Working in the automotive industry requires familiarity with the terms and abbreviations commonly used in this field.
In the article below, we present the second part of our series: 50 English Terms and Abbreviations for Suppliers Producing Automotive Components. (The first part is available link and the second part at the link).
👉 Download our free ebook 200 english terms and abbreviations for Automotive Engineer
We hope this resource will be a valuable tool in your professional journey.
Glossary of Automotive Terms and Abbreviations
5S
A methodology for maintaining cleanliness and organization in the workplace. It includes five key steps: Sort, Set in Order, Shine, Standardize, and Sustain.
Action Plan
A documented plan outlining actions to address nonconformities identified internally or externally.
Assembly Line
A production line used to assemble components such as bumpers or car seats.
Appearance Approval Report (AAR)
A report required for aesthetic assessments. It is part of the product approval process and applies to grained, painted, or upholstered components.
Advance Product Quality Planning (APQP)
A structured process for planning product quality during development and pre-series production phases.
Countermeasure
A corrective action or solution implemented to resolve a problem.
Cycle Time
The time required to complete a specific task at a workstation.
Datum Point
A reference point ensuring proper positioning of a product on a gauge or another component.
Design Freeze
A milestone indicating the completion of design activities (e.g., DFMEA, final mathematical models), enabling the next phase, such as tooling development.
Deviation
A temporary departure from a defined standard, often referred to as a waiver or interim approval.
Downtime
Periods when production halts due to failures, lack of orders, or unavailability of components.
Electronic Data Interchange (EDI)
An electronic system for exchanging information between suppliers and customers, commonly used in logistics.
Emergency Response Action (ERA)
Immediate action taken in response to safety-critical notifications or widespread non-conformance issues.
Equipment Spare Part
A replacement part designated for production machinery or equipment.
Feedback
Information provided after identifying gaps, nonconformities, or other issues.
Follow-Up
A subsequent meeting to review the status of previously defined actions, often outlined in an Open Issues List (OIL).
Forklift
A vehicle used to transport materials between production lines and warehouses.
Final Product Audit
A random audit conducted on packaged final products, following guidelines like VDA 6.5.
Green Cross
A visual tool tracking the number of accident-free days at a production site.
Identification
Labeling the status of a product (e.g., finished, semi-finished, non-conforming).
International Material Data System (IMDS)
A system for declaring the chemical composition of delivered products, typically required before approval.
Internal Customer (IC)
An internal stakeholder, such as the next workstation in the production process.
Long-Term Capability
A process performance metric over time, expressed through Cp and Cpk indices.
Material Delivery
The supply of materials to a manufacturing site, often managed using a Kanban system.
Maintenance
The department responsible for the upkeep of production machinery and tools.
Mean Time Between Failure (MTBF)
An indicator measuring the average time between equipment failures.
Mean Time to Repair (MTTR)
An indicator measuring the average time needed to repair equipment.
Measurement
The process of obtaining precise values, such as dimensions, forces, or pressures.
Milestone
A key stage in pre-production planning, often defined by the customer.
Occurrence
A risk analysis indicator, commonly used in PFMEA.
Pareto Diagram
A chart used to prioritize issues and define corrective actions.
Plan-Do-Check-Act Cycle (PDCA)
A continuous improvement process developed by Dr. E. Deming.
Premium Freight
Special, unscheduled transport used for urgent needs, often tracked as a logistics KPI.
Preventive Actions
Steps taken to prevent recurrence of problems, typically defined in Step D7 of the 8D method.
Process Audit (PA)
An assessment of manufacturing processes, conducted during commissioning or production. Examples include VDA 6.3 (VW), Mass Production Audit (Stellantis), and MSA (Ford).
Prototype
A preliminary version of a component used for validation testing, requiring a dedicated control plan.
Quality Policy
A document outlining a company’s quality objectives and mission.
Repair Workstation
A station designated for repairing defective components.
Scrap
Rejected products or materials that fail to meet quality standards.
Shadow Board (SB)
A visual management tool displaying which tools have been removed from their designated places.
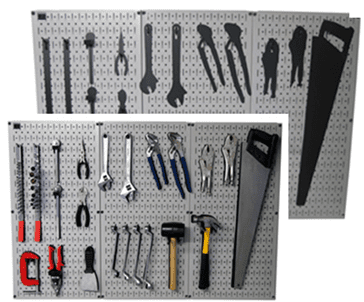
Short-Term Capability
A metric for short-term process performance, expressed by Pp and Ppk indices.
Special Status
An escalation step defined by the customer to address significant issues.
Standardization
The foundation of consistent quality, productivity, and continuous improvement.
Sub-Assembly
A process step involving smaller assemblies before final assembly.
Team Leader
The leader responsible for a production team.
Team Member
A member of a production team.
Timing Chart / Planning
A supplier development schedule aligning with customer milestones.
Traceability
The ability to track a product’s history, especially for addressing customer quality claims.
Value-Added Work (VAW)
Work that directly adds value, excluding activities like inspection or handling.
Variable Data
Data that can be measured and presented as specific values (e.g., dimensions, force, voltage).
👉 Download our free ebook: 200 english terms and abbreviations for Automotive Engineer to further enhance your knowledge!
Author Dariusz Kowalczyk