One of the problem solving steps is the root cause definition. The double Ishikawa diagram offers an alternative to this phase of analysis, addressing two scenarios: why the problem happened and why it was not detected.
You should most often use this method in two scenarios. First, if there is an issue that affects safety and/or regulation. Secondly, if the problem concerns a large affected population of components sent to the customer.
Document structure
The document itself looks familiar, but it’s a little different from the standard approach. I first encountered this type of diagram while working as an OEM supplier, and I regret very much that I didn’t know this tool earlier.
Why? Because it gives us the opportunity to look at the problem from a different perspective, focusing on two areas closely related to Occurrence and Detection from PFMEA, namely:
- Why did the problem occur?
- Why was the problem undetected?
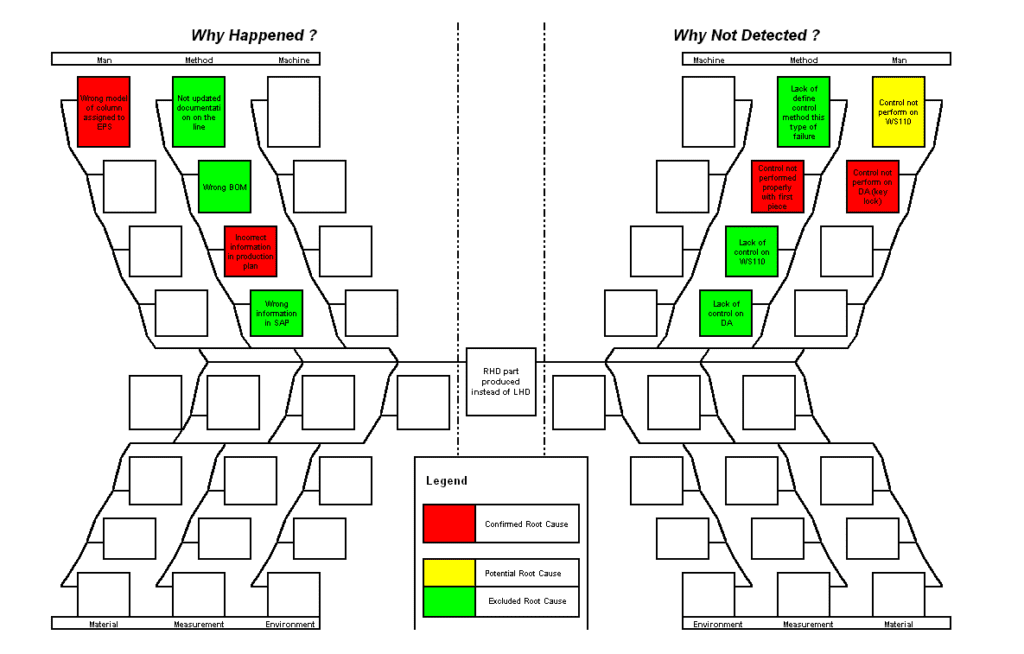
Thanks to this approach, we are able to more accurately identify all the causes that influenced the production of the defective product. Most often, as in life, we deal with a coincidence of several events that led to the problem.
In this case, we should apply appropriate prioritization – for example, using the 80/20 rule. In practice, the team should address up to three root causes.
Double Ishikawa Diagram – Benefits
The director of the facility where I work used to say to the problem solving team (not only for quality issues) ,“Show me your Ishikawa.” Why? By identifying how many factors there were, the team could see how much effort they had made and how much time they had spent on the analysis.
He didn’t expect the team to define 5 Whys for each identified cause. He was interested in the number of areas that the team examined. I encourage you to implement this approach at your facility as well. You will see how this can positively surprise you when it becomes your daily routine.
You can download an automatic, editable Excel form for free on the Free Quality Tools
Document name: Double Ishikawa for Why Happened and Why Undetected – Excel form
Dariusz Kowalczyk