Thanks to the 5xWhy method, we are able to define the real root cause, not just the symptom. This is important because symptoms often lead to containment actions, which are defined in step D3 of the 8D report.
How then to carry out such an analysis?
Step zero is to correctly complete the Ishikawa diagram. If we already know whether we are dealing with an incorrectly performed control, lack of its implementation, or poorly defined process parameters, we proceed to the 5xWhy method.
5xWhy – structure
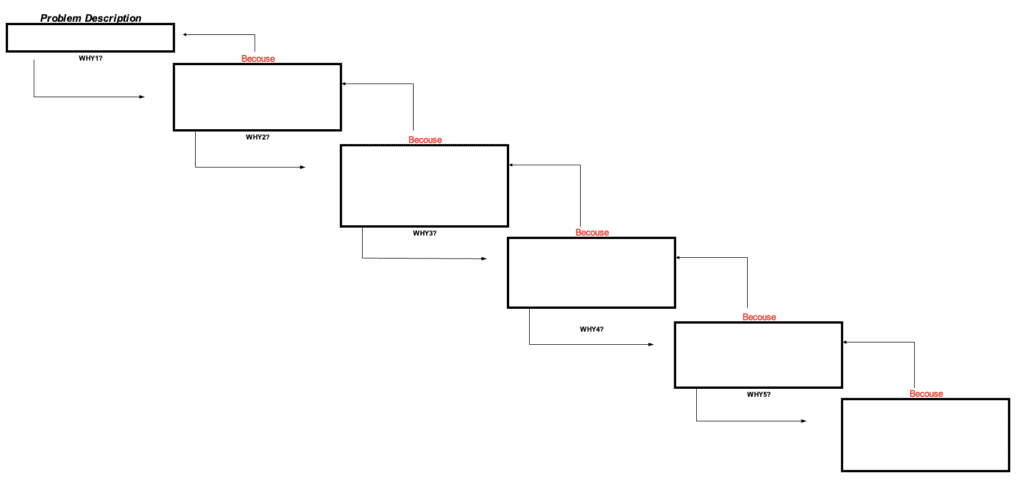
The structure of the method itself is very simple, as it consists of asking questions five times to most likely get to the root cause.
In theory, it seems easy, but in practice, it can be challenging because we can fall into several traps that significantly hinder progress:
5xWhy vs. 5 guilty
When conducting meetings in a team, we must be aware of the importance of the relationships within it. I have observed many times (even as a client’s representative) that during meetings, conversations move from the “content” level to the “emotional” level.
This shift occurs when participants focus not on solving the problem but on who didn’t do what and what it led to.
Teamwork – Not a “One man hero”
Group work is very important during 5xWhy analysis. Only through synergy and modifying the ideas presented by other participants can we gain a better view of the problem, allowing us to look at operational activities from different perspectives. One person alone cannot achieve this.
Quality of the team – Who should solve the problem?
Continuing the topic of teamwork, it should be remembered that unlike defining the Ishikawa diagram (which can include people from outside the production area), 5xWhy requires someone who knows the production process and technical issues.
This knowledge often emerges from the third “Why,” where the most common transition from general formulation to the technical area occurs.
Additionally, the team should include everyone who experiences the problem, not just the person reporting it. Most often, a quality person reports customer complaints or internal problems and organizes the team.
Objectivity: “It didn’t happen with us”
Maintaining objectivity and stepping out of the comfort zone are valuable traits for participants. It allows us to look critically at our process without delegating responsibility to other departments. I experienced this when I blamed a sub-component for a bent metal bracket, which turned out to be due to incorrect handling by the operator.
It was not the operator’s fault, as the production process design allowed for such opportunities.
5xWhy – Example
Below is an example of the 5xWhy method to help you understand the exact mechanisms between each question.
Problem: Unable to mount the instrument cover to the dashboard
Why (1):
Because the dashboard cover does not have the correct dimensions (it is too short).
Why (2) is too short ?:
Because the component cooling parameters were changed during the injection process.
Why (3) the component cooling parameters have been changed?
Because the parameters of the production process have not been password protected.
Why (4) parameters were not protected by the password?
Because after tests for the production of another product in the pre-launch phase, the process engineer forgot to activate the password for current production
Why (5) Why did the process engineer forget to activate the password?
Because the production software does not force such an action when changing parameters from the test cycle to the production cycle.
In this case, we see that the action to be introduced is software modification. It should ensure that when switching between test and production parameters, they are immediately unavailable for modification by production workers.
Another systemic action to implement is the modification of the checklist for production tests by adding the following questions:
- Have the parameters changed from test to process parameters after the tests finished?
- Has the process engineer activated the password for process parameters?
Benefits of the 5 Why Technique
-
Simplicity: Easy to understand and implement.
-
Cost-Effective: Requires no special tools or training.
-
Encourages Team Collaboration: Involves team members in the problem-solving process.
-
Promotes Continuous Improvement: Helps organizations identify and address issues proactively.
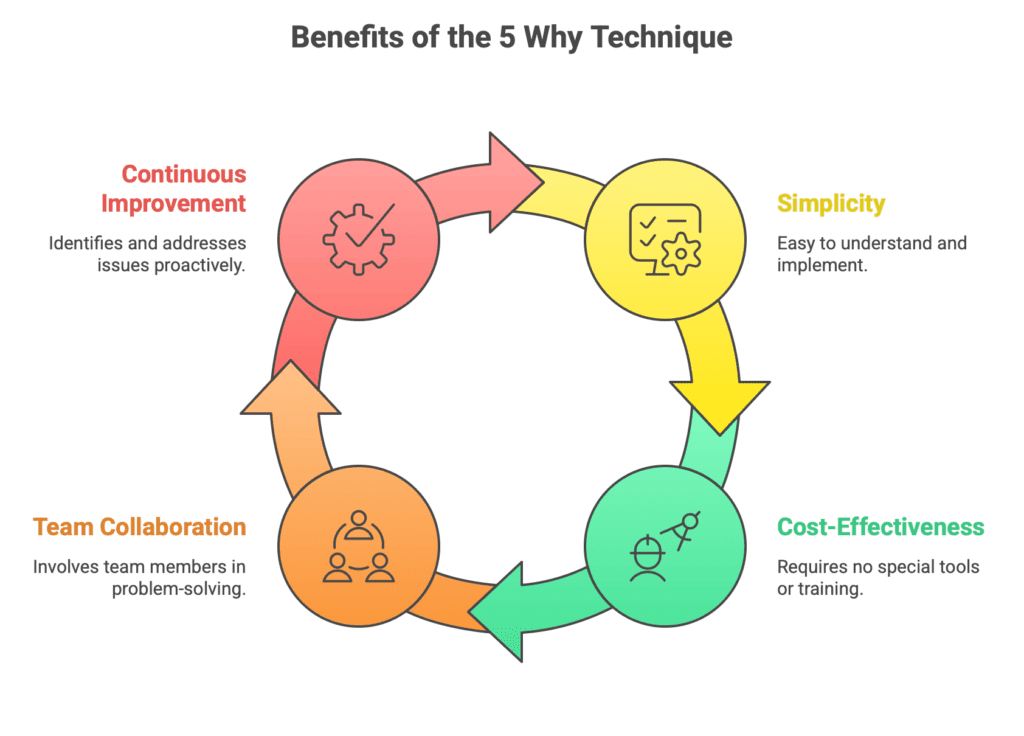
You can download an automatic, editable Excel form for free on the Free Quality Tools
Document name: 5Why β Excel form
Dariusz Kowalczyk