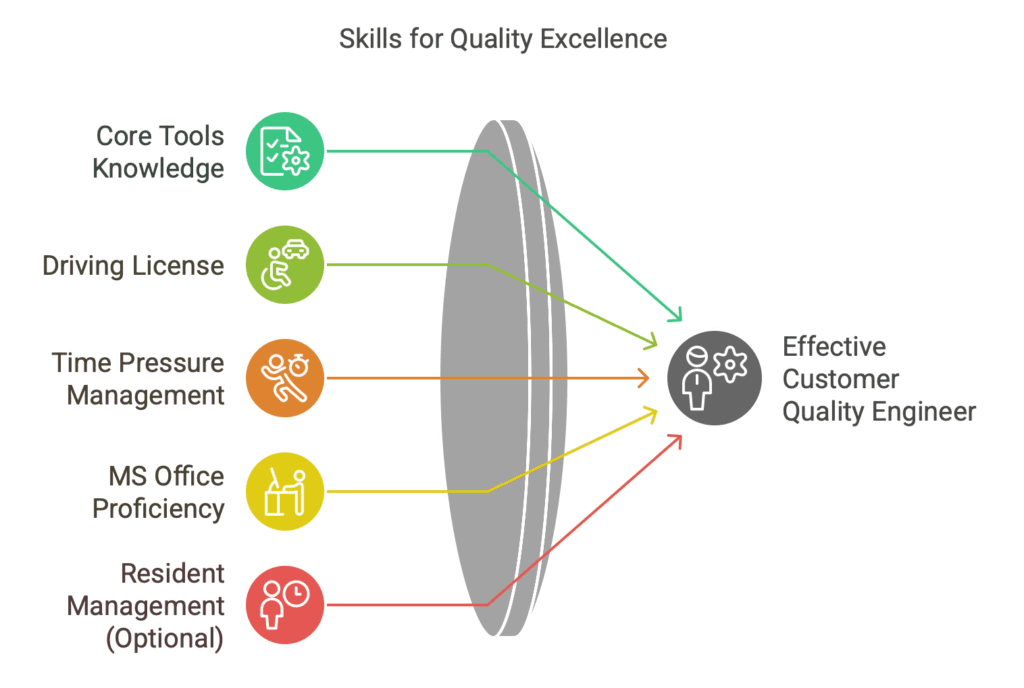
As you can see, it is a very demanding position, but at the same time, it gives a lot of satisfaction and the opportunity to learn and develop.
Dariusz Kowalczyk